Wired glass, a seemingly simple material, plays a surprisingly crucial role in our built environment. From enhancing security in commercial buildings to contributing to fire safety in residential homes, wired glass offers a unique blend of functionality and aesthetic appeal. This exploration delves into the diverse types of wired glass, their manufacturing processes, applications, and the key considerations for its use in construction projects.
We’ll examine its strengths and weaknesses compared to other glazing options, providing a complete understanding of this often-overlooked building material.
We will cover everything from the definition and different types of wired glass to its applications in various building types and its role in enhancing security and fire safety. We’ll also discuss maintenance, environmental impact, cost considerations, and a comparison with laminated glass. By the end, you’ll have a solid grasp of wired glass’s potential and limitations.
Wired Glass
Wired glass is a type of safety glass that incorporates a mesh of thin wires within the glass during its manufacturing process. This embedded wire mesh adds significant strength and enhances its fire-resistant properties, making it suitable for various applications where safety is paramount.
Wired Glass Types and Manufacturing Processes
Several types of wired glass exist, each with its own manufacturing process and resulting properties. The most common methods involve embedding a wire mesh into molten glass before it cools and solidifies. The type of wire used, its density, and the overall manufacturing process influence the final product’s characteristics. These variations allow for a range of applications, from simple glazing to more specialized uses.
Properties of Different Wired Glass Types
The properties of wired glass, such as strength, transparency, and fire resistance, vary depending on the type and manufacturing process. While all wired glass offers increased safety compared to standard annealed glass, some types exhibit superior performance in specific areas. For instance, thicker wired glass generally provides greater strength and fire resistance. The transparency can also be affected by the wire mesh density; a denser mesh might slightly reduce clarity.
Type of Wired Glass | Manufacturing Process | Key Properties | Applications |
---|---|---|---|
Standard Wired Glass | Molten glass is poured over a wire mesh, then cooled and annealed. | Increased strength compared to annealed glass, improved fire resistance, relatively high transparency. | Doors, windows in industrial settings, sidelights, partitions. |
Heavy Wired Glass | Similar to standard wired glass, but uses thicker glass and potentially a denser wire mesh. | Higher strength and impact resistance, superior fire resistance, slightly reduced transparency compared to standard wired glass. | High-security applications, fire-rated doors and windows, skylights. |
Specialty Wired Glass (e.g., tempered wired glass) | Combines the wire mesh embedding process with heat treatment (tempering) to enhance strength. | Exceptional strength and impact resistance, improved fire resistance, similar transparency to standard wired glass. | High-impact areas, security glazing, automotive applications (less common now). |
Safety and Security Aspects of Wired Glass
Wired glass, with its embedded wire mesh, offers a significant boost to building safety and security compared to standard annealed glass. Its enhanced properties make it a valuable material in various applications, particularly where safety and security are paramount. This section will delve into the specific ways wired glass contributes to both fire safety and security against intrusions.
Wired Glass and Enhanced Building Security
The primary security benefit of wired glass lies in its resistance to shattering. While it can still break under significant impact, the embedded wire mesh holds the fragments together, preventing them from dispersing and causing injury. This significantly reduces the risk of intrusion through windows or doors fitted with wired glass, acting as a deterrent and delaying any potential break-in.
The resulting delay provides valuable time for emergency response or for occupants to react to the situation. This is especially important in commercial buildings, where security is a major concern, and in residential settings where increased protection against intruders is desired.
Wired Glass and Fire Safety
Wired glass plays a crucial role in fire safety by limiting the spread of flames and smoke. The wire mesh embedded within the glass strengthens the pane and increases its resistance to heat. This prevents the glass from shattering easily during a fire, which would otherwise create openings for flames and smoke to spread more rapidly. Furthermore, the integrity of the glass pane is maintained for a longer period, helping to contain the fire and provide a safe escape route for occupants.
Building codes often mandate the use of wired glass in specific locations, such as fire-rated doors and windows, to enhance overall fire safety.
Standards and Regulations Governing Wired Glass
The use of wired glass in construction is subject to various standards and regulations that vary by region and jurisdiction. These regulations often specify the type of wire mesh, the glass thickness, and the performance requirements for fire resistance and impact resistance. For example, in many areas, building codes stipulate the use of wired glass in fire-rated assemblies to meet specific fire-resistance ratings.
Compliance with these standards is crucial to ensure that the wired glass used meets the required safety and security levels. Consulting local building codes and relevant safety standards is essential before specifying and installing wired glass in any construction project.
Comparative Performance of Wired Glass in a Security Breach Scenario
Consider a scenario where a retail store experiences a break-in attempt. One window is fitted with standard annealed glass, while another uses wired glass. In the case of the annealed glass window, a forceful impact, such as a thrown object or a ram attack, would likely shatter the glass completely, creating a large opening for the intruder to enter.
The shattered glass would also pose a significant risk of injury. In contrast, the wired glass window, while potentially cracking, would retain its structural integrity to a much greater extent. The wire mesh would hold the fragments together, hindering the intruder’s access and delaying their entry. This delay would likely trigger alarms and provide valuable time for security personnel to respond, or for the occupants to take action.
This scenario clearly demonstrates the superior security performance of wired glass compared to standard annealed glass in such a situation.
Applications of Wired Glass in Construction
Wired glass, with its inherent strength and safety features, finds a wide range of applications in the construction industry. Its ability to resist shattering, while still allowing for light transmission, makes it a valuable material for various architectural designs, both in commercial and residential settings. The choice of using wired glass often depends on the specific needs of the building and the desired level of security and safety.
The use of wired glass in construction projects balances the need for transparency with safety requirements. It offers a cost-effective solution compared to other safety glass options, particularly in applications where high impact resistance isn’t paramount. However, its limitations in terms of impact resistance and potential for sharp fragments upon breakage should be carefully considered during the design phase.
Common Architectural Applications of Wired Glass
Wired glass is frequently used in a variety of architectural elements. It is a common sight in sidelights flanking entry doors, providing both visual appeal and a degree of security. It’s also used in windows, especially in areas where impact resistance is less critical, such as upper-story windows or interior partitions. Furthermore, it finds application in skylights and other translucent roofing elements, offering a balance between natural light and safety.
Finally, wired glass can be incorporated into decorative elements like glass block partitions or feature walls.
Wired Glass in Commercial Buildings
In commercial settings, wired glass serves multiple purposes. Its use in doors and windows contributes to security, hindering unauthorized entry. It’s often specified in partitions separating office spaces, allowing light penetration while maintaining visual privacy. Larger commercial buildings may utilize wired glass in fire-rated assemblies, though tempered or laminated glass are often preferred for higher levels of fire protection.
The cost-effectiveness of wired glass makes it an attractive option for applications where the risk of high-impact damage is relatively low. For example, a large office building might use wired glass in internal partitions or less vulnerable exterior windows, reserving more impact-resistant glass for ground-level windows or entrances.
Wired Glass in Residential Buildings
Residential applications of wired glass frequently involve doors and windows, primarily for security purposes. It’s commonly found in sidelights next to exterior doors, enhancing security without obstructing natural light. Similar to commercial applications, its use in interior partitions can help define spaces while maintaining visual openness. However, the growing preference for enhanced safety and energy efficiency often leads homeowners to opt for laminated or tempered glass in areas prone to impact, such as ground floor windows or sliding glass doors.
Wired glass remains a viable option for less vulnerable areas like upper-story windows or interior doors.
Advantages and Disadvantages of Wired Glass in Different Settings
The advantages and disadvantages of wired glass are context-dependent. In doors, it offers a degree of security and visual appeal, but its relatively low impact resistance might be a concern in high-traffic areas or locations prone to vandalism. In windows, wired glass provides a balance between light transmission and safety, but its limitations in impact resistance might necessitate its use in less vulnerable areas.
In partitions, it offers visual separation while maintaining some light penetration, but its lack of sound insulation compared to other materials could be a drawback.
Building Types Frequently Using Wired Glass
The choice of glazing material is influenced by factors like budget, security needs, and building codes. Wired glass, while offering a balance between cost and safety, is often seen in specific building types.
- Older Buildings: Many older buildings incorporate wired glass due to its historical prevalence and relative affordability. Replacing it with more modern alternatives can be costly.
- Low-Security Applications: Buildings with less stringent security requirements, such as smaller retail spaces or residential buildings in low-crime areas, might utilize wired glass to maintain transparency without significant security concerns.
- Interior Partitions: Wired glass is frequently chosen for internal partitions, balancing privacy with light transmission and cost-effectiveness. The risk of impact is lower in these settings.
- Industrial Buildings (certain areas): In some industrial settings, wired glass might be used in upper-story windows or less vulnerable areas where high impact resistance isn’t crucial, and cost is a major factor.
Maintenance and Care of Wired Glass
Wired glass, while durable, requires proper care to maintain its integrity and extend its lifespan. Regular cleaning and prompt attention to damage are crucial for ensuring both safety and aesthetic appeal. Neglecting maintenance can lead to premature deterioration and compromise the security features of the glass.
Proper Cleaning and Maintenance Procedures
Cleaning wired glass is similar to cleaning other types of glass, but requires a gentler approach to avoid scratching the wire mesh embedded within. Avoid abrasive cleaners and scouring pads, as these can damage the surface and the wire mesh, potentially weakening the glass. A simple solution of warm water and mild dish soap, applied with a soft sponge or cloth, is generally sufficient.
Rinse thoroughly with clean water and dry with a lint-free cloth to prevent streaking. For stubborn dirt or grime, a glass cleaner specifically designed for delicate surfaces can be used, but always test it in an inconspicuous area first. Regular cleaning, ideally every few months or as needed, will help prevent the buildup of dirt and grime that can obscure visibility and potentially weaken the glass over time.
Identifying and Addressing Common Damage
Common damage to wired glass includes cracks, chips, and broken wires. Cracks, even small ones, can significantly weaken the glass and should be addressed immediately. Chips, particularly around the edges, can create stress points that lead to further damage. Broken wires compromise the glass’s strength and security features. Inspect your wired glass regularly for any signs of damage.
If any damage is found, it’s crucial to replace the pane immediately. Delaying repairs increases the risk of further damage and potential injury. Small chips might be temporarily mitigated with clear epoxy resin, carefully applied to prevent further cracking. However, this is a temporary solution and professional replacement is always recommended.
Lifespan and Replacement Considerations
The lifespan of wired glass varies depending on factors such as its thickness, the quality of the wire mesh, environmental conditions, and the level of maintenance. Generally, wired glass can last for many years, sometimes decades, if properly maintained. However, exposure to extreme temperatures, harsh weather conditions, or impacts can significantly reduce its lifespan. Regular inspection is vital.
If significant damage is observed, or if the glass shows signs of significant deterioration (such as extensive rusting of the wire mesh), replacement is necessary to maintain safety and security. Consider replacing wired glass in areas prone to impact, such as doorways and lower windows, more frequently than in less vulnerable locations. The cost of replacement should be weighed against the potential risks associated with using damaged glass.
Safe Replacement of a Damaged Pane of Wired Glass
Replacing a pane of wired glass requires caution and, ideally, professional assistance. Improper handling can lead to injury.
- Safety First: Wear safety glasses and gloves to protect yourself from sharp edges and potential cuts.
- Preparation: Carefully remove any surrounding trim or frames to access the damaged pane. Take pictures or make notes of how the pieces fit together for reassembly.
- Removal: Gently remove the damaged pane. If it’s stuck, use a putty knife to carefully loosen it from the frame, working slowly and steadily to avoid breakage.
- Measurement: Accurately measure the opening to ensure the replacement pane fits perfectly.
- Installation: Carefully insert the new pane into the opening. Use appropriate sealant (typically glazing compound) to secure the pane in place and ensure a watertight seal. Allow the sealant to cure completely before reinstalling the trim or frame.
- Cleanup: Clean up any excess sealant and debris.
Environmental Impact and Sustainability
Wired glass, while offering crucial safety and security benefits, carries an environmental footprint throughout its lifecycle, from raw material extraction to disposal. Understanding this impact is crucial for responsible building design and material selection. This section examines the environmental considerations associated with wired glass and explores its sustainability compared to alternatives.The manufacturing process of wired glass involves the melting of glass components, often using significant energy resources.
The incorporation of the wire mesh adds another layer of energy consumption and material usage. Disposal presents further challenges, as wired glass is not easily recyclable in standard glass streams due to the embedded metal mesh. This often leads to its disposal in landfills, contributing to waste accumulation and potential environmental contamination.
Manufacturing and Disposal Impacts
The environmental impact of wired glass manufacturing stems primarily from energy consumption in the glass melting process and the use of raw materials. The production of soda-lime glass, a common base for wired glass, requires significant energy input, typically from fossil fuels, resulting in greenhouse gas emissions. Furthermore, the mining and processing of silica sand, a key component, can lead to habitat disruption and dust pollution.
The addition of the wire mesh increases the overall material and energy input, exacerbating the environmental footprint. Disposal often involves sending the glass to landfills, contributing to land usage and potential leaching of harmful substances into the surrounding environment. In contrast, some alternatives like laminated glass might offer slightly better environmental profiles due to potentially simpler recycling processes, though their manufacturing still consumes energy.
Comparison with Alternative Glazing Materials
Compared to other glazing materials, wired glass’s sustainability profile is a complex issue. Laminated glass, for example, may offer better impact resistance and potentially simpler recycling options (though the interlayer material can present challenges). However, laminated glass manufacturing also requires significant energy input. Tempered glass boasts superior strength but shares a similar energy-intensive manufacturing process. The choice between these materials often hinges on a balancing act between performance requirements, cost, and environmental impact, requiring a life-cycle assessment to accurately compare.
For example, a building might opt for laminated glass in areas requiring high impact resistance, while using wired glass in less critical zones, minimizing the overall environmental impact of the glazing system.
Recycling Options for Wired Glass
Currently, recycling wired glass presents significant challenges. The presence of the embedded wire mesh makes it incompatible with standard glass recycling streams. Most often, wired glass ends up in landfills. However, some specialized recycling facilities may exist that can process wired glass, separating the glass and metal components for individual recycling. These facilities are, however, relatively rare, and the economics of such recycling remain a significant barrier to widespread adoption.
Research and development are needed to improve the recyclability of wired glass, potentially through the development of new materials or processing techniques. Promoting the use of such specialized recycling facilities is crucial for diverting wired glass from landfills and reducing its environmental impact.
Wired Glass and Building Sustainability Ratings
The choice of wired glass can influence a building’s overall sustainability rating, although it’s not the sole determining factor. Building certification systems like LEED (Leadership in Energy and Environmental Design) consider various aspects of material selection, including embodied energy, recyclability, and potential for reuse. While wired glass might not score as highly as some alternative materials in terms of recyclability, its use in specific applications (e.g., security glazing) can contribute to the building’s overall performance in terms of safety and longevity, indirectly impacting the sustainability rating.
A comprehensive life-cycle assessment should be conducted to evaluate the overall environmental impact of the building’s glazing system, considering factors beyond just the material choice itself, such as energy efficiency and overall building design.
Cost and Pricing of Wired Glass
The cost of wired glass, like any building material, is subject to a variety of factors. Understanding these factors allows for better budgeting and informed decision-making during a construction or renovation project. Pricing varies depending on several key elements, impacting both the material cost and the overall installation expense.
Factors Influencing Wired Glass Pricing
Several interconnected factors influence the final price of wired glass. Thickness is a primary determinant; thicker glass, offering greater strength and security, naturally commands a higher price. The size of the glass panes also plays a significant role; larger sheets require more material and often incur higher handling and transportation costs. The type of wire mesh embedded within the glass affects the price; more robust or specialized wire types will increase the cost.
Finally, the supplier and geographic location significantly impact pricing, as transportation and regional market demands fluctuate. Specialized coatings or treatments applied to the wired glass, such as those enhancing energy efficiency or sound insulation, will also add to the expense.
Comparison with Other Glazing Options
Wired glass sits competitively within the broader glazing market. While often more expensive than standard annealed glass, it’s generally less costly than laminated or tempered glass, particularly for applications where the high impact resistance of tempered glass isn’t strictly required. Compared to other security glazing options like polycarbonate, wired glass usually presents a more economical choice, although polycarbonate might offer superior impact resistance in specific scenarios.
The choice ultimately depends on the project’s specific safety and security needs and budget constraints.
Factors Impacting Overall Installation Cost
The installation cost of wired glass extends beyond the material price itself. Labor costs, influenced by factors such as the complexity of the installation (e.g., intricate cuts or unusual shapes), the height of the installation, and the installer’s experience, represent a significant portion of the total cost. Transportation costs for delivering the glass to the site and any necessary equipment rentals can also add to the expense.
Furthermore, the need for additional framing or support structures might increase the overall installation budget. Finally, any required permits or inspections will add to the project’s overall cost.
Sample Cost Estimate for a Small-Scale Project
Let’s consider a hypothetical project: installing wired glass in a small storefront window measuring 4 feet by 6 feet. We’ll assume the use of standard 1/4-inch thick wired glass.
Item | Quantity | Unit Cost | Total Cost |
---|---|---|---|
Wired Glass (4ft x 6ft) | 1 | $50 | $50 |
Installation Labor | 1 | $100 | $100 |
Transportation | 1 | $25 | $25 |
Total Estimated Cost | $175 |
This estimate is a simplified example and doesn’t include potential additional costs such as disposal fees for old glass or unforeseen complications during installation. Actual costs will vary depending on the specific project details and location. It is crucial to obtain multiple quotes from reputable installers to ensure a competitive and accurate cost assessment.
Wired Glass vs. Laminated Glass
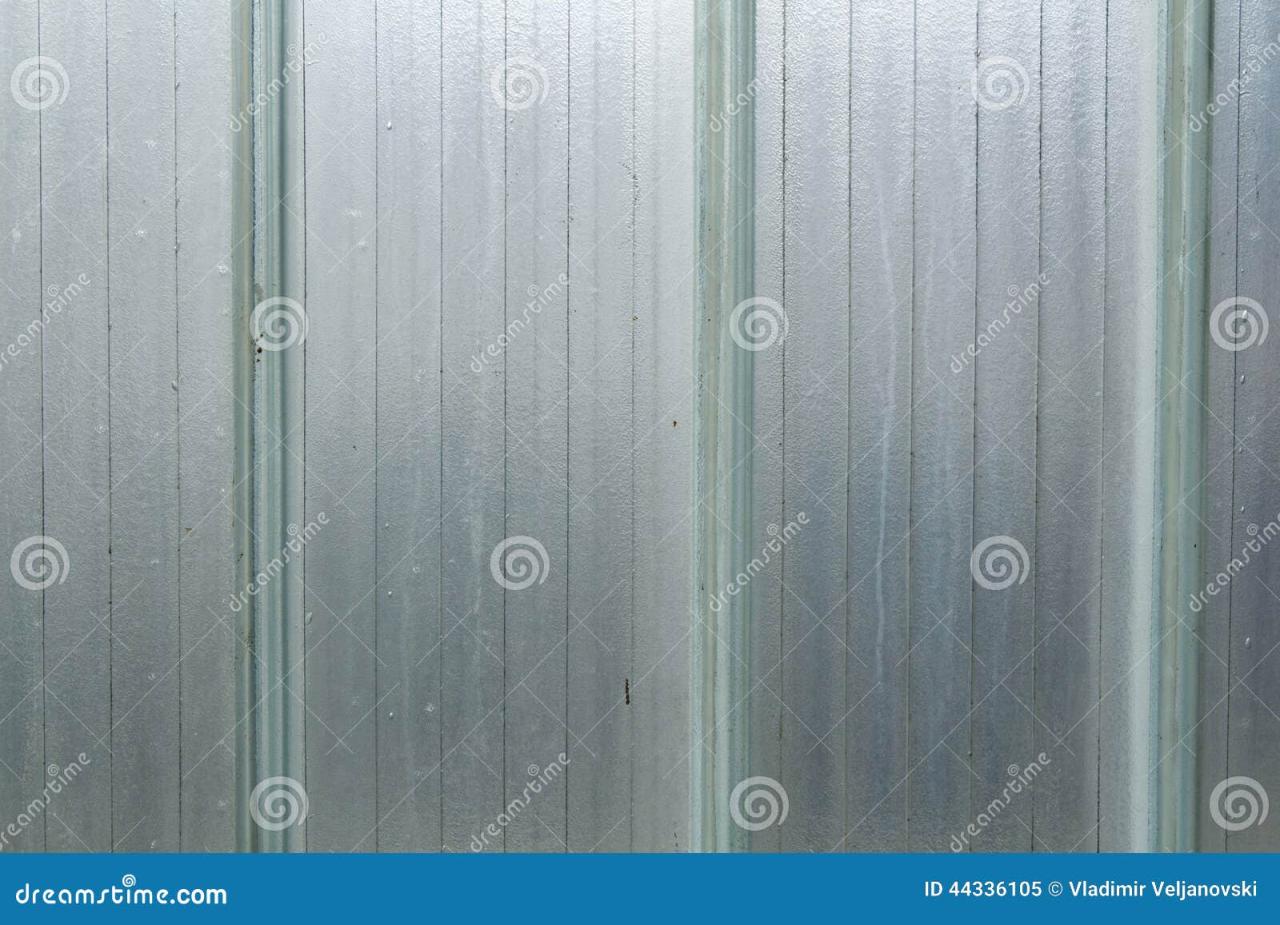
Source: dreamstime.com
Choosing between wired glass and laminated glass depends heavily on the specific needs of a project. Both offer safety and security features, but their strengths lie in different areas. Understanding their key differences is crucial for making an informed decision.
Wired glass and laminated glass are both used in construction to enhance safety and security, but they achieve this through different methods and offer distinct advantages and disadvantages. While wired glass is a more traditional solution, laminated glass has become increasingly popular due to advancements in manufacturing and its superior performance in certain applications.
Safety and Security Properties
Wired glass, as its name suggests, incorporates a wire mesh embedded within the glass during manufacturing. This mesh helps hold the glass together if it breaks, preventing large shards from scattering. This offers a degree of protection against injury, but it’s important to note that the glass itself still shatters. Laminated glass, on the other hand, consists of two or more layers of glass bonded together with a layer of polyvinyl butyral (PVB) interlayer.
This interlayer is what provides the enhanced safety features. When broken, the glass fragments adhere to the PVB, significantly reducing the risk of sharp shards and providing greater protection against intrusion.
Suitable Applications
The choice between wired and laminated glass often hinges on the intended application. Wired glass, due to its lower cost, is frequently used in applications where high-impact resistance isn’t critical, such as sidelights, obscure glazing in doors, and certain types of skylights. Its use in areas requiring high security is less common due to its susceptibility to shattering. Laminated glass, however, finds applications in situations demanding higher safety and security standards.
This includes automotive windshields, security glazing in high-risk areas, and architectural applications where impact resistance is paramount, such as hurricane-prone regions.
Cost Comparison
Generally, wired glass is less expensive than laminated glass. This cost difference stems from the simpler manufacturing process of wired glass. The added complexity and materials used in creating the PVB interlayer in laminated glass contribute to its higher price point. However, the long-term cost-effectiveness of each type should be considered. While the initial investment in laminated glass is higher, its superior safety and security features may translate to lower insurance premiums or reduced repair costs in the long run.
Advantages and Disadvantages
A direct comparison highlighting the benefits and drawbacks of each glass type is essential for making the right choice. The following lists summarize the key points:
- Wired Glass: Advantages
- Lower initial cost
- Relatively easy to install
- Provides some degree of shatter resistance
- Wired Glass: Disadvantages
- Shatters into sharp fragments upon impact
- Offers limited security against intrusion
- Lower impact resistance compared to laminated glass
- Laminated Glass: Advantages
- Superior impact resistance
- Holds together upon breakage, minimizing sharp fragments
- Enhanced security against intrusion
- Offers better sound insulation
- Laminated Glass: Disadvantages
- Higher initial cost
- More complex installation process
- Can be more difficult to cut and fabricate
Closing Notes
From its humble beginnings to its modern applications, wired glass continues to be a relevant and versatile material in construction. Understanding its properties, limitations, and appropriate applications is key to utilizing it effectively. While alternatives exist, wired glass retains a significant place in the market, offering a balance of safety, security, and cost-effectiveness in many situations. Choosing the right type of glass for a specific project requires careful consideration of the intended use and the overall design goals.
Hopefully, this guide has provided the necessary insights to make informed decisions.
Essential Questionnaire
Can wired glass be cut?
Yes, but it’s more difficult and requires specialized tools due to the embedded wire mesh. It’s best left to professionals.
Is wired glass recyclable?
Yes, but recycling processes vary depending on location and the type of glass. Check with local recycling facilities.
How does the wire mesh affect the glass’s transparency?
The wire mesh reduces transparency slightly, though the extent varies depending on the wire thickness and spacing. It’s generally still suitable for many applications.
What are the common causes of wired glass failure?
Common causes include impact damage, thermal stress (sudden temperature changes), and improper installation.
How long does wired glass typically last?
With proper maintenance, wired glass can last for many years, but its lifespan depends on factors like exposure to the elements and the level of stress it experiences.