Optical Glass, a material seemingly simple in its name, unveils a world of intricate complexity. From the precise crafting of lenses that shape our view of the cosmos to the delicate fibers carrying information across continents, optical glass underpins countless technologies. Its properties, determined by careful manipulation of chemical composition and manufacturing processes, dictate its performance across a wide spectrum of applications, each demanding specific optical characteristics.
This exploration delves into the fascinating world of optical glass, examining its various types, manufacturing techniques, optical properties, testing methods, future trends, and environmental considerations. We’ll uncover the secrets behind its creation, from the melting of raw materials to the precise polishing that brings its potential to life.
Types of Optical Glass
Optical glass is categorized based on its refractive index (n d) and Abbe number (ν d), which dictate its ability to bend light and its dispersion characteristics, respectively. These properties determine how well the glass focuses light and minimizes chromatic aberration, a crucial factor in the performance of optical systems. The choice of glass type depends heavily on the specific application, demanding a careful consideration of these optical properties and their impact on image quality.
Crown Glass and Flint Glass: A Comparison
Crown and flint glasses represent the two fundamental types of optical glass. They differ significantly in their chemical compositions and resulting optical properties. Crown glasses generally have lower refractive indices and higher Abbe numbers compared to flint glasses. This means crown glasses bend light less and exhibit less dispersion.
Property | Crown Glass | Flint Glass |
---|---|---|
Refractive Index (nd) | Typically 1.50 – 1.60 | Typically 1.55 – 2.00 |
Abbe Number (νd) | Typically 50 – 65 | Typically 20 – 40 |
Chemical Composition | Primarily silica (SiO2) with additions of alkali and alkaline earth oxides (e.g., potassium, sodium, calcium oxides) | Primarily silica with significant additions of lead oxide (PbO) and other heavy metal oxides (e.g., barium, zinc oxides). |
Optical Properties | Low dispersion, low refractive index | High dispersion, high refractive index |
Typical Applications | Lenses in cameras, telescopes, eyeglasses | High-index lenses, prisms, and other optical components where high refractive power is needed. |
Classification of Optical Glass by Refractive Index and Abbe Number
A more detailed classification involves plotting the refractive index against the Abbe number. This creates a diagram where different glass types occupy distinct regions. While the exact boundaries can vary slightly depending on the manufacturer, this provides a useful framework for understanding the relationships between these key properties.
Type | Refractive Index (nd) | Abbe Number (νd) | Typical Applications |
---|---|---|---|
Crown Glass (e.g., BK7) | ~1.517 | ~64 | General purpose lenses, windows, prisms |
Flint Glass (e.g., SF11) | ~1.78 | ~25 | High-index lenses, prisms, achromatic doublets |
Fluoride Crown Glass (e.g., CAF2) | ~1.434 | ~95 | UV optics, high-precision lenses |
Phosphate Glass | Variable, often higher than crown glass | Variable, often lower than crown glass | High-refractive-index lenses, optical fibers |
Specialty Optical Glasses
Beyond crown and flint glasses, a range of specialty glasses cater to specific needs. These glasses often incorporate unusual elements to achieve unique optical or physical properties.Phosphate glasses, for instance, use phosphorus pentoxide (P 2O 5) as a primary glass former, resulting in glasses with high refractive indices and relatively low Abbe numbers. They find use in high-index lenses and fiber optics.
Fluoride glasses, using fluorides as primary components, possess exceptionally low refractive indices and high Abbe numbers, making them suitable for applications requiring minimal dispersion and transmission in the ultraviolet (UV) spectrum. Chalcogenide glasses, containing chalcogen elements like sulfur or selenium, exhibit high refractive indices and transmit infrared (IR) radiation, finding applications in IR optics and sensors. The choice among these specialty glasses depends heavily on the specific wavelength range and desired optical properties.
Manufacturing Process of Optical Glass
Creating high-quality optical glass involves a meticulous process demanding precise control over every stage, from raw material selection to final polishing. The purity and homogeneity of the finished product directly impact its optical performance, making each step crucial.
The manufacturing process begins with the careful selection and preparation of raw materials, primarily silica sand, along with other oxides like boric oxide, alumina, and various metal oxides, depending on the desired refractive index and dispersion properties. These materials are weighed precisely according to the specific glass formulation, ensuring consistent results. Impurities are carefully controlled as even minute amounts can significantly affect the optical quality of the final product.
Melting and Refining
The precisely weighed batch of raw materials is then fed into a high-temperature furnace, typically an electric melting furnace, where temperatures reach 1500°C or more. The melting process transforms the raw materials into a molten glass mass. This molten glass undergoes refining to remove bubbles and other imperfections. Techniques such as bubbling with inert gases (like nitrogen or argon) help to remove bubbles, while fining agents are sometimes added to accelerate the process.
The entire process requires precise temperature control and careful monitoring to ensure the resulting glass is free from defects and exhibits a high degree of homogeneity.
Shaping Optical Glass
Once the molten glass is refined, it’s ready to be shaped into the desired form. Several methods exist, each suited to different applications and desired shapes.
Molding involves pouring the molten glass into a pre-heated mold of the desired shape. This is commonly used for mass production of simple shapes like lenses or prisms. The mold’s material and temperature are carefully controlled to ensure the glass conforms to the desired shape and cools uniformly. Pressing is a similar method, where a plunger forces the molten glass into a mold.
This method offers better control over the final shape and is often used for more complex components. Grinding and Polishing are used for creating precise shapes and surfaces, often after an initial shaping process. This involves using progressively finer abrasives to remove material and achieve the desired surface finish. The final polishing step uses very fine abrasives or polishing compounds to produce a highly smooth and precise surface, crucial for optical applications.
Precision is paramount here; even minute imperfections can scatter light and degrade the optical performance.
Annealing
After shaping, the glass undergoes annealing, a controlled cooling process designed to reduce internal stresses that can arise during manufacturing. These stresses can lead to birefringence (double refraction) and distortion, significantly affecting the optical quality. The annealing process involves slowly cooling the glass over a specific temperature range, allowing the stresses to relax. The precise temperature profile and cooling rate are critical and vary depending on the glass type and shape.
Improper annealing can lead to cracks or internal stresses, rendering the glass unusable for optical applications. A properly annealed piece of optical glass will have significantly improved stability and durability.
Flowchart of the Optical Glass Manufacturing Process
The following describes a simplified flowchart of the process:
Raw Material Preparation → Melting & Refining → Shaping (Molding, Pressing, Grinding/Polishing) → Annealing → Inspection & Quality Control → Finished Optical Glass
Optical Properties and Applications
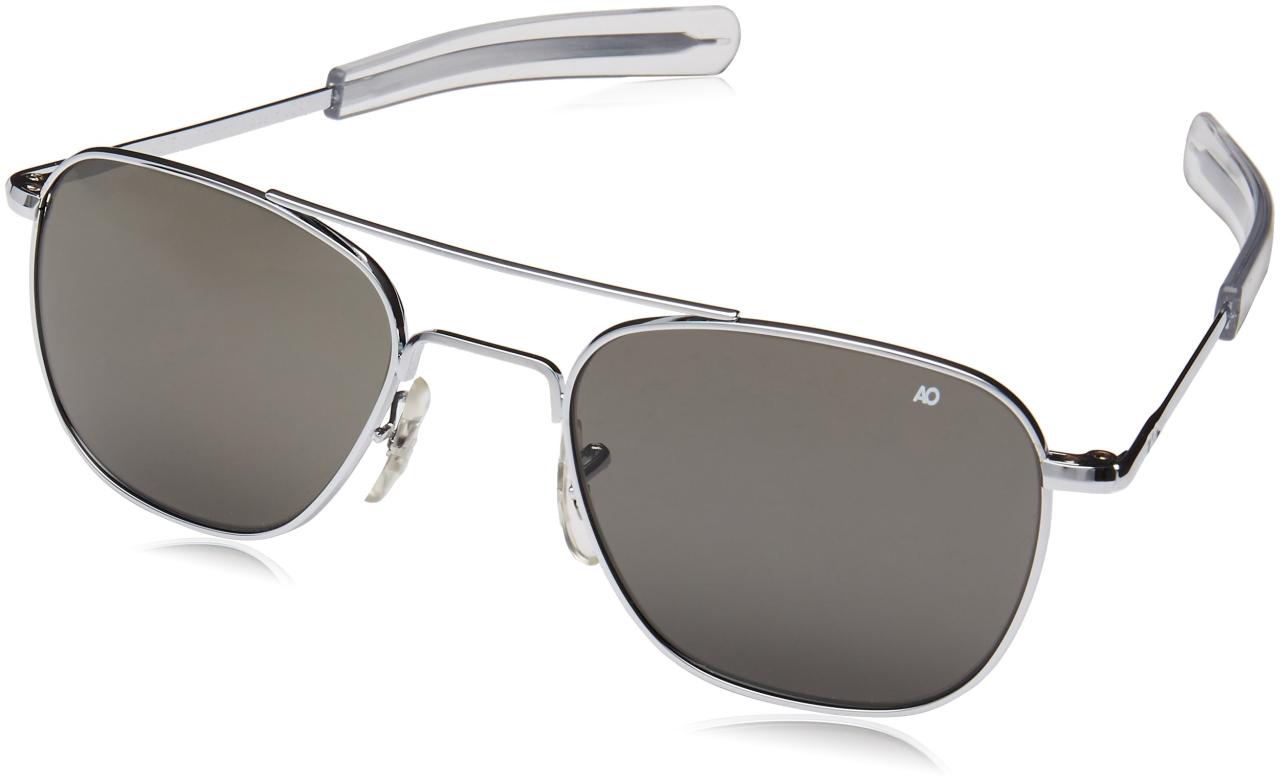
Source: media-amazon.com
Optical glass, with its precisely controlled composition, exhibits a range of optical properties crucial for its diverse applications. Understanding these properties, particularly the interplay between refractive index, Abbe number, and dispersion, is key to selecting the appropriate glass for a specific optical system.The refractive index (n) measures how much light bends when passing from air into the glass. A higher refractive index indicates greater bending.
The Abbe number (ν) quantifies the glass’s dispersion – its ability to separate different wavelengths of light. A higher Abbe number signifies lower dispersion, meaning less color fringing. Dispersion, essentially the change in refractive index with wavelength, is inversely related to the Abbe number. These three properties are intrinsically linked and are critical factors in designing optical systems to minimize aberrations and achieve high image quality.
For instance, a lens designed for high magnification might require a glass with a high refractive index to achieve a short focal length, but a high Abbe number is also necessary to minimize chromatic aberration.
Optical glass, known for its precise refractive properties, is crucial in various applications. However, for extreme scratch resistance, a different material often takes center stage: check out the properties of Sapphire Glass for a comparison. Ultimately, the choice between optical glass and sapphire depends heavily on the specific needs of the application, balancing optical clarity with durability.
Relationship Between Refractive Index, Abbe Number, and Dispersion
The relationship between refractive index (n), Abbe number (ν), and dispersion is expressed mathematically and graphically through dispersion curves. These curves plot the refractive index against wavelength for a specific glass type. The slope of the curve represents the dispersion. A steeper slope indicates higher dispersion, while a flatter slope indicates lower dispersion, corresponding to a higher Abbe number.
The specific values of n and ν are crucial in designing optical systems to minimize chromatic aberration, a common lens defect causing colored fringes around objects. The selection of glasses with appropriate n and ν values allows designers to compensate for this aberration, leading to sharper and more accurate images.
Examples of Optical Glass Applications
Different optical glasses are tailored for specific applications based on their optical properties and other factors like durability and cost.
- Camera Lenses: High-refractive-index glasses are often used in camera lenses to reduce the number of elements needed, making the lens smaller and lighter. Glasses with low dispersion are crucial for minimizing chromatic aberration and ensuring sharp images across the visible spectrum.
- Telescope Lenses and Mirrors: Telescopes require glasses with extremely low dispersion and high transmission in the visible and near-infrared regions to achieve high resolution and clarity in astronomical observations. Large telescope mirrors are often made from low-expansion glasses to maintain their shape under varying temperatures.
- Microscope Objectives: Microscope objectives demand high-refractive-index glasses to achieve high numerical aperture, allowing for better resolution and magnification. These glasses must also have excellent transmission properties in the visible spectrum.
- Optical Fibers: Optical fibers utilize high-purity silica glass with a precisely controlled refractive index profile to guide light signals over long distances with minimal loss. The core and cladding layers have slightly different refractive indices, enabling total internal reflection.
- Prisms: Prisms, used for dispersing light into its constituent wavelengths or for beam deflection, are typically made from glasses with specific refractive indices and Abbe numbers to optimize their performance for a given application (e.g., spectroscopy or beam steering).
Comparison of Optical Glass Performance in Applications
Glass Type | Application | Advantages | Disadvantages |
---|---|---|---|
BK7 (Borosilicate Crown Glass) | Camera lenses, general-purpose optics | Good transmission, relatively low cost, readily available | Moderate dispersion, not ideal for high-precision applications |
Fused Silica | High-precision optics, UV applications | Excellent transmission across a wide wavelength range, very low thermal expansion | High cost, difficult to process |
SF11 (Dense Flint Glass) | High-index lenses, microscope objectives | High refractive index, allows for compact designs | High dispersion, susceptible to chromatic aberration if not carefully managed |
LaSFN9 (Lanthanum Crown Glass) | High-resolution imaging systems | High refractive index, low dispersion | Higher cost than BK7 |
Testing and Quality Control
Ensuring the quality of optical glass is paramount for its successful application in various optical instruments. Rigorous testing and quality control measures are implemented throughout the manufacturing process to guarantee the glass meets the stringent requirements of its intended use. These measures cover a range of properties, from basic optical characteristics to more subtle aspects like homogeneity and internal structure.Precise measurement of optical properties is crucial.
This involves sophisticated techniques and equipment designed to deliver highly accurate results. The quality control process doesn’t simply check the final product; it’s a continuous process that monitors every stage of production, from raw materials to finished lenses.
Refractive Index and Abbe Number Measurement
The refractive index and Abbe number are fundamental optical properties of glass. The refractive index (n) describes how much light slows down when passing through the material, while the Abbe number (ν) indicates the material’s dispersion, or how much the refractive index varies with wavelength. These parameters are typically measured using a precision refractometer. This instrument uses the principle of total internal reflection to determine the refractive index at specific wavelengths, usually the sodium D-line (589.3 nm) and the hydrogen F-line (486.1 nm) and C-line (656.3 nm).
The Abbe number is then calculated from these measurements using a standard formula. The accuracy of these measurements directly impacts the performance of the final optical component. For example, slight variations in refractive index can lead to significant aberrations in lenses, blurring the image.
Homogeneity and Internal Quality Assessment
The homogeneity and internal quality of optical glass are assessed using various non-destructive testing methods. These methods are critical because even microscopic imperfections can significantly affect the performance of optical components, especially in high-precision applications.One common technique is visual inspection under magnification, often using polarized light. This helps identify inhomogeneities, such as striae (streaks of different refractive index) and bubbles.
Optical glass, known for its precision and clarity, is used in a variety of applications, from lenses to scientific instruments. A related concept, though with different properties, is Low-E Glass (Low Emissivity Glass) , which focuses on controlling heat transfer. Understanding the distinctions between these glass types is crucial for selecting the right material for specific needs, especially when considering energy efficiency and optical performance.
Optical glass, therefore, maintains its importance in specialized fields.
Other methods include ultrasonic testing, which detects internal flaws by measuring the transmission and reflection of ultrasonic waves, and scattering measurements, which quantify the amount of light scattered by internal imperfections. Laser interferometry provides a highly sensitive way to measure the surface quality and refractive index variations within the glass. These techniques help ensure the glass is free from defects that could compromise its optical performance.
Optical glass, prized for its clarity and precision in lenses and prisms, differs significantly in composition from other types of glass. For instance, it’s quite unlike the heavier, more lustrous Lead Glass / Lead Crystal , which is known for its brilliance and often used in decorative items. The absence of lead oxide in optical glass ensures its superior optical properties, making it ideal for scientific and technical applications.
Quality Control Measures Throughout Manufacturing
Maintaining consistent quality requires a multi-faceted approach implemented at every stage of production.
- Raw Material Inspection: Thorough inspection of the raw materials (e.g., silica sand, oxides) is crucial to ensure they meet the required purity and chemical composition.
- Melting Process Monitoring: Temperature and atmosphere are carefully controlled during the melting process to prevent the formation of bubbles or other defects.
- Homogenization Control: Stirring and other techniques are used to ensure the molten glass is thoroughly mixed and homogenous before forming.
- Forming and Annealing Control: Precise control of temperature and cooling rates during forming and annealing minimizes internal stress and ensures dimensional stability.
- In-Process Inspection: Samples are taken at various stages of production for testing and quality assessment.
- Final Inspection and Testing: Every finished piece of optical glass undergoes a rigorous final inspection, including measurements of refractive index, Abbe number, and other optical properties, as well as assessments of homogeneity and surface quality.
- Statistical Process Control (SPC): Statistical methods are used to monitor and control the manufacturing process, identifying and correcting any deviations from established standards.
Future Trends and Developments: Optical Glass
The field of optical glass is constantly evolving, driven by the increasing demands of advanced technologies. New materials and manufacturing techniques are continuously being developed to create optical glasses with superior properties, enabling groundbreaking applications in various sectors. This section will explore some key trends and their potential impact.The development of new optical glasses focuses on enhancing existing properties and introducing entirely new functionalities.
This involves optimizing existing glass compositions and exploring novel materials to achieve superior performance across various parameters. For instance, there’s a significant push towards creating glasses with higher refractive indices, lower dispersion, and improved resistance to environmental factors like radiation and temperature fluctuations. This improvement in properties is directly linked to advancements in material science and precise manufacturing processes.
Improved Optical Properties and Novel Glass Compositions
Researchers are actively exploring new glass compositions incorporating rare-earth elements and other advanced materials to achieve specific optical properties. For example, the development of chalcogenide glasses offers the potential for applications in mid-infrared optics, expanding the possibilities for sensing and imaging technologies. Similarly, the exploration of fluoride glasses enables the creation of lenses and optical components with extremely low dispersion, crucial for high-resolution imaging systems.
These advancements often involve complex synthesis methods and careful control of the manufacturing process to ensure the desired properties are consistently achieved. One example of this is the ongoing research into the use of phosphate glasses, which offer unique properties for specific applications, such as high refractive index and low thermal expansion.
Applications in Photonics and Optoelectronics
Novel optical glasses are playing an increasingly vital role in photonics and optoelectronics. High-index glasses are essential for miniaturizing optical components in integrated photonic circuits, leading to more compact and efficient devices. The development of glasses with tailored nonlinear optical properties is crucial for applications such as optical switching and frequency conversion. Furthermore, the use of optical glasses in high-power laser systems requires the development of glasses with exceptional damage thresholds and thermal stability.
For instance, the development of new glasses with improved resistance to laser-induced damage is crucial for the advancement of high-power laser systems used in various industrial and scientific applications, including laser surgery and material processing. The potential of these advancements is vast, promising smaller, faster, and more energy-efficient optical devices.
Challenges and Opportunities in Optical Glass R&D
Despite the significant progress, several challenges remain in the field of optical glass research and development. The synthesis of novel glasses often involves complex and expensive processes. Moreover, ensuring the reproducibility and scalability of these processes for mass production presents a significant hurdle. Further challenges include the need for improved characterization techniques to accurately assess the optical and physical properties of these advanced glasses.
Optical glass, known for its precise refractive properties, is used in a variety of applications, from high-quality lenses to scientific instruments. Interestingly, the principles of controlling light transmission are also relevant to the construction of energy-efficient windows; you can learn more about this by checking out information on Insulated Glass / Double Glazed Glass , which often incorporates specialized coatings to improve insulation.
Ultimately, both optical glass and insulated glass rely on precise manipulation of light and heat transfer for optimal performance.
However, the opportunities are equally significant. The growing demand for advanced optical components in various industries, coupled with ongoing advancements in materials science and manufacturing technologies, is driving substantial investment in this field. This investment is fostering innovation and leading to the development of optical glasses with unprecedented properties and functionalities, paving the way for transformative advancements across multiple sectors.
Environmental Impact and Sustainability
The manufacturing of optical glass, while crucial for numerous technological advancements, carries a significant environmental footprint. This stems primarily from the energy-intensive production processes and the generation of waste materials. Understanding and mitigating these impacts are increasingly important as the demand for high-quality optical components continues to grow.The production of optical glass is energy-intensive, requiring high temperatures for melting raw materials and subsequent shaping processes.
Significant amounts of energy are consumed in these furnaces, often fueled by fossil fuels, contributing to greenhouse gas emissions. Furthermore, the manufacturing process generates various types of waste, including cullet (broken or rejected glass), refractory materials from furnace linings, and chemical residues from cleaning and polishing processes. Improper disposal of these materials can lead to soil and water contamination.
The extraction of raw materials, such as silica sand, also has environmental consequences, including habitat disruption and potential water pollution.
Energy Consumption in Optical Glass Manufacturing
High-temperature melting furnaces are the primary energy consumers in optical glass production. The energy intensity varies depending on the specific manufacturing process and the type of furnace used. For example, electric melting furnaces are generally more energy-efficient than those fueled by natural gas or oil, but they require a significant upfront investment. Continuous improvements in furnace design and control systems aim to optimize energy efficiency and minimize fuel consumption.
Studies have shown that significant energy savings can be achieved through the implementation of advanced process control technologies and the use of alternative energy sources. For instance, a shift towards renewable energy sources like solar or wind power to supply the electricity needed for electric melting furnaces would substantially reduce the carbon footprint.
Waste Management and Recycling in Optical Glass Production
Effective waste management strategies are crucial for minimizing the environmental impact of optical glass manufacturing. This includes the careful handling and disposal of cullet, which can often be recycled back into the production process, reducing the need for virgin raw materials. Refractory waste requires specialized disposal methods to prevent environmental contamination. Companies are increasingly adopting closed-loop systems to recycle process water and minimize water consumption.
The implementation of advanced filtration and purification technologies helps reduce the volume of wastewater requiring treatment. For example, some manufacturers have successfully implemented systems to recover and reuse chemicals used in the polishing process, significantly reducing waste generation.
Sustainable Practices in the Optical Glass Industry
Several sustainable practices are being implemented to minimize the environmental impact of optical glass manufacturing. These include the use of recycled cullet as a raw material, reducing reliance on virgin materials and lowering energy consumption. Improved furnace designs and process optimization are leading to greater energy efficiency and reduced emissions. The adoption of cleaner production technologies, such as the use of less polluting chemicals and the implementation of closed-loop water systems, is also gaining traction.
Companies are increasingly investing in life cycle assessments (LCAs) to evaluate the environmental impact of their products and processes, identifying areas for improvement and setting targets for emission reductions. Furthermore, the development and implementation of stricter environmental regulations and industry standards are driving the adoption of more sustainable practices. Examples include the development of new, less energy-intensive glass compositions and the exploration of alternative manufacturing methods that reduce waste and emissions.
Epilogue
The journey into the world of optical glass reveals a remarkable interplay between material science, engineering precision, and technological innovation. From the fundamental understanding of refractive index and Abbe number to the sophisticated manufacturing processes and rigorous quality control measures, every aspect contributes to the exceptional performance of this indispensable material. As we look toward the future, the ongoing development of new optical glasses promises to further expand the horizons of science and technology, paving the way for groundbreaking advancements in fields like photonics and optoelectronics.
The pursuit of sustainability within the industry also ensures that this vital resource remains available for generations to come.
Essential Questionnaire
What is the difference between soda-lime glass and optical glass?
Soda-lime glass is a common, inexpensive glass used in everyday applications. Optical glass, however, undergoes much stricter quality control and is designed for precision optical applications, requiring higher purity and homogeneity to minimize optical imperfections.
How is the refractive index of optical glass measured?
The refractive index is typically measured using a refractometer, an instrument that measures the angle of refraction of light passing through the glass. Precise measurements are crucial for ensuring the glass meets the specifications for its intended application.
Can optical glass be recycled?
While recycling optical glass is challenging due to the specific properties required, some initiatives are exploring methods to recover and reuse certain types of optical glass, particularly those from specific applications.
What are some emerging applications of optical glass?
Emerging applications include advanced laser systems, high-precision optical sensors, and components for quantum computing. The development of new glass compositions with tailored properties is driving these advancements.