Low-E Glass (Low Emissivity Glass) isn’t just another type of windowpane; it’s a technological marvel quietly revolutionizing energy efficiency in buildings worldwide. These specialized glass units boast coatings designed to control the flow of heat and light, impacting everything from your energy bills to your indoor comfort levels. This exploration delves into the science behind Low-E glass, its environmental benefits, and its growing role in sustainable architecture.
From understanding the different types of Low-E coatings available – hard-coat, soft-coat, and sputtered – to exploring their impact on heating and cooling costs, we’ll cover the practical applications and long-term advantages of incorporating Low-E glass into residential and commercial projects. We’ll also discuss the latest advancements in the field and consider the future of this innovative technology.
What is Low-E Glass?
Low-E glass, or low-emissivity glass, is a type of glass designed to improve energy efficiency in buildings. Its core function is to control the flow of heat through windows, reducing heat loss in winter and heat gain in summer. This is achieved through the application of microscopic, transparent metallic or metallic oxide coatings. These coatings don’t affect the visual appearance significantly but dramatically impact the glass’s thermal properties.
Low-E Coating Types
Several types of Low-E coatings exist, each with its own manufacturing process and performance characteristics. The choice of coating depends on factors like the climate, building design, and desired level of energy efficiency.
Low-E Glass Manufacturing
The manufacturing process of Low-E glass involves applying a thin, transparent coating to one or both surfaces of the glass. This is typically done using one of three main methods: hard-coating, soft-coating, and sputtering. Hard-coating involves applying the coating during the float glass manufacturing process, resulting in a durable coating resistant to scratches and abrasion. Soft-coating, applied after the glass is manufactured, offers superior performance in terms of U-factor and SHGC but is less durable.
Sputtering is a more advanced technique that allows for precise control over the coating’s properties and can produce highly efficient coatings. The coated glass is then often incorporated into insulated glazing units (IGUs), which consist of two or more panes of glass separated by a spacer filled with air or inert gas, further enhancing thermal performance.
Comparison of Low-E Glass Types
The following table compares the properties of different Low-E glass types. Note that specific values can vary depending on the manufacturer and the exact coating composition. The values presented here are representative examples and should not be considered definitive for all products.
Coating Type | U-factor (BTU/hr·ft²·°F) | SHGC | VLT (%) | Durability |
---|---|---|---|---|
Hard-coat | 0.30 – 0.40 | 0.30 – 0.45 | 70 – 80 | High |
Soft-coat | 0.20 – 0.30 | 0.20 – 0.35 | 70 – 85 | Moderate |
Sputtered | 0.15 – 0.25 | 0.15 – 0.30 | 75 – 85 | High to Moderate (depending on specific coating) |
Energy Efficiency Benefits of Low-E Glass
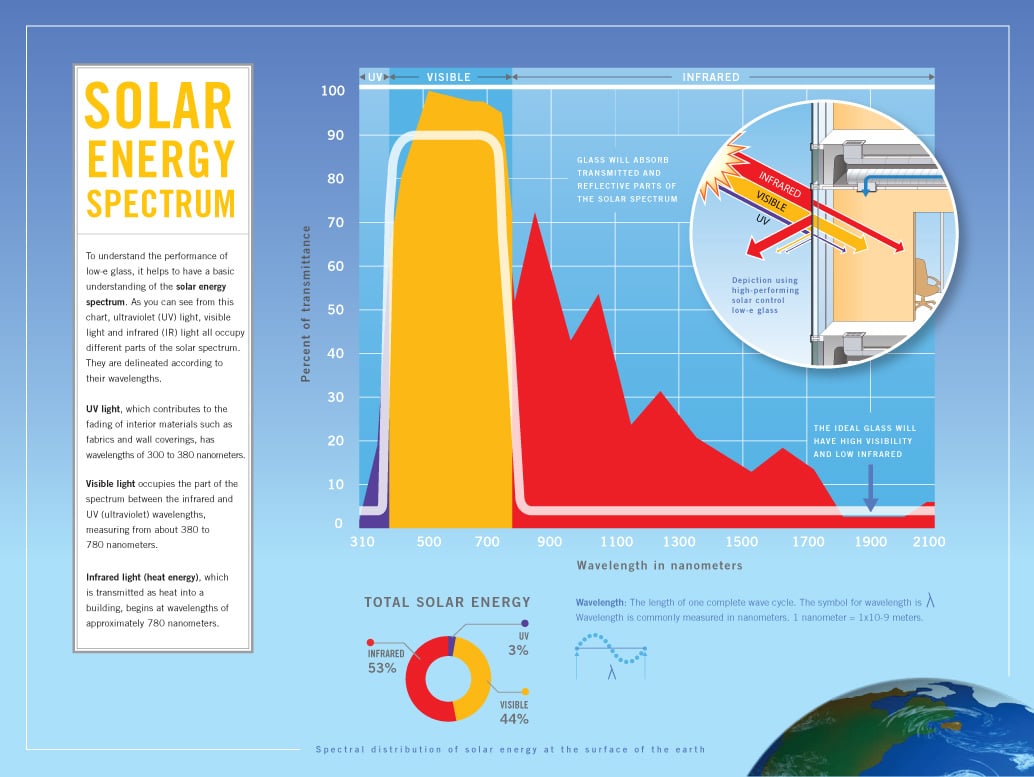
Source: hubspot.net
Low-E glass, with its special coatings, significantly improves a building’s energy performance by reducing heat transfer through windows. This translates to lower energy bills and a more comfortable indoor environment, making it a smart investment for both homeowners and commercial developers. The technology behind Low-E glass allows for precise control over the flow of heat, resulting in substantial energy savings throughout the year.Low-E glass reduces energy consumption in buildings primarily by controlling the transmission of both solar heat gain and radiant heat loss.
In summer, it reflects much of the sun’s infrared radiation, preventing excessive heat from entering the building and reducing the strain on air conditioning systems. Conversely, in winter, it minimizes the escape of heat from inside, reducing the demand on heating systems. This dual-action capability makes Low-E glass effective in a wide range of climates.
Impact on Heating and Cooling Costs, Low-E Glass (Low Emissivity Glass)
The impact of Low-E glass on heating and cooling costs is substantial. By reducing the amount of energy needed to maintain a comfortable indoor temperature, Low-E glass directly lowers utility bills. The exact savings depend on factors like climate, building design, and the specific type of Low-E glass used. However, studies have consistently shown that Low-E glass can lead to significant reductions—often in the range of 10-30%—in annual energy costs associated with heating and cooling.
For example, a large office building in a hot climate might see a considerable reduction in its air conditioning expenses, while a residential home in a colder region could experience significant savings on its heating bills. These savings accumulate over the lifetime of the building, making the initial investment in Low-E glass worthwhile.
Improved Indoor Comfort
Beyond energy savings, Low-E glass contributes to a more comfortable indoor environment. By reducing solar heat gain in summer, it helps prevent uncomfortable overheating and reduces the need for constant air conditioning. In winter, it minimizes heat loss, preventing drafts and maintaining a more consistent and comfortable temperature throughout the building. This improved thermal comfort translates to a more pleasant living or working space, increasing occupant satisfaction and productivity.
The reduction in temperature fluctuations also minimizes the stress on building materials and reduces the potential for condensation, preventing damage and promoting a healthier indoor environment.
Examples of Building Designs Maximizing Energy Savings
The energy-saving potential of Low-E glass is maximized when integrated effectively into building design. Careful consideration of factors like window orientation, shading devices, and overall building insulation is crucial.
- Passive Solar Design: Buildings designed to maximize solar heat gain in winter and minimize it in summer can significantly benefit from Low-E glass. South-facing windows (in the Northern Hemisphere) with Low-E coatings can effectively capture solar heat during winter, reducing the need for supplemental heating. Strategic use of overhangs or awnings can shade windows during summer, further reducing solar heat gain.
- Modern Office Buildings: Many modern office buildings incorporate large expanses of glass for natural light. The use of Low-E glass in these designs minimizes energy consumption associated with both heating and cooling, while still allowing for ample natural light.
- Green Building Certifications: Buildings seeking LEED (Leadership in Energy and Environmental Design) or other green building certifications often utilize Low-E glass as a key element in achieving energy efficiency targets. The performance of Low-E glass is often a significant factor in earning points towards certification.
Environmental Impact and Sustainability
Low-E glass offers significant environmental advantages compared to traditional glass, contributing to a more sustainable built environment. Its energy-saving properties directly reduce reliance on fossil fuels for heating and cooling, leading to lower greenhouse gas emissions. The long-term benefits extend beyond immediate energy savings, impacting the overall lifecycle environmental footprint of buildings.Low-E glass reduces a building’s environmental impact primarily through its superior energy efficiency.
By minimizing heat transfer, it lessens the demand on HVAC systems, thus decreasing the energy consumption associated with their operation. This translates to a lower carbon footprint compared to buildings using traditional glass, which requires significantly more energy to maintain comfortable indoor temperatures. The reduced energy demand also lowers air pollution resulting from power generation.
Carbon Footprint Comparison
The carbon footprint of Low-E glass is lower than that of traditional glass throughout its lifecycle. While the manufacturing process of Low-E glass involves additional steps to apply the low-emissivity coating, the energy savings realized during the building’s operational life significantly outweigh the increased manufacturing footprint. Studies have shown that the reduced energy consumption over the building’s lifespan more than compensates for the extra energy used in Low-E glass production.
For example, a study by the Lawrence Berkeley National Laboratory showed that the embodied carbon of Low-E glass is comparable or even lower than traditional glass when considering the operational energy savings over a building’s lifetime. The exact difference varies depending on factors like climate, building design, and the specific type of Low-E coating used.
Long-Term Sustainability Advantages
The long-term sustainability advantages of Low-E glass are substantial. Its extended lifespan contributes to reduced waste generation compared to more frequently replaced materials. The reduced energy consumption translates to lower operational costs for building owners, encouraging longer building lifespans and minimizing the need for frequent demolition and reconstruction. This reduced demolition and reconstruction also reduces the environmental impact associated with the extraction of raw materials and waste disposal.
Furthermore, the durability of Low-E glass contributes to a reduced need for replacements, thus minimizing material consumption and waste over time.
Life-Cycle Assessment of Low-E Glass
The following table summarizes the life-cycle assessment of Low-E glass, considering its environmental impact at each stage.
Stage | Environmental Impact | Mitigation Strategies | Comments |
---|---|---|---|
Manufacturing | Energy consumption for glass production and coating application; emissions of greenhouse gases and air pollutants. | Using renewable energy sources in manufacturing; optimizing production processes to minimize waste and energy use; utilizing recycled materials. | The manufacturing process of Low-E glass has a higher initial energy requirement, but the operational energy savings usually outweigh this. |
Transportation | Fuel consumption and greenhouse gas emissions from transportation to the building site. | Optimizing transportation routes and using efficient transportation modes; reducing packaging materials. | Transportation impact is relatively small compared to other stages. |
Installation | Energy consumption associated with installation; potential waste generation from broken or damaged glass. | Careful handling and installation practices to minimize waste; using recycled materials for packaging and disposal of waste. | Proper installation practices are crucial to minimize waste and ensure the longevity of the glass. |
Disposal/End-of-Life | Landfill space consumption; potential release of harmful substances if not properly disposed of. | Recycling programs for glass; developing end-of-life management strategies for the Low-E coating. | Recycling programs are crucial to minimize the environmental impact of disposal. Research into responsible disposal methods for the coating is ongoing. |
Applications of Low-E Glass: Low-E Glass (Low Emissivity Glass)
Low-E glass, with its superior energy efficiency properties, finds widespread application in both residential and commercial buildings, significantly impacting building design and performance across diverse climates and architectural styles. Its versatility allows for customized solutions tailored to specific needs, maximizing comfort and minimizing environmental impact.Low-E glass’s applications are diverse and extend beyond simply improving energy efficiency. Its use impacts aesthetics, durability, and the overall sustainability of a building.
Understanding these applications is crucial for architects, builders, and homeowners alike.
Residential Applications of Low-E Glass
Low-E glass is a popular choice for residential windows, doors, and skylights. Its ability to reduce heat transfer makes it ideal for improving comfort and reducing energy costs in homes. It’s particularly beneficial in regions with extreme temperature fluctuations, where it can help maintain a consistent indoor temperature year-round. Furthermore, its use in windows can enhance the aesthetic appeal of a home, contributing to its overall value.
Commercial Applications of Low-E Glass
In commercial buildings, the benefits of Low-E glass are amplified due to the larger surface area of windows and the need for efficient climate control in larger spaces. Office buildings, retail spaces, and hotels frequently utilize Low-E glass to minimize energy consumption and improve occupant comfort. The reduced solar heat gain can lead to significant cost savings on air conditioning, while the improved insulation helps reduce heating costs in colder months.
The enhanced clarity and reduced glare can also improve productivity and occupant well-being.
Low-E Glass in Different Architectural Styles
The adaptability of Low-E glass allows its seamless integration into a wide array of architectural styles. From modern minimalist designs to traditional Victorian architecture, Low-E glass enhances the aesthetic appeal without compromising functionality. Its neutral appearance allows for versatility, blending seamlessly with various design elements. In modern buildings, large expanses of Low-E glass can create stunning visual effects while maintaining energy efficiency.
In traditional buildings, Low-E glass can be incorporated without disrupting the overall architectural integrity.
Suitability of Low-E Glass for Various Climates
Low-E glass offers distinct advantages across diverse climates. In hot climates, its ability to reflect solar heat reduces the burden on air conditioning systems, leading to significant energy savings. In cold climates, it minimizes heat loss, reducing reliance on heating systems. Its versatility makes it suitable for both temperate and extreme climates, adapting to specific needs and maximizing energy efficiency regardless of location.
For example, a coating optimized for a hot, sunny climate might differ from one designed for a cold, cloudy climate.
Innovative Applications of Low-E Glass in Modern Architecture
- Curtain Walls: Large-scale curtain walls incorporating Low-E glass are increasingly common in modern skyscrapers, offering both aesthetic appeal and significant energy savings. The image of a modern glass skyscraper showcasing a reflective curtain wall, shimmering in the sunlight, demonstrates the elegant integration of Low-E glass in large-scale projects. The reflective properties reduce solar heat gain while maximizing natural light penetration.
- Self-Cleaning Glass: Combining Low-E coatings with self-cleaning technologies creates a maintenance-free solution for high-rise buildings and other structures where cleaning can be difficult and expensive. The image depicts a clean, pristine glass facade, effortlessly maintaining its appearance without the need for frequent cleaning, illustrating the benefits of this innovative technology.
- Smart Windows: Integration of Low-E glass with electrochromic technology allows for dynamic control of light and heat transmission, adjusting automatically based on external conditions. This image shows a window smoothly transitioning from transparent to tinted, adapting to changing light levels, showcasing the intelligent and responsive nature of this application.
Cost Considerations and Return on Investment
Investing in Low-E glass involves upfront costs that exceed those of standard glass, but the long-term energy savings and increased comfort often make it a worthwhile investment. This section will explore the initial cost differences, the potential for long-term savings, and the overall return on investment (ROI) associated with choosing Low-E glass.
Initial Cost Comparison
Low-E glass typically costs more than standard clear glass. The price difference varies depending on factors such as the type of Low-E coating, the glass thickness, and the size of the windows. While a precise figure is impossible without specific details, expect to pay a premium of 20-50% or more for Low-E glass compared to standard glass. This higher initial cost is a significant factor to consider when budgeting for a new construction or renovation project.
However, this premium should be viewed in the context of the long-term benefits.
Long-Term Cost Savings
The primary benefit of Low-E glass lies in its energy efficiency. By reducing heat transfer, Low-E glass lowers heating and cooling costs. This translates to significant savings over the lifetime of the windows, potentially offsetting the higher initial investment many times over. The amount of savings depends on factors such as climate, building design, and the efficiency of the heating and cooling systems.
In colder climates, the reduction in heat loss during winter can be substantial, while in warmer climates, the reduction in heat gain during summer becomes crucial. These savings manifest in lower energy bills, contributing to long-term cost reductions.
Return on Investment (ROI) Analysis
Calculating the ROI of Low-E glass requires comparing the initial cost increase against the projected energy savings over the expected lifespan of the windows (typically 20-30 years). Several factors influence the ROI, including:
- Climate: Colder or hotter climates will generally yield a faster ROI.
- Energy prices: Higher energy prices accelerate the payback period.
- Window size and number: Larger window areas will result in greater energy savings.
- Type of Low-E coating: Different coatings offer varying levels of performance and cost.
A simple ROI calculation involves dividing the net savings (total energy savings minus the additional cost of Low-E glass) by the initial investment. A higher ROI indicates a faster payback period. Many online calculators and energy efficiency tools can help estimate the ROI for specific situations. For example, a homeowner in a cold climate with high energy costs might see a payback period of 5-7 years, while someone in a moderate climate might see a longer payback period of 10-15 years.
Sample Cost-Benefit Analysis (Residential Application)
The following table provides a simplified cost-benefit analysis for a hypothetical residential application. Note that these figures are estimates and can vary greatly depending on location, energy costs, and specific window specifications.
Item | Cost | Savings (Annual) | Savings (20 years) |
---|---|---|---|
Standard Glass (10 windows) | $2,000 | $0 | $0 |
Low-E Glass (10 windows) | $3,000 | $300 | $6,000 |
Net Cost Increase | $1,000 | ||
Net Savings (20 years) | $5,000 |
Note: This example assumes a $300 annual energy savings with Low-E glass. Actual savings will vary.
Maintenance and Durability
Low-E glass, while offering significant energy efficiency benefits, requires proper maintenance to ensure its longevity and continued performance. The durability and lifespan of Low-E windows depend on several factors, including the type of coating used, the quality of installation, and environmental conditions. Understanding these factors and employing appropriate maintenance practices will help maximize the investment in Low-E glass.Low-E coatings are remarkably durable, designed to withstand years of exposure to the elements.
However, the specific durability varies depending on the type of coating. Hard coatings, for instance, tend to be more resistant to scratching and abrasion than softer coatings. The manufacturing process also plays a significant role; high-quality manufacturing ensures a more robust and longer-lasting coating. Even with durable coatings, however, improper cleaning or accidental damage can compromise the integrity of the Low-E layer, impacting its performance over time.
Durability and Longevity of Low-E Coatings
Different types of Low-E coatings exhibit varying levels of durability. Pyrolytic coatings, applied during the glass manufacturing process, are generally considered the most durable, offering excellent resistance to scratching and abrasion. Sputtered coatings, applied after the glass is manufactured, are also quite durable but may be slightly less resistant to damage than pyrolytic coatings. The longevity of a Low-E coating can range from decades for high-quality installations to a shorter period if exposed to harsh environmental conditions or subjected to improper cleaning.
While there’s no single definitive lifespan, a well-maintained Low-E window can reasonably be expected to retain its performance for many years, often exceeding 20 years.
Potential Issues and Challenges with Long-Term Use
While Low-E glass is designed for long-term use, certain issues can arise over time. One potential problem is the degradation of the coating due to exposure to UV radiation and extreme weather conditions. This degradation may be gradual and may not significantly impact performance for many years. Another concern is accidental damage, such as scratches or impacts, which can compromise the coating’s integrity.
Additionally, improper cleaning methods can also damage the coating, leading to reduced energy efficiency. Finally, while rare, some Low-E coatings may experience delamination, where the coating separates from the glass. This is more likely to occur with lower-quality coatings or improper installation.
Best Practices for Cleaning and Maintaining Low-E Glass
Regular cleaning is crucial for maintaining the performance and appearance of Low-E glass. To prevent damage and ensure the longevity of the coating, follow these best practices:
- Use a soft, non-abrasive cloth or sponge.
- Employ a mild detergent solution; avoid harsh chemicals, abrasive cleaners, or ammonia-based products.
- Rinse thoroughly with clean water to remove all traces of detergent.
- Dry the glass gently with a clean, soft cloth to prevent water spots.
- Avoid using high-pressure water jets or abrasive cleaning tools.
- Address any scratches or damage promptly to prevent further deterioration.
- Regularly inspect the windows for any signs of damage or degradation.
Technological Advancements in Low-E Glass
Low-E glass technology is constantly evolving, driven by the need for improved energy efficiency and sustainability in buildings. Recent advancements focus on enhancing performance, expanding applications, and simplifying manufacturing processes. These improvements are leading to more effective and cost-competitive solutions for reducing energy consumption and environmental impact.Recent advancements in Low-E glass technology have significantly improved its performance characteristics.
Manufacturers are exploring new coating materials and deposition techniques to optimize solar heat gain control and infrared radiation reflection. This leads to enhanced insulation properties, resulting in lower heating and cooling costs for building owners. Simultaneously, the industry is working on improving the visible light transmission of Low-E glass, ensuring that buildings remain bright and comfortable without compromising energy efficiency.
Improved Coating Materials and Deposition Techniques
The development of more durable and effective coatings is a major area of progress. New materials are being explored to increase the longevity of the Low-E coating and its resistance to scratching and degradation. Advanced deposition techniques, such as magnetron sputtering and chemical vapor deposition, allow for greater control over the coating’s thickness, composition, and uniformity, leading to improved performance and consistency.
For example, the use of silver nanoparticles within the coating structure has demonstrated enhanced infrared reflectivity compared to traditional tin oxide-based coatings. This improvement translates directly to better thermal insulation and energy savings.
Emerging Trends in Low-E Glass Manufacturing and Applications
Several emerging trends are shaping the future of Low-E glass. One notable trend is the increasing adoption of triple-pane windows incorporating Low-E coatings. This configuration offers significantly enhanced insulation compared to double-pane windows, further reducing energy consumption and improving indoor comfort. Another trend involves the integration of Low-E coatings with other advanced glazing technologies, such as self-cleaning glass or electrochromic glass, to create multifunctional windows that can dynamically adjust their properties based on environmental conditions.
This integration creates smart windows capable of optimizing both energy efficiency and daylighting. The development of flexible Low-E coatings for use in curved or unusual architectural designs is also gaining momentum, broadening the range of applications for this technology.
Future Potential of Low-E Glass in Sustainable Building Design
Low-E glass is poised to play a crucial role in the future of sustainable building design. Its ability to significantly reduce energy consumption makes it a key component of green building initiatives. As building codes and energy efficiency standards become more stringent, the demand for Low-E glass is expected to increase dramatically. Furthermore, advancements in coating technology and manufacturing processes are driving down the cost of Low-E glass, making it a more accessible and economically viable option for a wider range of building projects.
The integration of Low-E glass with other sustainable building materials and technologies, such as solar panels and smart building management systems, will further enhance its contribution to environmentally responsible construction.
A New Type of Low-E Glass Coating: Multilayer Oxide Coating with Embedded Graphene
Imagine a Low-E coating composed of multiple layers of metal oxides, such as titanium dioxide (TiO2) and zinc oxide (ZnO), interspersed with layers of graphene. The graphene layers act as highly efficient infrared reflectors, while the metal oxide layers provide durability, scratch resistance, and control over visible light transmission. This multilayer structure allows for fine-tuning of the coating’s optical and thermal properties, optimizing performance for specific climatic conditions and building orientations.
The graphene’s unique properties result in exceptionally high infrared reflectivity, exceeding that of traditional silver-based coatings, leading to superior thermal insulation and significant energy savings. This design also exhibits enhanced durability and resistance to degradation compared to conventional coatings, promising a longer lifespan and reduced replacement costs. The increased infrared reflectivity translates to a lower U-value (heat transfer coefficient), indicating superior thermal performance and improved energy efficiency.
For instance, a building incorporating this advanced coating could potentially reduce its heating and cooling energy consumption by 20-30% compared to buildings using standard Low-E glass.
Summary
Ultimately, Low-E glass represents a significant step forward in sustainable building practices. Its ability to reduce energy consumption, lower carbon footprints, and enhance indoor comfort makes it a compelling choice for both new constructions and renovations. While the initial investment may be slightly higher than standard glass, the long-term cost savings and environmental benefits clearly demonstrate a strong return on investment.
As technology continues to advance, we can expect even greater efficiency and performance from Low-E glass, solidifying its position as a key player in the future of sustainable building design.
Detailed FAQs
Is Low-E glass more expensive than regular glass?
Yes, typically Low-E glass has a higher upfront cost. However, the long-term energy savings often offset this initial expense.
Can Low-E glass be cleaned like regular glass?
Yes, but it’s recommended to use a soft cloth and non-abrasive cleaner to avoid damaging the coatings. Avoid harsh chemicals.
Does Low-E glass affect the appearance of a building?
The impact on appearance is minimal. Different Low-E coatings offer varying levels of light transmission and reflectivity, allowing for aesthetic customization.
How long does Low-E glass last?
The lifespan of Low-E glass depends on the coating type and quality. High-quality coatings can last for decades with proper maintenance.
Is Low-E glass suitable for all climates?
Yes, but the optimal type of Low-E coating will vary depending on the climate. Colder climates benefit from coatings that maximize solar heat gain, while warmer climates benefit from coatings that minimize it.