Laminated Glass, far more than just a type of glass, represents a significant advancement in safety and performance. It’s created by bonding multiple layers of glass together with a strong, transparent interlayer, resulting in a material with exceptional strength, sound insulation, and security features. This fascinating material finds applications across diverse industries, from high-rise buildings to automotive windshields, and its unique properties continue to drive innovation in construction and design.
This exploration delves into the manufacturing process, the various types of interlayers and their distinct characteristics, and the wide-ranging applications of laminated glass. We’ll examine its impact resistance, sound-dampening capabilities, and security benefits, comparing its performance to traditional annealed glass. Further, we’ll discuss relevant safety standards, cost considerations, and the growing focus on sustainable practices within the laminated glass industry.
Definition and Types of Laminated Glass
Laminated glass is a type of safety glass consisting of two or more layers of glass bonded together by one or more interlayers of polyvinyl butyral (PVB) or other similar materials. This bonding creates a strong, durable product that offers enhanced safety and performance characteristics compared to standard annealed glass. The interlayer is key to its functionality, holding the glass layers together even when shattered, preventing dangerous shards from scattering.
Laminated Glass Manufacturing Process
The manufacturing process begins with the preparation of the glass sheets. These sheets are cleaned meticulously to ensure optimal bonding with the interlayer. The interlayer material, typically PVB film, is then placed between the glass sheets. The assembly is then fed into an autoclave, a large pressure vessel, where it is subjected to heat and pressure. This process causes the interlayer to melt slightly and bond firmly to the glass sheets, creating a single, unified panel.
The final product is then cooled and inspected for quality before being cut to size and further processed if necessary.
Types of Interlayers and Their Properties
Several interlayers can be used in laminated glass, each offering unique properties. The most common is polyvinyl butyral (PVB), known for its excellent adhesion to glass, impact resistance, and ability to hold the glass fragments together upon breakage. Other interlayers include SentryGlas®, a strong and stiff ionoplast interlayer offering high strength and improved resistance to delamination; ethylene-vinyl acetate (EVA), providing flexibility and good adhesion; and polyurethane interlayers, suitable for specific applications requiring high sound insulation.
The choice of interlayer depends heavily on the intended application and required performance characteristics.
Applications of Laminated Glass Based on Interlayer Type
The selection of interlayer significantly impacts the final application of the laminated glass. PVB laminated glass is widely used in automotive windshields, architectural glazing, and security applications due to its balance of strength and transparency. SentryGlas® laminated glass, due to its superior strength, is often preferred in hurricane-prone regions or for applications requiring exceptional impact resistance, such as skylights or high-rise buildings.
EVA laminated glass is often used in applications where flexibility is needed, such as curved glass or applications requiring intricate shapes. Finally, polyurethane interlayers find their niche in noise reduction applications like soundproof windows.
Comparison of Laminated Glass Types
Different types of laminated glass exhibit varying performance characteristics. While all provide improved safety over monolithic glass, their strength, light transmission, and UV protection differ. PVB offers a good balance of properties, while SentryGlas® boasts superior strength but may be slightly less transparent. The choice depends on the specific requirements of the application.
Laminated Glass Type | Strength | Light Transmission | UV Protection |
---|---|---|---|
PVB Laminated Glass | High | Excellent | Good |
SentryGlas® Laminated Glass | Very High | Good | Good |
EVA Laminated Glass | Moderate | Excellent | Moderate |
Polyurethane Laminated Glass | Moderate to High | Good to Excellent | Good |
Properties and Performance of Laminated Glass
Laminated glass, thanks to its unique construction, boasts a range of superior properties compared to its annealed counterpart. These enhanced characteristics make it a versatile material suitable for diverse architectural and safety applications. The key improvements lie in its impact resistance, sound insulation capabilities, and enhanced security features.
Impact Resistance of Laminated Glass
Laminated glass significantly surpasses annealed glass in impact resistance. The interlayer, typically polyvinyl butyral (PVB), holds the glass fragments together even after a forceful impact. While annealed glass shatters into sharp, dangerous shards upon impact, laminated glass remains largely intact, minimizing the risk of injury and property damage. This is crucial in applications like vehicle windshields, where it prevents the scattering of glass fragments in accidents.
The level of impact resistance is directly proportional to the thickness of the glass and the interlayer. A thicker glass and interlayer will withstand greater impact forces before failure. For example, a laminated windshield in a car can withstand the impact of a small stone thrown from a passing vehicle, whereas an annealed glass window would likely shatter.
Sound Insulation Properties of Laminated Glass
The interlayer in laminated glass acts as a sound damper, effectively reducing noise transmission. The PVB layer absorbs sound waves, preventing their passage through the glass. This property is particularly beneficial in buildings located in noisy environments, such as near busy roads or airports. The thicker the interlayer, the better the sound insulation. For instance, laminated glass is frequently used in noise barriers along highways to mitigate the sound pollution impacting nearby residential areas.
The reduction in noise levels is measurable in decibels (dB), with thicker laminates providing greater sound attenuation. A building using laminated glass in its windows could experience a noticeable decrease in ambient noise, leading to a more peaceful interior environment.
Security Features of Laminated Glass
Laminated glass provides a significant security advantage over annealed glass. The interlayer makes it significantly more difficult to break through, deterring intrusion and increasing the time required to gain entry. While annealed glass shatters easily, laminated glass resists penetration, delaying attempts at forced entry. This added security is valuable in applications such as storefront windows, museum displays, and security-sensitive areas.
The increased resistance to break-in attempts can provide crucial time for response by security personnel or law enforcement. Furthermore, even if the glass is broken, the fragments remain adhered to the interlayer, preventing easy access through the opening.
Factors Influencing the Strength and Durability of Laminated Glass
Several factors contribute to the overall strength and durability of laminated glass. These include the thickness and type of glass used, the thickness and type of interlayer, and the manufacturing process. The use of high-quality materials and precise manufacturing techniques ensures optimal performance. For example, using a thicker PVB interlayer will result in increased impact resistance and sound insulation.
Similarly, employing stronger glass types like tempered glass in the laminate construction further enhances its durability. Exposure to extreme temperatures or UV radiation over extended periods can affect the long-term performance of the interlayer, so proper selection and installation are crucial.
Performance of Laminated Glass Under Stress
Laminated glass exhibits different behaviors under various stress conditions. Under impact, the PVB interlayer prevents complete shattering, holding the glass fragments together. Under pressure, it can withstand significant loads before failure, depending on its thickness and the glass type used. Under temperature fluctuations, the interlayer helps to maintain the structural integrity of the glass, mitigating the effects of thermal expansion and contraction.
For instance, in a hurricane, laminated glass may crack but will remain largely intact, preventing debris from entering the building. Conversely, in a fire, the interlayer can help to delay the spread of flames and provide additional time for evacuation.
Applications of Laminated Glass
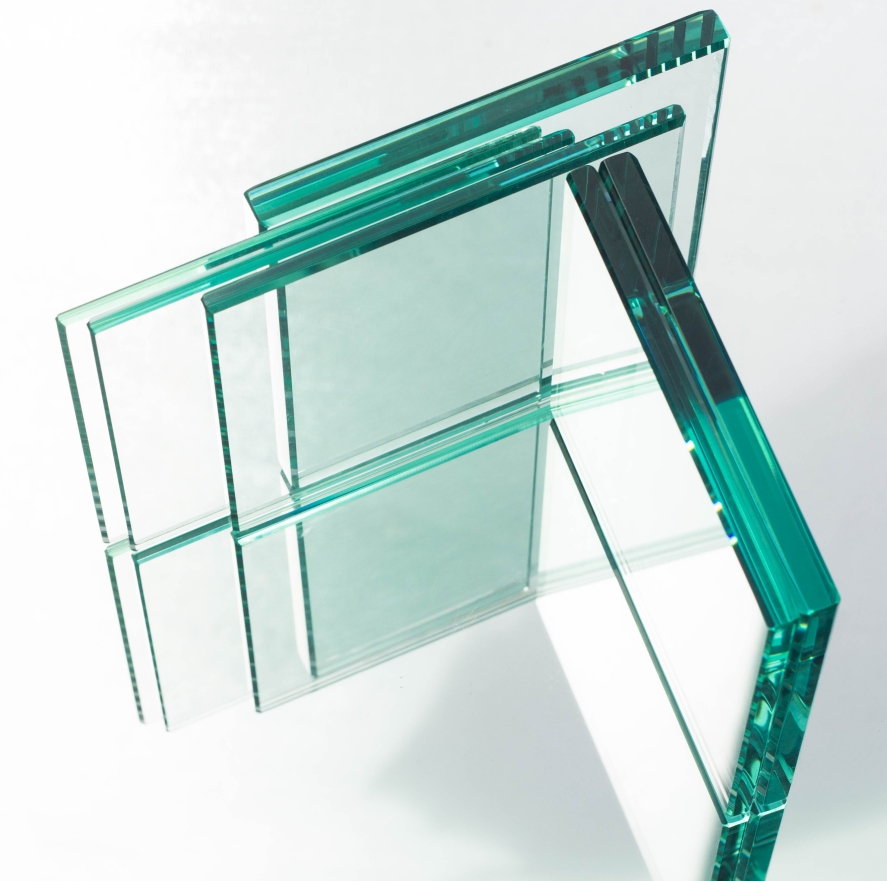
Source: customglassmfg.net
Laminated glass, with its inherent strength and safety features, finds applications across a wide range of industries and architectural designs. Its versatility stems from its ability to combine strength with aesthetic appeal and enhanced safety properties. This section will explore several key applications, highlighting the benefits this material provides.
Laminated Glass in High-Rise Buildings
Imagine a sleek, modern high-rise building, its facade shimmering in the sunlight. This building likely incorporates laminated glass in its curtain wall system. The large panes of laminated glass offer significant advantages: they provide excellent sound insulation, reducing noise pollution from the city below. Their impact resistance protects the building’s occupants from debris and accidental damage, while also contributing to the structural integrity of the building.
Furthermore, laminated glass can be treated to reduce solar heat gain, improving energy efficiency and occupant comfort. In the event of breakage, the interlayer holds the glass fragments together, preventing them from shattering and causing injury or damage. This is crucial in a high-rise building where the consequences of glass failure can be severe.
Laminated Glass in Automotive Windshields
Automotive windshields are a prime example of laminated glass’s crucial role in safety. The interlayer, typically polyvinyl butyral (PVB), bonds two sheets of glass, creating a strong, yet flexible, unit. In the event of an impact, the PVB layer prevents the glass from shattering into dangerous shards, significantly reducing the risk of injury to the driver and passengers.
Beyond safety, the PVB layer also helps to dampen noise and reduce vibrations, improving the driving experience. Furthermore, the laminated structure provides better resistance to scratches and weathering compared to single-pane glass.
Industries Utilizing Laminated Glass
The versatility of laminated glass makes it a valuable material across numerous sectors. Here are five industries that extensively use laminated glass, along with explanations of its benefits:
- Construction: Used in windows, doors, curtain walls, skylights, and balustrades in both residential and commercial buildings for its strength, safety, and sound insulation properties.
- Automotive: Essential for windshields and other windows in vehicles due to its safety features and ability to withstand impacts.
- Marine: Employed in windows and portholes on boats and ships, offering impact resistance and protection against harsh marine environments.
- Museums and Art Conservation: Provides protection for valuable artwork and artifacts, preventing damage from impacts and UV radiation. The strength and clarity of the glass are also important factors.
- Security: Used in security windows and doors, offering resistance to forced entry and protecting against vandalism and burglaries. Its strength and ability to withstand impacts make it ideal for high-security applications.
Advantages of Laminated Glass in Museum Displays
In museums and art galleries, the preservation of priceless artifacts is paramount. Laminated glass offers several key advantages for protecting these valuable items. Its strength prevents damage from accidental impacts, while its UV-filtering properties protect delicate artwork from fading and degradation caused by sunlight. The clarity of the glass ensures that the artwork is displayed with minimal distortion, allowing visitors to appreciate its beauty without compromising its safety.
The inherent safety of laminated glass also minimizes the risk of injury to visitors in the event of breakage.
Building Facade Incorporating Laminated Glass
Envision a contemporary office building, its facade a breathtaking display of architectural ingenuity. The exterior walls are clad in large panels of laminated glass, arranged in a dynamic, geometric pattern. Some panels are tinted a subtle blue-green, while others are clear, allowing natural light to flood the interior. The laminated glass provides excellent thermal insulation, reducing energy consumption and improving the building’s environmental performance.
The strength and impact resistance of the glass ensure the building’s structural integrity and safety. At night, the building is transformed, with the internal lighting creating a mesmerizing glow that highlights the unique architectural design. The laminated glass panels, reflecting the city lights, add to the building’s overall aesthetic appeal, turning it into a stunning landmark.
Standards and Regulations for Laminated Glass
Laminated glass, due to its enhanced safety and security features, is subject to a variety of standards and regulations worldwide. These standards dictate manufacturing processes, performance requirements, and installation practices to ensure consistent quality and safety for consumers. Compliance with these regulations is crucial for manufacturers and installers alike.
Key Safety Standards and Regulations
Numerous organizations globally set standards for laminated glass. These include, but are not limited to, ASTM International (American Society for Testing and Materials) in the United States, EN standards (European Norms) within the European Union, and ISO (International Organization for Standardization) international standards. Specific standards address various aspects, such as impact resistance, sound insulation, and the type and performance of the interlayer used.
For instance, ASTM E1300 covers the standard test method for determining the impact resistance of laminated glass, while EN 14449 details the requirements for laminated safety glass. These standards often specify minimum requirements for properties like glass thickness, interlayer type, and overall strength. Variations exist between regional standards, reflecting differing construction practices and environmental conditions.
The Role of Testing and Certification
Testing and certification play a vital role in verifying that laminated glass meets the required standards. Independent testing laboratories, accredited by relevant organizations, conduct rigorous tests on samples of laminated glass to assess its performance characteristics. These tests typically involve evaluating impact resistance, penetration resistance, and other relevant properties. Successful completion of these tests leads to certification, indicating that the product meets the specified standards.
This certification provides assurance to architects, builders, and consumers that the laminated glass is safe and performs as expected. Without proper testing and certification, the quality and performance of the laminated glass cannot be guaranteed.
Comparison of Standards Across Regions, Laminated Glass
While the fundamental principles underlying laminated glass standards are similar globally, variations exist in specific requirements. For example, the minimum impact resistance requirements might differ between the United States and the European Union, reflecting variations in building codes and common applications. Similarly, the types of interlayers permitted and their performance characteristics may be subject to different regional standards. This highlights the importance of understanding the specific standards applicable to a given project location.
Consultations with local building authorities are crucial to ensure compliance.
Requirements for Proper Installation and Maintenance
Correct installation is paramount to ensure the performance and longevity of laminated glass. Standards often include guidelines on handling, cutting, and glazing techniques. Improper installation can compromise the structural integrity and safety features of the glass, negating the benefits of using laminated glass. Maintenance is relatively minimal; however, it’s important to avoid scratching or impacting the surface of the glass.
Regular cleaning with appropriate cleaning agents is recommended. Damage to the glass should be assessed and repaired or replaced promptly by qualified professionals to prevent further issues.
Factors to Consider When Specifying Laminated Glass
Choosing the right laminated glass for a project requires careful consideration of several factors:
- Required Safety Level: The level of impact resistance needed depends on the application (e.g., residential window vs. storefront). Higher security needs may necessitate thicker glass and stronger interlayers.
- Acoustic Performance: Laminated glass offers superior sound insulation compared to monolithic glass. The thickness of the glass and the type of interlayer affect the sound reduction.
- Solar Control: The selection of glass type and interlayer can impact the amount of solar heat and UV radiation transmitted into the building.
- Aesthetic Considerations: Laminated glass can incorporate various interlayers, allowing for different levels of transparency, tinting, or even decorative patterns.
- Budgetary Constraints: The cost of laminated glass varies depending on the thickness, type of glass, and interlayer used. Balancing performance requirements with budget is essential.
Cost and Sustainability of Laminated Glass
Laminated glass, while offering superior safety and performance, comes with a higher initial cost compared to standard annealed glass. However, a comprehensive assessment needs to consider its lifecycle costs and environmental impact to understand its true value proposition. This section will delve into the factors affecting the cost of laminated glass, compare it to alternatives, and explore its sustainability aspects.
Factors Influencing the Cost of Laminated Glass
Several factors contribute to the price of laminated glass. The thickness and type of glass used are primary determinants. Thicker glass, naturally, increases cost. The interlayer material also plays a significant role; polyvinyl butyral (PVB) is common, but other materials like SentryGlas® offer enhanced performance but at a premium price. The size and complexity of the glass unit also impact manufacturing costs.
Finally, market demand and the cost of raw materials, such as resin and glass, can fluctuate, directly influencing the final price. For example, a large-scale project requiring many custom-sized laminated glass units will cost more than a smaller project using standard sizes.
Lifecycle Cost Comparison with Alternative Glazing Options
While the initial cost of laminated glass is higher than that of annealed or tempered glass, its longer lifespan and enhanced performance features can lead to lower lifecycle costs. The added safety and security features reduce the risk of replacement due to breakage, resulting in long-term savings. Furthermore, its superior insulation properties can reduce energy consumption for heating and cooling, offering further cost advantages over the long term.
A building with laminated glass may see reduced insurance premiums due to its improved safety profile, further lowering the overall lifecycle cost. A detailed lifecycle cost analysis comparing different glazing options is crucial for informed decision-making in construction projects. Such analyses frequently show that despite higher upfront investment, laminated glass delivers significant cost benefits over its service life.
Environmental Impact of Laminated Glass Production and Disposal
The manufacturing process of laminated glass involves energy consumption for glass production and the processing of interlayer materials. The transportation of materials and finished products also contributes to the carbon footprint. Disposal presents another challenge. While the glass component can be recycled, the interlayer material often complicates this process, reducing the recycling rate compared to standard glass.
However, advancements are being made in developing more recyclable interlayer materials and improved recycling technologies to address these challenges. For instance, some manufacturers are exploring the use of bio-based interlayers or developing more efficient separation techniques for recycling laminated glass components.
Sustainable Practices in Laminated Glass Manufacturing and Recycling
Several initiatives aim to enhance the sustainability of laminated glass. The use of recycled glass cullet in the glass production process reduces the demand for virgin materials, lowering energy consumption and greenhouse gas emissions. Employing more energy-efficient manufacturing processes and optimizing transportation routes can also minimize the environmental footprint. Investing in research and development of more environmentally friendly interlayer materials is crucial.
Furthermore, promoting the design for disassembly and recyclability of laminated glass units can facilitate end-of-life management and increase the recycling rate. The development of standardized recycling processes and the creation of efficient collection systems are also critical for maximizing the environmental benefits of recycling.
Examples of Initiatives Promoting Sustainable Use of Laminated Glass
Several organizations and manufacturers are actively involved in promoting the sustainable use of laminated glass. The development of industry standards and certifications that promote sustainable manufacturing practices is one such example. Some manufacturers have implemented programs to collect and recycle laminated glass, diverting waste from landfills and recovering valuable materials. Government incentives and policies aimed at encouraging the use of sustainable building materials can also play a vital role.
Initiatives focusing on educating architects, builders, and consumers about the environmental benefits of laminated glass and its sustainable disposal options can further increase its adoption. For example, several green building rating systems, such as LEED, award points for the use of sustainable building materials, including laminated glass produced with recycled content and designed for easy recycling.
Wrap-Up
From its robust impact resistance and sound insulation to its enhanced security features, laminated glass offers a compelling blend of performance and safety. Its versatility shines through its widespread use in various sectors, highlighting its crucial role in modern construction, automotive manufacturing, and beyond. Understanding the different types of interlayers, their properties, and the associated standards ensures informed decision-making in choosing the optimal solution for any specific application.
The future of laminated glass looks bright, with ongoing innovation focused on enhancing its sustainability and expanding its applications further.
Question Bank
Can laminated glass break?
Yes, even laminated glass can break under extreme force. However, the interlayer holds the shattered pieces together, preventing them from scattering and posing a significant safety hazard.
How is laminated glass cleaned?
Cleaning laminated glass is similar to cleaning regular glass. Use a soft cloth, mild detergent, and warm water. Avoid abrasive cleaners or sharp objects.
What is the lifespan of laminated glass?
With proper installation and maintenance, laminated glass can last for many decades, exhibiting excellent durability and longevity.
Is laminated glass more expensive than regular glass?
Yes, laminated glass generally costs more than annealed glass due to the added manufacturing process and materials. However, the enhanced safety and performance often justify the higher cost.
Can laminated glass be recycled?
While recycling laminated glass is more complex than recycling annealed glass, many regions are developing efficient recycling programs for this material, promoting sustainability.