Insulated Glass / Double Glazed Glass: Stepping into a world of enhanced energy efficiency, noise reduction, and architectural design flexibility, we explore the multifaceted nature of insulated glass units (IGUs). From their manufacturing processes and diverse applications to their thermal and acoustic performances, we’ll delve into the science and technology behind these ubiquitous building components. Understanding IGUs is key to creating comfortable, energy-efficient, and sustainable structures.
This guide covers the manufacturing process, detailing the selection of glass types, spacer bar materials, sealant applications, and gas filling techniques. We’ll explore the various types of IGUs available, including laminated and sound-reducing options, and discuss their suitability for different building types and climates. Finally, we’ll examine the energy efficiency, acoustic performance, safety, durability, and lifecycle cost considerations associated with IGUs, providing a comprehensive overview for both professionals and homeowners.
Insulated Glass Manufacturing Process
Insulated glass units (IGUs), also known as double-glazed or double-paned windows, are manufactured through a precise process that combines multiple layers of glass with a sealed air or gas-filled space. This process ensures superior thermal insulation and sound reduction compared to single-pane glass. The manufacturing process involves several key steps, each crucial for the final product’s performance and durability.
The creation of an IGU begins with the careful selection of glass panes. Different types of glass, each offering unique properties, are chosen depending on the desired performance characteristics of the final IGU. These panes are then cleaned meticulously to remove any dust or debris that could compromise the seal. Following cleaning, the spacer bar is inserted between the glass panes.
This spacer maintains the air gap and provides structural support. A sealant is then applied to create a hermetic seal, preventing moisture ingress and maintaining the gas fill. Finally, the unit is filled with a chosen gas, usually argon or krypton, before undergoing a final quality check.
Sealant Types and Properties
Several types of sealants are employed in IGU manufacturing, each with specific properties influencing the unit’s longevity and performance. Butyl sealant, a common choice, provides excellent adhesion and flexibility, accommodating thermal expansion and contraction. Polysulfide sealant offers superior resistance to ultraviolet (UV) degradation, extending the IGU’s lifespan. Finally, silicone sealants are known for their high strength and durability.
The selection of the sealant depends on factors like the climate, the type of spacer bar used, and the desired performance characteristics of the IGU.
Spacer Bar Materials and Energy Efficiency
The spacer bar, positioned between the glass panes, plays a vital role in the IGU’s thermal performance and structural integrity. Aluminum spacers, while cost-effective, are excellent conductors of heat, potentially reducing the IGU’s energy efficiency. Stainless steel spacers offer improved thermal performance compared to aluminum but are more expensive. Warm-edge spacers, incorporating materials with low thermal conductivity like polymer or metal alloys, significantly reduce heat transfer, leading to enhanced energy efficiency.
The choice of spacer bar material directly impacts the overall performance and cost of the IGU.
IGU Manufacturing Process Flowchart
The following flowchart visually represents the steps involved in manufacturing an IGU:
[Start] –> [Glass Selection & Cleaning] –> [Spacer Bar Insertion] –> [Sealant Application (Butyl, Polysulfide, or Silicone)] –> [Gas Filling (Argon, Krypton, or Air)] –> [Quality Check] –> [Final IGU]
Types of Glass Used in IGUs
Different types of glass offer varying properties, influencing the IGU’s overall performance. The table below compares common glass types used in IGU manufacturing.
Glass Type | Description | Properties | Applications |
---|---|---|---|
Annealed Glass | Standard float glass | Relatively inexpensive, brittle | General purpose IGUs |
Tempered Glass | Heat-strengthened glass | High strength, shatters into small, relatively harmless pieces | Safety applications, high-impact areas |
Low-E Glass | Coated glass with low emissivity | Reduces heat transfer, improves energy efficiency | Energy-efficient IGUs |
Types and Applications of Insulated Glass
Insulated glass units (IGUs), also known as double-glazed or even triple-glazed windows, offer significant advantages over single-pane glass. Their construction, involving two or more panes separated by a gas-filled spacer, dramatically improves energy efficiency, sound insulation, and even safety. The specific type of IGU chosen depends heavily on the intended application and the environmental conditions.
Types of Insulated Glass Units
Several variations of insulated glass units cater to diverse needs. Standard IGUs use two panes of annealed glass separated by a spacer filled with air or an inert gas like argon or krypton. Laminated IGUs incorporate a layer of polyvinyl butyral (PVB) interlayer between one or more glass panes, enhancing safety and security by holding the glass together even if broken.
Sound-reducing IGUs often utilize thicker glass panes and specialized spacers to minimize noise transmission. Finally, decorative IGUs offer aesthetic options through the use of patterned, tinted, or coated glass, adding a design element to the window. These options can be combined, for example, a laminated, argon-filled, sound-reducing IGU with a decorative outer pane.
Applications of Insulated Glass in Different Building Types
The benefits of insulated glass make it a versatile material used across various building sectors. The choice of IGU type is tailored to the specific requirements of each application.
- Residential Buildings: Standard IGUs are commonly used in homes to improve energy efficiency, reducing heating and cooling costs. Laminated IGUs offer added security and protection against accidental breakage. Sound-reducing IGUs are beneficial in homes located near busy roads or airports.
- Commercial Buildings: Commercial buildings often utilize IGUs to maximize energy efficiency, reduce noise pollution, and enhance the overall aesthetic appeal. The choice of IGU often depends on the building’s location and function; a skyscraper in a bustling city might benefit from sound-reducing and energy-efficient IGUs, while a quieter office building might prioritize energy efficiency alone.
- Industrial Buildings: Industrial applications may prioritize durability and resistance to extreme temperatures or chemicals. Specialized IGUs with enhanced thermal performance or impact resistance are often employed in industrial settings. For example, a factory near a highway might use a sound-reducing IGU to reduce noise pollution impacting employee productivity.
Benefits of Insulated Glass in Specific Applications
The advantages of insulated glass are particularly pronounced in specific contexts.
- Noise Reduction in Airports: Sound-reducing IGUs with multiple layers of glass and specialized gas fills significantly reduce aircraft noise in buildings near airports, improving comfort and productivity for occupants. The effectiveness of these IGUs is measured in decibels (dB) of noise reduction. For instance, a well-designed IGU might reduce noise levels by 30 dB or more, making a significant difference in a noisy environment.
- Energy Efficiency in Homes: Standard IGUs with argon or krypton gas fillings significantly improve a home’s thermal performance, reducing energy consumption for heating and cooling. The energy savings can translate to substantial cost reductions over the lifespan of the windows, offsetting the initial investment in high-performance IGUs. The energy efficiency is often expressed in terms of U-value (heat transfer coefficient), with lower U-values indicating better insulation.
Insulated Glass in Specialized Environments
IGUs are adapted for use in challenging environments.
- Extreme Temperatures: IGUs designed for extreme temperatures utilize specialized glass types and spacers that can withstand significant thermal stress without compromising performance. These might include low-iron glass for improved solar heat gain control or specialized spacers designed to maintain gas integrity in extreme conditions. Examples include IGUs used in desert climates or high-altitude regions.
- High Humidity: IGUs used in high-humidity environments, such as greenhouses or coastal areas, employ specialized sealants and spacers to prevent moisture condensation and degradation. The choice of sealant and spacer materials is critical in these environments to ensure long-term performance and prevent moisture ingress into the air space between the panes.
Energy Efficiency and Thermal Performance
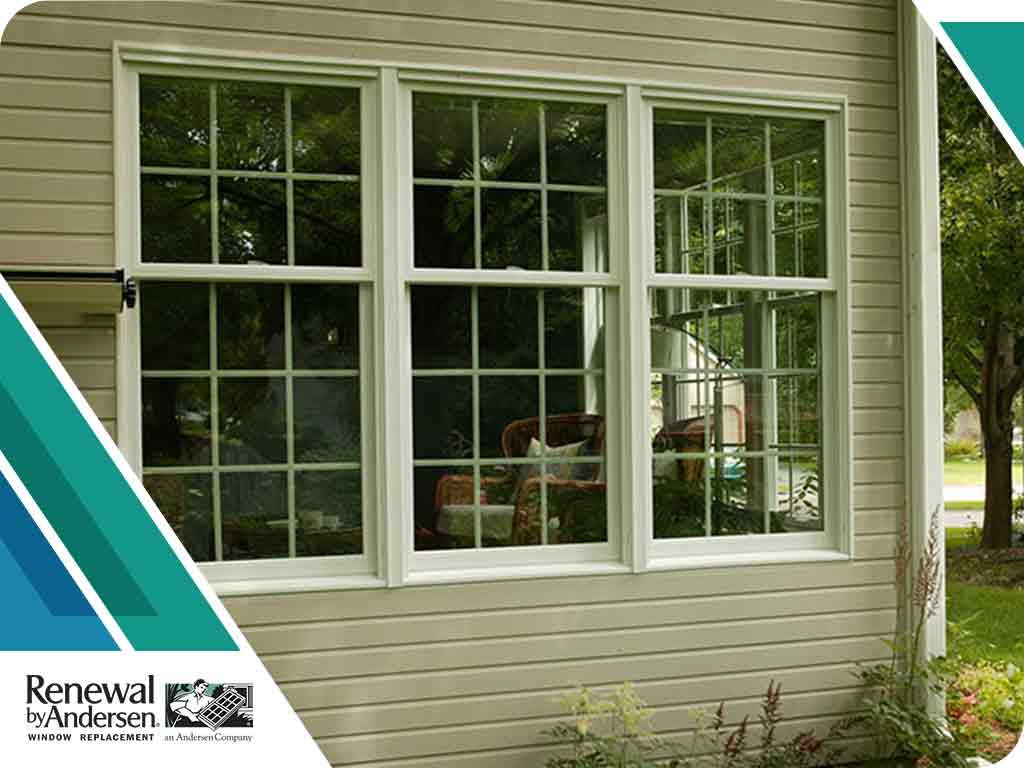
Source: rbakc.com
Insulated glass units (IGUs), also known as double-glazed or triple-glazed windows, significantly impact a building’s energy efficiency. Their thermal performance is determined by a combination of factors, including the type of glass, the gas fill within the cavity, and the spacer bar material. Understanding these factors is crucial for optimizing energy consumption and reducing heating and cooling costs.
Gas Fill Impact on Thermal Performance
The gas trapped between the glass panes plays a crucial role in reducing heat transfer. Air, while the cheapest option, is a relatively poor insulator compared to gases like argon, krypton, and xenon. These heavier noble gases have lower thermal conductivity, meaning they impede heat flow more effectively. Argon is the most commonly used due to its cost-effectiveness and readily available supply.
Krypton offers even better insulation, but at a higher price. Xenon, while the best insulator, is rarely used commercially due to its high cost and limited availability. The difference in performance is noticeable; IGUs filled with argon typically show a 20-30% improvement in thermal performance over air-filled units, while krypton can offer a further 10-15% enhancement.
Comparison of IGUs with Different Gas Fills and Spacer Bars
The choice of spacer bar also affects the IGU’s thermal performance. Traditional aluminum spacer bars conduct heat readily, creating a thermal bridge that reduces the overall insulation value. More modern spacer bars, such as those made of warm-edge materials like stainless steel or super spacers filled with a desiccant, significantly minimize this thermal bridging effect. The combination of a high-performance gas fill (like krypton) and a warm-edge spacer bar results in the best overall thermal performance.
For example, an IGU with krypton gas and a warm-edge spacer will exhibit a considerably lower U-value than one with argon gas and an aluminum spacer.
U-Value and SHGC Relationship to Energy Efficiency
The U-value represents the rate of heat transfer through a material; a lower U-value indicates better insulation. The solar heat gain coefficient (SHGC) represents the fraction of solar radiation that passes through the glass and is converted into heat inside the building. A lower SHGC is desirable in hot climates to reduce cooling loads, while a higher SHGC might be preferred in colder climates to maximize solar heat gain.
For optimal energy efficiency, the IGU needs a balance between low U-value and appropriate SHGC based on climate conditions. For instance, a low U-value is crucial for minimizing heating costs in a cold climate, whereas a low SHGC is essential for reducing cooling costs in a hot climate.
Impact of Low-E Coatings on Energy Efficiency
Low-emissivity (Low-E) coatings are microscopically thin, transparent layers applied to the glass surface. These coatings reflect infrared radiation, reducing heat transfer both inward during summer and outward during winter. Different types of Low-E coatings offer varying levels of performance, and their application can significantly improve both the U-value and SHGC. For example, a Low-E coating can substantially reduce heat loss in winter and solar heat gain in summer, resulting in considerable energy savings.
U-Values and SHGCs for Various IGU Configurations
IGU Configuration | U-Value (W/m²K) | SHGC | Spacer Type |
---|---|---|---|
Air-filled, Clear Glass, Aluminum Spacer | 6.0 | 0.8 | Aluminum |
Argon-filled, Clear Glass, Aluminum Spacer | 3.0 | 0.8 | Aluminum |
Argon-filled, Low-E Glass, Warm-Edge Spacer | 1.5 | 0.3 | Warm-Edge |
Krypton-filled, Low-E Glass, Warm-Edge Spacer | 1.0 | 0.3 | Warm-Edge |
Acoustic Performance of Insulated Glass
Insulated glass units (IGUs), also known as double- or triple-glazed windows, offer significant advantages beyond thermal efficiency. Their construction inherently contributes to sound insulation, making them a valuable asset in noise-reduction applications. The effectiveness of an IGU in reducing noise depends on several interconnected factors.
Factors Affecting Sound Insulation in IGUs
The sound insulation properties of an IGU are determined by a combination of factors, including the thickness and type of glass panes, the spacing between the panes, the type of gas filling the cavity, and the presence of any interlayers like those found in laminated glass. Thicker glass generally offers better sound insulation, as does a wider air or gas-filled cavity.
The type of gas used can also play a role, with some gases offering slightly better acoustic performance than others. Finally, the use of laminated glass significantly enhances the overall sound insulation capabilities.
Relationship Between Glass Pane Thickness and Acoustic Performance
Thicker glass panes generally provide better sound insulation. This is because thicker glass has a greater mass, which effectively dampens sound waves. The increase in sound reduction isn’t directly proportional to the increase in thickness, however; the relationship is more complex and influenced by other factors such as the frequency of the sound. For instance, a 6mm pane might offer a noticeable improvement over a 4mm pane, but the difference between a 10mm and a 12mm pane might be less pronounced.
This highlights the importance of considering the entire IGU design rather than focusing solely on individual component thicknesses.
Sound Reduction Performance of Different IGU Types
Standard IGUs with two or three panes of annealed glass offer a moderate level of sound insulation. Laminated glass IGUs, which incorporate a polyvinyl butyral (PVB) interlayer between glass panes, exhibit significantly improved sound reduction compared to standard units. The PVB interlayer helps to dampen vibrations, reducing the transmission of sound energy. Specialized sound-reducing IGUs often incorporate thicker glass panes, wider air spaces, and may even utilize different gas fillings optimized for acoustic performance.
These specialized units can achieve considerably higher sound reduction levels than standard IGUs. The specific sound reduction performance of an IGU is typically expressed as a Sound Transmission Class (STC) rating, with higher STC values indicating better sound insulation.
Use of Laminated Glass in Enhancing Sound Insulation
Laminated glass plays a crucial role in enhancing the sound insulation performance of IGUs. The PVB interlayer in laminated glass effectively absorbs and dissipates sound energy, preventing its transmission through the glass. This damping effect is particularly effective at higher frequencies. The increased mass of the laminated glass also contributes to its superior sound-reducing capabilities. Combining laminated glass with other sound-reducing techniques, such as wider air spaces or specialized gas fillings, results in even greater sound insulation.
Building Applications Requiring Superior Sound Insulation
Superior sound insulation is critical in various building applications. Hospitals, for instance, often utilize IGUs with enhanced sound-reducing properties to minimize noise disruption in patient rooms and create a more peaceful environment. Schools and universities also benefit from quieter classrooms, enabling better learning conditions. Residential buildings located near busy roads or airports often incorporate IGUs with high STC ratings to mitigate traffic or aircraft noise.
Similarly, sound-sensitive environments such as recording studios and home theaters often utilize IGUs with superior acoustic performance to minimize unwanted noise intrusion. In these applications, IGUs contribute to creating more comfortable and productive environments by significantly reducing noise levels.
Safety and Durability Considerations
Insulated glass units (IGUs), while offering excellent energy efficiency and acoustic performance, require careful consideration of safety and long-term durability. The choice of glass type, the quality of the sealant and spacer bar, and proper installation all significantly impact the lifespan and safety of the IGU. Environmental factors also play a crucial role in determining the longevity of these units.
Safety Aspects of Different Glass Types in IGUs
The selection of glass type within an IGU is paramount for safety. Tempered glass, also known as safety glass, is significantly stronger than annealed glass and breaks into small, relatively harmless pieces upon impact, reducing the risk of serious injury. Laminated glass, another safety option, holds together even when broken, preventing shards from scattering. The use of tempered glass is particularly important in applications where impact is likely, such as storefront windows or skylights.
In high-risk areas, combining tempered and laminated glass in an IGU provides an even higher level of safety. For instance, a tempered inner pane and a laminated outer pane offers protection from both impact and penetration.
Factors Influencing the Long-Term Durability of IGUs
Several factors contribute to the long-term durability of IGUs. The most critical is the quality and performance of the sealant, which creates an airtight and moisture-resistant seal between the panes of glass. Sealant degradation, caused by UV exposure, temperature fluctuations, and chemical reactions, is a major cause of IGU failure. The spacer bar, which maintains the gap between the panes, is also susceptible to corrosion, especially if made of low-quality materials.
Corrosion can lead to sealant failure and the ingress of moisture, compromising the IGU’s performance and lifespan. The type of gas filling within the IGU also affects its durability; argon and krypton are more stable than air, and less prone to leakage.
Impact of Environmental Factors on IGU Performance and Lifespan
Environmental factors significantly impact IGU performance and lifespan. Extreme temperature fluctuations cause stress on the sealant and spacer bar, accelerating degradation. High humidity can lead to condensation and moisture ingress, promoting corrosion and fungal growth within the IGU. UV radiation from sunlight degrades the sealant, reducing its effectiveness over time. In coastal areas, salt spray can accelerate corrosion of the spacer bar and affect sealant performance.
For example, IGUs in desert climates might experience accelerated sealant degradation due to intense UV radiation and extreme temperature swings, while those in humid tropical regions might be prone to condensation and mold growth.
Recommendations for Proper Installation and Maintenance
Proper installation and regular maintenance are crucial for ensuring the longevity of IGUs. Careful handling during installation is vital to avoid damage to the glass or sealant. The IGU should be securely fastened to the frame to prevent movement and stress on the unit. Regular inspection for signs of sealant failure, such as fogging or condensation, is essential.
Prompt repair or replacement of damaged IGUs prevents further deterioration and ensures continued performance. Cleaning should be done with soft cloths and mild detergents, avoiding harsh chemicals or abrasive cleaners that can damage the glass surface or sealant.
IGU Quality and Integrity Inspection Checklist
Before accepting the installation, a thorough inspection is recommended.
- Visual Inspection: Check for any cracks, chips, or scratches on the glass panes. Look for signs of sealant failure, such as fogging, discoloration, or bubbling.
- Sealant Integrity: Carefully examine the sealant around the perimeter of the IGU for any gaps or imperfections. A continuous, unbroken sealant is crucial for optimal performance.
- Spacer Bar Condition: Inspect the spacer bar for signs of corrosion or damage. Corrosion can indicate a potential problem with the IGU’s long-term durability.
- Gas Fill (if applicable): If the IGU is filled with argon or krypton, verify the gas type and quantity if documentation is available. Significant gas leakage indicates a problem.
- Proper Installation: Ensure the IGU is securely fastened to the frame and properly sealed to prevent air leakage.
Cost and Lifecycle Analysis of Insulated Glass
Choosing insulated glass units (IGUs) involves careful consideration of upfront costs and long-term savings. The initial investment can vary significantly depending on the chosen specifications, and understanding the lifecycle cost is crucial for making informed decisions. This analysis explores the various cost factors associated with IGUs, allowing for a comprehensive comparison of different options.
Initial Cost Comparison of IGU Types
The initial cost of IGUs is influenced by several factors, including the type of glass used (e.g., clear, low-E, tinted), the number of panes, the gas fill (argon, krypton, or air), and the spacer type. Generally, simpler configurations with standard clear glass and air filling will be the least expensive. More advanced IGUs featuring low-E coatings, noble gas fills, and enhanced spacer systems will command higher prices.
For example, a basic double-pane IGU with clear glass and air might cost around $10-$20 per square foot, while a triple-pane IGU with low-E coatings and argon fill could cost $30-$50 or more per square foot. These figures are estimates and can vary based on region, supplier, and volume.
Long-Term Cost Savings from Energy Efficiency
The energy efficiency improvements offered by IGUs translate into significant long-term cost savings. By reducing heat transfer, IGUs lower heating and cooling loads, resulting in lower energy bills. The magnitude of these savings depends on factors like climate, building design, and the IGU’s performance characteristics. For instance, a homeowner in a cold climate might see a substantial reduction in their winter heating costs, while someone in a hot climate could experience significant savings on summer cooling expenses.
These savings can accumulate over the lifespan of the IGU, potentially offsetting the higher initial cost of a more energy-efficient unit. A well-insulated home might see a return on investment in a few years through reduced energy consumption.
Factors Contributing to Overall Lifecycle Cost, Insulated Glass / Double Glazed Glass
The lifecycle cost of an IGU encompasses not only the initial purchase price but also installation costs, potential maintenance expenses, and the long-term energy savings. Installation costs can vary depending on the complexity of the project and the installer’s labor rates. While IGUs are generally low-maintenance, potential issues such as seal failure can lead to repair or replacement costs.
Therefore, selecting high-quality IGUs from reputable manufacturers can minimize the risk of premature failure and reduce long-term expenses. Furthermore, the expected lifespan of the IGU plays a significant role in the overall lifecycle cost calculation. A longer-lasting IGU will generally result in lower overall costs over its operational life.
Cost-Saving Strategies in IGU Selection and Installation
Several strategies can help minimize the overall cost of IGUs. Careful consideration of the climate and building design can help determine the optimal IGU specifications, avoiding unnecessary features that add to the cost without providing significant additional benefits. Obtaining multiple quotes from different suppliers can help identify competitive pricing. Choosing experienced and reputable installers can ensure proper installation, preventing future problems and associated costs.
Taking advantage of any available rebates or tax incentives for energy-efficient upgrades can further reduce the overall cost. Finally, bulk purchasing can sometimes lead to lower per-unit costs.
Cost Comparison and Lifecycle Analysis of Various IGU Options
IGU Type | Initial Cost ($/sq ft) | Estimated Annual Energy Savings ($) | Estimated Lifespan (Years) |
---|---|---|---|
Basic Double-Pane (Air) | 10-20 | 50-100 | 20 |
Double-Pane (Argon, Low-E) | 20-30 | 150-250 | 25 |
Triple-Pane (Argon, Low-E) | 30-50 | 250-400 | 30 |
Note
These are estimated figures and can vary significantly based on location, climate, building design, and specific product specifications. Consult with local suppliers for accurate pricing and performance data.
Wrap-Up
Ultimately, insulated glass/double glazed glass offers a powerful combination of energy efficiency, noise reduction, and enhanced safety. By carefully considering the various factors discussed – from glass type and gas fill to spacer bar material and installation – you can make informed decisions to optimize the performance and longevity of your IGUs. Whether you’re a builder, architect, or homeowner, understanding the nuances of IGUs is crucial for creating buildings that are both comfortable and sustainable.
Frequently Asked Questions: Insulated Glass / Double Glazed Glass
What is the lifespan of insulated glass units?
With proper installation and maintenance, IGUs can last for 20 years or more. However, factors like sealant degradation and spacer bar corrosion can affect their lifespan.
Can I repair a damaged IGU?
Generally, repairing a damaged IGU is not cost-effective. Replacement is usually the better option.
How do I clean insulated glass?
Use a soft cloth and a mild detergent solution. Avoid abrasive cleaners or scrapers.
Are IGUs recyclable?
Yes, many components of IGUs are recyclable, although the process may vary depending on local facilities.
What are the different types of gas fills used in IGUs?
Common gas fills include argon, krypton, and xenon. Krypton offers the best thermal performance, but is more expensive.