Float Glass: The seemingly simple sheet of glass we encounter daily is a marvel of modern manufacturing. Its ubiquitous presence, from skyscrapers to smartphones, masks a sophisticated production process that dates back to the mid-20th century. This process, known as the float glass method, revolutionized glassmaking, enabling the mass production of high-quality, flat glass at an unprecedented scale.
We’ll delve into the fascinating history, intricate manufacturing process, diverse applications, and promising future of this essential material.
From the molten glass bath to the final polishing, the journey of a float glass sheet is a testament to human ingenuity. The precise control over temperature, composition, and atmosphere ensures the creation of a remarkably uniform and optically clear product. Understanding this process reveals the remarkable properties that make float glass so versatile and indispensable in modern society.
This exploration will cover everything from the fundamental chemical properties to the evolving market trends and future innovations shaping the industry.
Float Glass Manufacturing Process
Float glass, the ubiquitous flat glass used in windows, mirrors, and countless other applications, is produced through a remarkably elegant and efficient process. This method, developed in the mid-20th century, revolutionized glassmaking, allowing for the mass production of high-quality, flat sheets with unparalleled consistency. The process relies on the unique properties of molten glass and a bath of molten tin to achieve its remarkable results.
The Steps Involved in Float Glass Manufacturing
The float glass process involves several key stages, transforming raw materials into the pristine sheets we see everywhere. These stages are carefully controlled to ensure the final product meets stringent quality standards.
Stage | Description | Temperature (°C) | Image Description |
---|---|---|---|
Batching and Melting | Raw materials (sand, soda ash, limestone, etc.) are precisely mixed and fed into a furnace where they melt at extremely high temperatures. | 1500-1600 | A large, intensely hot furnace where raw materials are melted into a homogenous molten glass. The furnace is likely lined with refractory bricks to withstand the extreme temperatures. Molten glass flows from a spout or outlet at the furnace’s base. |
Float Bath | The molten glass flows onto a bath of molten tin, where it floats and spreads out, forming a flat sheet. Gravity and surface tension ensure the glass remains flat. | 1000-1100 | Molten glass flows smoothly onto a bath of molten tin, spreading evenly across the surface. The molten tin is contained within a long, narrow, and precisely leveled trough. The molten glass floats on top, guided by the tin’s surface. |
Cooling and Annealing | The glass sheet slowly cools on the tin bath to reduce internal stresses. This annealing process is crucial for preventing cracking and breakage. | Gradually decreasing to room temperature | The flat sheet of glass moves slowly along a long cooling chamber, gradually decreasing in temperature to prevent thermal shock. Workers may be visible through safety glass monitoring the process. |
Cutting and Finishing | The cooled glass sheet is inspected, cut to size, and then undergoes further finishing processes, such as edging and polishing, to achieve the desired final product. | Room temperature | Large sheets of glass are cut into smaller sizes using diamond-tipped saws. The edges are then refined to remove any imperfections. Inspection stations ensure quality control before packaging. |
The Role of Tin in the Float Glass Process
Molten tin plays a crucial role in the float glass process. Its unique properties—high density, low viscosity, and a relatively low melting point—make it ideal for creating a perfectly flat surface for the molten glass to float on. The tin’s surface tension, combined with the glass’s own surface tension, ensures a smooth, uniform sheet. The tin bath also protects the glass from contamination and allows for controlled cooling.
Furthermore, tin’s inert nature prevents it from chemically reacting with the molten glass, ensuring the quality and clarity of the final product.
Float Glass Compared to Older Glassmaking Techniques
Older glassmaking techniques, such as crown glass and cylinder glass methods, were labor-intensive and produced smaller, less uniform sheets of glass with inherent imperfections. These methods involved hand-blowing or shaping the glass, resulting in significant variations in thickness and flatness. The float glass process offers a significant advantage through automation and precise control, leading to large, consistently flat sheets with superior optical quality and reduced production costs.
Quality Control Measures in Float Glass Production
Rigorous quality control measures are implemented throughout the float glass manufacturing process. These measures ensure that the final product meets stringent specifications for flatness, thickness, optical clarity, and surface quality. Continuous monitoring of temperature, glass flow, and other parameters is crucial. Automated inspection systems are used to detect and reject any defects. Regular sampling and testing also guarantee consistency and compliance with industry standards.
Properties and Characteristics of Float Glass
Float glass, renowned for its exceptional flatness and optical clarity, is a ubiquitous material in various applications. Its unique properties stem from the manufacturing process itself, which results in a consistent, high-quality product. Understanding these properties is crucial for selecting the appropriate type of glass for specific needs.
Physical and Chemical Properties of Float Glass
Float glass possesses a unique combination of physical and chemical properties that make it suitable for a wide range of applications. These characteristics are largely determined by its composition, primarily silica (SiO2), and the manufacturing process.
- Optical Clarity: Float glass exhibits high optical clarity, meaning it transmits light with minimal distortion or scattering. This makes it ideal for applications requiring high visual fidelity, such as windows and display screens.
- Strength: While not inherently the strongest type of glass, float glass possesses sufficient tensile and compressive strength for many applications. Its strength can be further enhanced through tempering or other strengthening techniques.
- Thermal Stability: Float glass demonstrates good thermal stability, meaning it can withstand moderate temperature changes without significant cracking or breakage. However, rapid or extreme temperature fluctuations can still cause damage.
- Chemical Resistance: Float glass is relatively resistant to most chemicals, making it suitable for use in environments where exposure to chemicals is possible. However, it’s not impervious to all chemicals; strong acids and alkalis can affect its surface over time.
- Surface Finish: Float glass has a smooth, flat surface with minimal imperfections, contributing to its optical clarity and making it easy to coat or process further.
- Dimensional Stability: The float glass manufacturing process results in highly consistent dimensions, making it suitable for applications requiring precise tolerances.
Types of Float Glass and Their Applications
The versatility of float glass is further enhanced by the availability of different types, each tailored for specific applications. These variations often involve coatings or treatments applied to the base float glass.
- Standard Float Glass: This is the most common type, used extensively in windows, mirrors, and other general applications where high optical clarity and flatness are needed.
- Coated Float Glass: Various coatings can be applied to float glass to enhance its performance. Low-E coatings improve energy efficiency by reducing heat transfer, while solar control coatings reduce glare and heat gain. Anti-reflective coatings enhance visibility and reduce glare.
- Laminated Float Glass: This type consists of two or more layers of float glass bonded together with an interlayer, typically polyvinyl butyral (PVB). This provides increased safety and security, as the interlayer holds the glass fragments together in case of breakage.
- Toughened (Tempered) Float Glass: Heat treatment strengthens float glass, significantly increasing its impact resistance. Tempered glass is used in applications where safety and durability are paramount, such as automotive windshields and shower doors.
Environmental Impact of Float Glass Production and Mitigation Strategies
The production of float glass has an environmental impact, primarily due to energy consumption in the melting process and emissions of greenhouse gases. However, significant strides are being made to reduce the carbon footprint of float glass manufacturing.
Significant energy is required for the high-temperature melting process, leading to greenhouse gas emissions. The use of recycled glass cullet in the manufacturing process can substantially reduce energy consumption and emissions. Furthermore, advancements in furnace technology and increased energy efficiency are continuously improving the environmental profile of float glass production. Investing in renewable energy sources to power manufacturing facilities further contributes to reducing the environmental impact.
Comparison of Float Glass with Other Glass Types
The following table compares the properties of float glass with borosilicate and tempered glass.
Property | Float Glass | Borosilicate Glass | Tempered Glass |
---|---|---|---|
Thermal Shock Resistance | Moderate | High | High |
Chemical Resistance | Good | Excellent | Good |
Strength | Moderate | Moderate | High |
Optical Clarity | Excellent | Excellent | Excellent |
Cost | Relatively Low | Relatively High | Higher than Float Glass |
Applications of Float Glass
Float glass, due to its exceptional clarity, flatness, and strength, finds applications across a vast range of industries. Its versatility and cost-effectiveness make it a ubiquitous material in modern life, shaping everything from the buildings we inhabit to the vehicles we drive. The following sections explore its diverse uses and the industries that rely heavily on this remarkable product.
Diverse Applications of Float Glass Across Industries
Float glass’s widespread use stems from its desirable properties. Its exceptional flatness and optical clarity make it ideal for numerous applications, while its strength and durability ensure longevity. The following list categorizes its diverse applications across various sectors.
- Architectural: Windows, curtain walls, facades, skylights, doors, partitions.
- Automotive: Windshields, side and rear windows, sunroofs.
- Electronics: Touchscreens, displays, solar panels.
- Household Appliances: Oven doors, microwave doors, refrigerator shelves.
- Furniture: Tabletops, shelves, decorative elements.
- Transportation: Train windows, aircraft windows, bus windows.
- Artwork and Decoration: Paintings on glass, decorative glass panels, stained glass.
Innovative Uses of Float Glass in Modern Architecture and Design
Modern architecture and design are constantly pushing the boundaries of what’s possible with float glass. Its inherent properties lend themselves to creative and functional applications that enhance both aesthetics and performance.
- Curved Glass Facades: Buildings are increasingly featuring curved glass facades, creating stunning visual effects while maximizing natural light. The precise manufacturing process of float glass allows for the creation of complex, curved shapes without compromising structural integrity. Imagine a skyscraper with a gently curving glass exterior that reflects the city skyline, changing subtly throughout the day.
- Double-Skin Facades: These systems use two layers of glass with an air gap between them to improve insulation and reduce energy consumption. The inner layer provides protection from the elements while the outer layer acts as a sunshade, controlling heat gain and glare. This design enhances energy efficiency and provides superior climate control within the building.
- Glass Flooring and Walkways: Float glass’s strength and transparency make it a striking material for creating glass floors and walkways, adding dramatic visual impact to interior and exterior spaces. Imagine a modern home with a glass floor offering a view into a stunning garden below, or a walkway suspended above a bustling city street.
Top Five Industries Consuming Float Glass Globally
The construction, automotive, and electronics industries are the largest consumers of float glass worldwide, driven by high demand for energy-efficient buildings, advanced vehicles, and sophisticated electronic devices.
- Construction: The building and construction industry remains the largest consumer, driven by the ongoing need for windows, facades, and other glass elements in residential, commercial, and infrastructure projects. The sheer volume of buildings constructed globally ensures a consistent and high demand for float glass.
- Automotive: The automotive industry’s use of float glass in windshields, side and rear windows, and sunroofs is significant, with growth fueled by increasing vehicle production worldwide and the demand for safety and improved visibility.
- Electronics: The electronics industry uses substantial quantities of float glass for touchscreens, displays, and solar panels, reflecting the booming global demand for smartphones, tablets, and renewable energy solutions. The trend towards larger and higher-resolution screens further increases this demand.
- Appliances: The manufacture of household appliances such as ovens, microwaves, and refrigerators requires significant quantities of float glass for oven doors, shelves, and other components. The global demand for these appliances, coupled with technological advancements, sustains this sector’s glass consumption.
- Solar Energy: The rapid growth of the renewable energy sector significantly impacts float glass consumption. Solar panels utilize large amounts of glass for protection and light transmission, and as solar technology continues to evolve and become more affordable, this sector’s demand is expected to increase considerably.
A Novel Application: Self-Cleaning Float Glass for Public Transportation
A potential new application involves incorporating self-cleaning properties into float glass for use in public transportation vehicles like buses and trains. This could be achieved by coating the glass with a photocatalytic material that breaks down dirt and grime when exposed to sunlight, reducing the need for frequent cleaning and improving hygiene.The benefits include reduced maintenance costs for transit agencies, improved passenger comfort due to cleaner windows, and enhanced visibility for drivers and passengers.
However, challenges include developing a durable and cost-effective coating that can withstand the harsh environmental conditions experienced by public transportation vehicles, ensuring long-term effectiveness and maintaining transparency. Further research is needed to overcome these challenges and fully realize the potential of this innovative application.
Float Glass Market and Industry
The global float glass market is a dynamic sector influenced by a complex interplay of factors impacting both supply and demand. Growth is driven by construction activity, particularly in developing economies, while challenges arise from fluctuating raw material costs and environmental regulations. Understanding the market trends, major players, economic influences, and technological advancements is crucial for navigating this competitive landscape.Global Market Trends and Influencing FactorsThe global float glass market exhibits significant regional variations.
Demand in Asia, particularly China and India, remains strong due to rapid urbanization and infrastructure development. Conversely, mature markets in North America and Europe demonstrate more stable, albeit slower, growth. Supply is largely influenced by the availability and cost of raw materials like silica sand and soda ash, as well as energy prices, which are critical for the energy-intensive float glass manufacturing process.
Environmental regulations, focusing on reducing greenhouse gas emissions and waste, also play a significant role in shaping the industry’s operational landscape and influencing production costs. Furthermore, the increasing demand for energy-efficient glass products, such as low-E glass, is driving innovation and market expansion in specialized segments.
Major Float Glass Manufacturers and Market Share
Several companies dominate the global float glass market, each with varying geographical strengths and product portfolios. While precise market share data fluctuates, companies like AGC Inc., NSG Group (Nippon Sheet Glass), and Guardian Glass consistently rank among the leading players. These manufacturers often operate globally, catering to diverse regional markets. Their market share is influenced by factors such as production capacity, technological advancements, strategic partnerships, and their ability to meet the specific demands of different regions.
For instance, a manufacturer with strong manufacturing facilities in Asia might hold a larger market share in that region compared to a competitor with a stronger presence in Europe. Competition is fierce, with companies vying for market share through price competitiveness, product differentiation, and expansion into new markets.
Economic Factors Impacting Float Glass Price and Availability
The price and availability of float glass are subject to significant economic fluctuations. Raw material costs, particularly silica sand and soda ash, have a direct impact on production expenses. Fluctuations in energy prices, a major input for the float glass manufacturing process, further amplify price volatility. Global economic conditions also play a role; during periods of economic downturn, demand for construction materials, including float glass, tends to decrease, leading to price adjustments.
Conversely, periods of robust economic growth typically drive up demand, potentially leading to price increases and potential shortages. Government policies, including tariffs and trade regulations, can also influence both price and availability by impacting the import and export of float glass products. For example, increased tariffs on imported float glass could lead to higher prices for domestic consumers.
Technological Advancements in the Float Glass Industry
Technological advancements are continuously reshaping the float glass industry, driving efficiency improvements and expanding product capabilities. Innovations in furnace design, for example, enhance energy efficiency and reduce emissions. Advanced coating technologies are enabling the production of more sophisticated glass products, such as self-cleaning glass and solar control glass, catering to a growing demand for specialized functionalities. Automation and digitalization are improving production processes, optimizing resource utilization, and enhancing quality control.
Research and development efforts focus on creating even more energy-efficient and environmentally friendly float glass products, responding to increasing sustainability concerns. For instance, the development of new coating materials that improve insulation properties leads to energy savings and reduces reliance on artificial heating and cooling.
Future Trends in Float Glass Technology
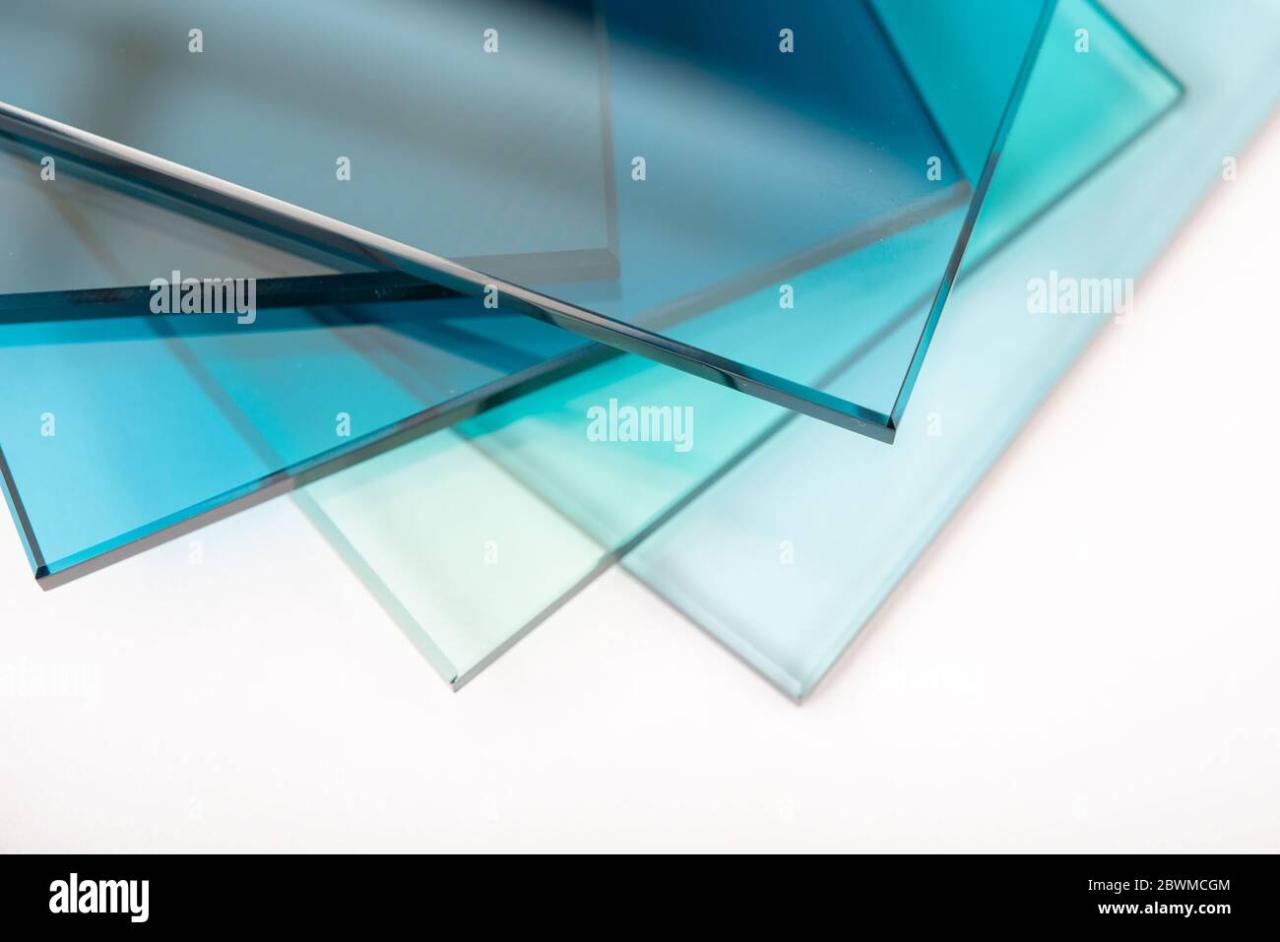
Source: alamy.com
The float glass industry is poised for significant transformation in the coming years, driven by increasing demands for sustainability, enhanced performance, and innovative applications. Advancements in manufacturing techniques, coupled with the integration of new technologies, will shape the future of this crucial material.The pursuit of greater efficiency and reduced environmental impact is a primary driver of innovation. This translates into a focus on reducing energy consumption during the manufacturing process, minimizing waste, and exploring alternative, more sustainable raw materials.
Furthermore, the development of new glass compositions with enhanced properties, such as improved strength, thermal insulation, and self-cleaning capabilities, is another key area of development.
Sustainable and Efficient Manufacturing Processes
Significant progress is expected in reducing the energy intensity of float glass production. This will involve optimizing furnace design and operation, exploring alternative fuels, and implementing advanced heat recovery systems. For example, research into using renewable energy sources, such as solar or geothermal power, to supply the substantial energy needs of float glass furnaces is actively underway. Additionally, the development of more efficient cooling systems and improved waste management strategies will contribute to a greener production process.
Companies are also exploring ways to utilize industrial byproducts or recycled materials in the manufacturing process, further reducing reliance on virgin resources.
Emerging Applications of Float Glass
Float glass is increasingly integrated into advanced technologies, expanding its applications beyond traditional uses. Smart windows, for example, are gaining popularity, incorporating features such as electronically controlled tinting for improved energy efficiency and light management. These windows can dynamically adjust their transparency based on external factors like sunlight intensity and temperature, reducing the need for artificial lighting and air conditioning.
Furthermore, the integration of float glass into solar panels is another exciting development. Float glass serves as a crucial substrate for photovoltaic cells, and advancements in its production are leading to higher efficiency and more durable solar panels. This integration offers a path towards more aesthetically pleasing and cost-effective solar energy solutions.
A Vision of a Future Float Glass Production Facility
Imagine a futuristic float glass production facility, powered primarily by renewable energy sources. The facility is designed with a focus on minimizing its environmental footprint, incorporating closed-loop water recycling systems and advanced waste heat recovery technologies. Automated guided vehicles (AGVs) transport raw materials and finished products efficiently throughout the facility, minimizing human intervention and improving safety. The furnace itself is a marvel of engineering, optimized for minimal energy consumption and maximum output.
Real-time monitoring systems ensure optimal operating conditions, maximizing efficiency and minimizing waste. The facility also incorporates advanced robotics and AI-driven systems for quality control and predictive maintenance, minimizing downtime and maximizing productivity.
Challenges and Opportunities in the Next Decade
The float glass industry faces both challenges and opportunities in the coming decade. Increased competition from alternative materials, fluctuating raw material prices, and the need for continuous innovation to meet evolving market demands are significant challenges. However, the growing demand for energy-efficient building materials, the expansion of renewable energy technologies, and the development of new applications for float glass present substantial opportunities for growth and innovation.
Companies that successfully navigate these challenges and capitalize on these opportunities will be well-positioned for success in the future. For instance, companies investing in research and development of new glass compositions with enhanced properties, such as self-cleaning or antimicrobial capabilities, will be better placed to capture market share in the growing niche markets.
Last Recap
Float glass, a seemingly simple material, has profoundly shaped our world. Its journey, from the innovative float process to its diverse applications in countless industries, is a story of continuous improvement and adaptation. As we look toward the future, the potential for innovation in float glass technology remains immense, promising even more sustainable, efficient, and technologically advanced applications. The ongoing evolution of this fundamental material will undoubtedly continue to influence architectural design, technological advancements, and the very fabric of our daily lives.
FAQs
What are the main differences between float glass and annealed glass?
While both are made from molten glass, float glass is made using the float process resulting in a flatter, more uniform sheet. Annealed glass, on the other hand, may have minor imperfections and variations in thickness.
Can float glass be recycled?
Yes, float glass is highly recyclable. It can be crushed and re-melted to create new glass products, reducing the need for raw materials and lowering the environmental impact.
How is the thickness of float glass controlled?
The thickness is precisely controlled during the float process by adjusting the speed of the glass ribbon moving across the molten tin bath and the temperature gradients.
What are the safety considerations when working with float glass?
Float glass, while relatively strong, can still shatter. Appropriate safety glasses and handling techniques should always be used to avoid injury from broken pieces.
Is float glass suitable for all applications?
While versatile, float glass might not be ideal for applications requiring extreme heat resistance or impact strength. Other types of glass, like borosilicate or tempered glass, might be better suited in those cases.