Bulletproof glass, far from being a simple concept, is a marvel of layered engineering and scientific innovation. This seemingly impenetrable barrier protects against high-velocity projectiles, and its creation involves a complex process of layering different types of glass and polymers. From its use in high-security buildings to its presence in everyday vehicles, bulletproof glass safeguards lives and property across a wide spectrum of applications.
We’ll delve into the science behind its creation, its impressive performance capabilities, and its evolving future.
This exploration covers the manufacturing process, the rigorous testing standards, the diverse applications across various industries, crucial maintenance tips, and exciting advancements shaping the future of bulletproof glass technology. We’ll uncover the secrets behind its strength, exploring the materials used, the manufacturing techniques employed, and the ongoing research that pushes the boundaries of this vital protective material.
Composition and Manufacturing of Bulletproof Glass
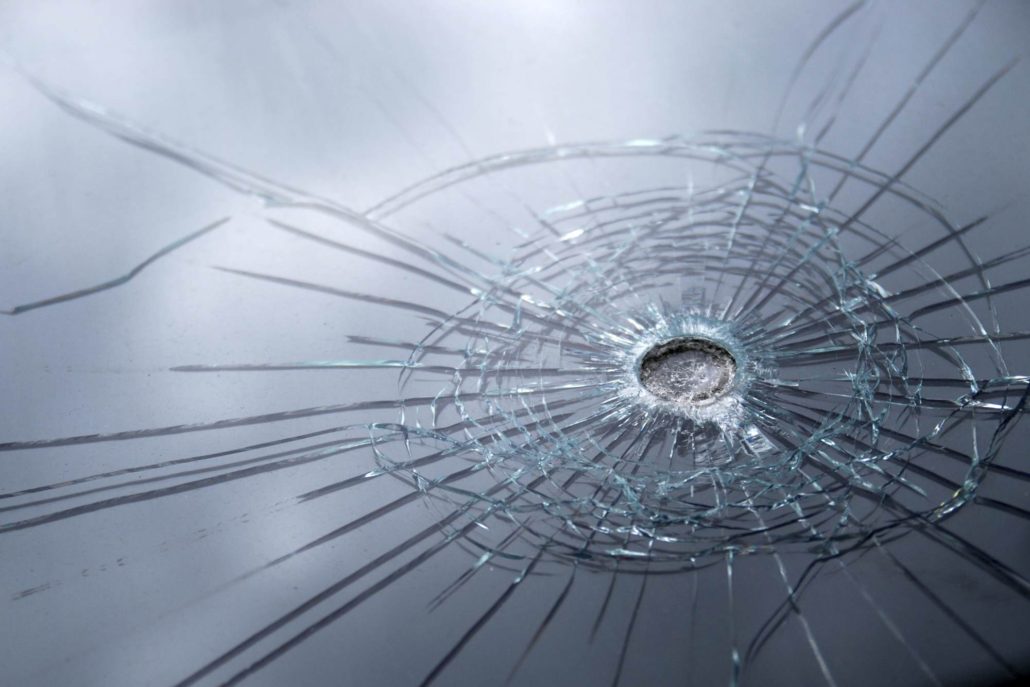
Source: hongjiaglass.com
Bulletproof glass, also known as ballistic glass, isn’t a single material but a sophisticated composite designed to withstand high-velocity projectiles. Its effectiveness relies on a carefully engineered combination of materials and manufacturing processes, creating a layered structure that dissipates impact energy.
Bulletproof glass is renowned for its ability to withstand high-impact projectiles, a crucial feature in security applications. However, a related concept is that of reinforced glass, like Wired Glass , which uses a metal mesh embedded within to increase strength and prevent shattering. While not bulletproof, this type of glass offers enhanced security and is often used in windows where impact resistance is desired, contrasting with the extreme protection offered by true bulletproof glass.
Layered Structure of Bulletproof Glass
Bulletproof glass typically consists of multiple layers of glass and a strong, flexible interlayer. A common configuration involves alternating layers of hard, brittle glass and a softer, more pliable interlayer material, often a type of polycarbonate or polyvinyl butyral (PVB). The glass layers provide the initial resistance to impact, while the interlayer holds the shattered glass fragments together, preventing penetration.
The number of layers and the specific materials used depend on the desired level of protection. For example, a higher threat level might require more layers of thicker, stronger glass.
Lamination Process
The layers of glass and interlayer are laminated together using a high-pressure, high-temperature process. The interlayer, acting as an adhesive, bonds firmly to the glass sheets. This process creates a strong, monolithic structure that can withstand significant impact. During lamination, the heat and pressure cause the interlayer to flow and bond completely to the glass surfaces, creating a near seamless bond.
The resulting laminated sheet is then cut to size and further processed as needed.
Types of Glass Used in Bulletproof Glass Production
Several types of glass are used in bulletproof glass, each offering unique properties. Common choices include soda-lime glass (the most common type of glass), borosilicate glass (known for its high heat resistance), and tempered glass (strengthened through a process of heating and rapid cooling). The selection depends on factors such as the desired level of protection, the weight requirements, and the overall cost.
For instance, soda-lime glass might be used in less demanding applications, while borosilicate glass could be incorporated for applications requiring greater heat resistance, and tempered glass increases the overall strength of the panel.
Comparison of Bulletproof Glass Compositions
The table below compares the strengths and weaknesses of various bulletproof glass compositions. Note that specific properties can vary significantly depending on the manufacturer and the exact composition.
Composition | Strengths | Weaknesses | Typical Applications |
---|---|---|---|
Soda-lime glass with PVB interlayer (multiple layers) | Relatively inexpensive, readily available | Lower ballistic resistance compared to other compositions | Lower-threat applications, vehicle windows |
Tempered glass with PVB interlayer (multiple layers) | Higher impact resistance than soda-lime, shatter resistance | More expensive than soda-lime, can still be penetrated by high-velocity projectiles | Medium-threat applications, bank teller windows |
Borosilicate glass with polycarbonate interlayer (multiple layers) | High heat resistance, excellent ballistic performance | Expensive, heavier than other options | High-threat applications, armored vehicles, security installations |
Hybrid compositions (e.g., combining different glass types and interlayers) | Tailored properties for specific threat levels, optimized for weight and cost | Complex manufacturing process, potentially higher cost | Custom applications requiring specialized protection levels |
Ballistic Performance and Testing
Bulletproof glass, despite its name, doesn’t offer absolute protection. Its effectiveness hinges on its ability to withstand the impact of projectiles, a performance rigorously evaluated through standardized testing procedures. Understanding these tests and the factors influencing performance is crucial for assessing the suitability of bulletproof glass for specific applications.
Standardized tests subject bulletproof glass to controlled impacts from various projectiles to determine its resistance. The results define the glass’s protection level, specifying the types and calibers of ammunition it can effectively stop.
Bulletproof glass is incredibly strong, designed to withstand high-impact projectiles. Its strength comes from its layered construction, often incorporating multiple layers of glass and a tough interlayer. A key component understanding this process is learning about the basics of Laminated Glass , which forms the foundation for many bulletproof glass designs. The same principles of layering and interlayer bonding are used to create the exceptional resilience of bulletproof glass.
Standardized Ballistic Tests, Bulletproof Glass
Several international standards define the methods for testing bullet-resistant glass. These tests typically involve firing projectiles of specific caliber and velocity at the glass sample at a controlled angle and distance. The outcome is assessed based on whether the projectile penetrates the glass, and if so, to what extent. Key parameters measured include the projectile’s velocity before and after impact, the size and shape of any resulting damage, and the overall structural integrity of the glass after the test.
Organizations like the Underwriters Laboratories (UL) and the National Institute of Justice (NIJ) provide standardized testing procedures and certifications for bullet-resistant materials. These certifications are crucial for ensuring that the glass meets specific performance requirements.
Impact of Projectile Type on Performance
The type of projectile significantly influences the performance of bulletproof glass. Factors like caliber (diameter), mass, shape, and velocity directly affect the energy transferred to the glass upon impact. Larger caliber, heavier projectiles traveling at higher velocities will naturally exert more force, demanding greater resistance from the glass. For example, a .44 Magnum round, known for its high energy, will pose a significantly greater challenge to bulletproof glass than a smaller caliber like a .22.
The shape of the projectile also plays a role; pointed projectiles tend to concentrate force more effectively than rounded ones, potentially leading to easier penetration.
Factors Affecting Penetration Resistance
Beyond projectile characteristics, several environmental and material factors influence the penetration resistance of bulletproof glass. Temperature fluctuations can affect the glass’s mechanical properties, potentially impacting its ability to withstand impact. Extreme cold might make the glass more brittle, while extreme heat can weaken its structure. The angle of impact also plays a critical role; oblique impacts (non-perpendicular) often distribute the force over a larger area, reducing the stress concentration at the point of impact and thus increasing the chance of the projectile being deflected.
Finally, the condition of the glass itself, such as the presence of flaws or damage, can significantly compromise its ballistic performance.
Performance of Different Bulletproof Glass Types
The following table illustrates the performance of various bulletproof glass types against different projectiles. Note that these are illustrative examples, and actual performance can vary based on specific manufacturing processes and testing conditions.
Bulletproof Glass Type | Projectile Type | Velocity (m/s) | Penetration Result |
---|---|---|---|
Single-layer laminated glass | 9mm Parabellum | 350 | Penetration |
Multi-layer laminated glass | 9mm Parabellum | 350 | No Penetration |
Multi-layer laminated glass with polycarbonate | .44 Magnum | 400 | Partial Penetration (Crack) |
High-performance multi-layer glass | .44 Magnum | 400 | No Penetration |
Applications and Uses of Bulletproof Glass
Bulletproof glass, also known as ballistic glass, finds applications across a wide spectrum of industries and situations where protection from projectiles is paramount. Its versatility and effectiveness are driven by its ability to withstand impact while maintaining transparency, making it a crucial component in various security systems and architectural designs. The specific type and thickness of bulletproof glass used varies significantly depending on the threat level and the application.
The diverse applications of bulletproof glass highlight its importance in modern security and design. Its use is constantly evolving, driven by advancements in materials science and a growing need for enhanced protection in increasingly unpredictable environments. The following sections detail some key areas where bulletproof glass plays a vital role.
Automotive Applications
The automotive industry utilizes bulletproof glass in high-security vehicles, ranging from armored limousines for VIPs to police vehicles designed for high-risk situations. The level of protection varies, with thicker, multi-layered glass offering greater resistance to high-caliber weaponry. These vehicles often incorporate additional security features, such as reinforced chassis and run-flat tires, to ensure comprehensive protection. For example, armored SUVs used by government officials and high-profile individuals often incorporate bulletproof glass as a standard safety feature.
Bulletproof glass is all about security, using multiple layers to stop projectiles. However, consider the energy efficiency aspects; you might also want to check out the benefits of using Low-E Glass (Low Emissivity Glass) , which can significantly reduce heat transfer. This makes it a worthwhile consideration when designing buildings that also need bulletproof protection, balancing safety and energy costs.
The design considerations include balancing protection with visibility and weight limitations.
Banking and Financial Institutions
Banks and other financial institutions widely employ bulletproof glass in teller windows and security booths to protect staff and assets from armed robberies. The level of protection required depends on the perceived risk, the location of the institution, and the types of threats prevalent in the area. In high-risk areas, thicker, more resistant glass may be employed, sometimes combined with reinforced walls and other security measures.
The design often prioritizes clear visibility to maintain customer interaction while providing adequate protection.
Security Applications
Beyond automotive and banking sectors, bulletproof glass finds extensive use in various security applications. This includes: security checkpoints at airports and government buildings; museum display cases protecting valuable artifacts; high-security prisons and detention centers; and private residences of high-net-worth individuals. The specific requirements for each application vary widely, impacting the type and thickness of glass selected.
For example, bulletproof glass used in a museum display case might prioritize clarity and minimal distortion, whereas that used in a prison might focus primarily on maximum impact resistance.
Architectural and Design Applications
Innovative uses of bulletproof glass extend into architectural and design contexts. Modern buildings increasingly integrate bulletproof glass into their facades and interiors, offering a balance between security and aesthetic appeal. This can range from high-rise buildings incorporating bulletproof glass in exterior walls to interior partitions in high-security offices. The use of laminated glass, often incorporating interlayers of polycarbonate, allows for a balance between strength and transparency, leading to visually appealing yet secure structures.
For instance, some high-profile museums utilize bulletproof glass walls to showcase exhibits while protecting them from damage or theft.
Applications of Bulletproof Glass: A Summary
The diverse applications of bulletproof glass are extensive and span numerous industries. Below is a summary categorized by industry or use case:
- Automotive: Armored vehicles, limousines, police cars.
- Banking and Finance: Teller windows, security booths, ATM enclosures.
- Security: Government buildings, airports, museums, prisons, private residences.
- Military and Defense: Armored vehicles, observation posts, protective barriers.
- Architectural and Design: Building facades, interior partitions, museum display cases.
Maintenance and Care of Bulletproof Glass
Bulletproof glass, while incredibly strong, requires careful maintenance to ensure its continued effectiveness and longevity. Neglecting proper care can compromise its ballistic properties, leading to reduced protection and potentially dangerous situations. Regular cleaning and careful handling are crucial for preserving the integrity of this specialized material.Proper Cleaning and Maintenance Procedures for Bulletproof GlassMaintaining bulletproof glass involves more than just a simple wipe-down.
The cleaning process must be gentle yet thorough to avoid scratching or damaging the delicate surface layers that contribute to its protective capabilities. Harsh chemicals or abrasive materials can significantly degrade the glass’s performance over time.
Cleaning Procedures
Clean bulletproof glass regularly using a soft, lint-free cloth and a mild, non-abrasive cleaning solution. Distilled water mixed with a small amount of isopropyl alcohol is a safe and effective option. Avoid using ammonia-based cleaners, as these can damage the protective coatings. Always clean the glass in a gentle, circular motion, avoiding harsh scrubbing. For stubborn stains, allow the cleaning solution to sit for a few minutes before wiping.
Thoroughly rinse the glass with clean water and dry it completely with a clean, soft cloth to prevent water spots.
Risks of Improper Cleaning or Handling
Improper cleaning or handling can lead to a variety of problems. Scratches on the surface, even microscopic ones, can weaken the glass and compromise its ability to stop projectiles. The use of abrasive cleaners or tools can also etch the surface, reducing its transparency and overall effectiveness. Furthermore, forceful impacts or dropping heavy objects on the glass can cause internal stress fractures, even if no visible damage is apparent.
These hidden flaws can significantly reduce the glass’s ballistic rating and create a safety hazard.
Damage Identification and Repair Strategies
Regular inspections are vital to identifying potential damage early on. Look for any scratches, chips, cracks, or discoloration. Small scratches might be manageable with specialized polishing compounds applied by professionals, but significant damage usually necessitates replacement. Internal damage, often invisible to the naked eye, is particularly dangerous. If there is any doubt about the integrity of the bulletproof glass, it’s crucial to have it professionally inspected and tested to determine the extent of the damage and whether repair or replacement is necessary.
Replacement should always be done by trained professionals using materials that meet the same ballistic standards as the original installation.
Best Practices for Maintaining Bulletproof Glass Integrity
Regular maintenance is key to prolonging the lifespan and effectiveness of bulletproof glass. Following these best practices can help ensure its continued protection:
- Clean the glass regularly using appropriate cleaning solutions and methods.
- Avoid using abrasive cleaners, harsh chemicals, or sharp objects on the glass surface.
- Inspect the glass regularly for any signs of damage, no matter how minor.
- Have any damage professionally assessed and repaired or replaced as needed.
- Protect the glass from potential impacts by installing appropriate barriers or protective coverings where necessary.
- Follow the manufacturer’s recommendations for cleaning and maintenance.
Future Trends and Innovations in Bulletproof Glass Technology
The field of bulletproof glass is constantly evolving, driven by the need for lighter, stronger, and more versatile protective materials. Advances in materials science, nanotechnology, and manufacturing techniques are paving the way for significant improvements in ballistic performance and overall functionality. This section explores emerging trends and potential future innovations that promise to revolutionize the use and application of bulletproof glass.
Lighter and Stronger Materials
The development of lighter yet stronger bulletproof glass is a key focus of ongoing research. Current multi-layered glass constructions, while effective, can be quite heavy, limiting their applications. Researchers are exploring new materials, such as advanced polymers and ceramics, which offer superior strength-to-weight ratios. For example, the incorporation of graphene, a single layer of carbon atoms, into the glass matrix could significantly enhance its strength and impact resistance while reducing overall weight.
Bulletproof glass is renowned for its ability to withstand high-impact forces, often used in security applications. Its strength is partially derived from its layered structure and specialized materials. A fascinating alternative material with similar properties is explored in this article on Sapphire Glass , highlighting its potential applications in high-end protective solutions. Understanding sapphire’s properties gives further insight into the science behind bulletproof glass technology.
This would expand the use of bulletproof glass in areas where weight is a critical factor, such as personal protective equipment and lightweight vehicles.
The Impact of Nanotechnology
Nanotechnology offers exciting possibilities for enhancing the properties of bulletproof glass. The manipulation of materials at the nanoscale allows for the creation of novel structures and composites with tailored properties. For instance, incorporating nanoparticles of materials like silicon carbide or zinc oxide into the glass matrix can increase its hardness, scratch resistance, and overall ballistic performance. Furthermore, nanotechnology could enable the development of self-healing bulletproof glass, which would automatically repair minor scratches and imperfections, extending its lifespan and maintaining its protective capabilities.
This technology could reduce maintenance costs and increase the overall longevity of the product.
Improved Ballistic Performance and Versatility
Research and development efforts are continuously focused on improving the ballistic performance and versatility of bulletproof glass. This includes exploring new layering techniques, optimizing the composition of existing materials, and developing new types of glass that can withstand higher-velocity projectiles. For example, research into the use of liquid crystals within the glass layers is showing promise in increasing the ability to absorb kinetic energy.
The development of flexible bulletproof glass, which could be incorporated into curved surfaces or even wearable technologies, is another area of active research. This would dramatically expand the range of applications for this crucial protective material.
Hypothetical Future Innovation: “Aerogel-Enhanced Laminate”
Imagine a new type of bulletproof glass, tentatively named “Aerogel-Enhanced Laminate” (AEL). This hypothetical innovation would feature a core layer of a transparent silica aerogel sandwiched between two layers of extremely tough, chemically strengthened glass. In an illustration, the AEL would appear as a slightly hazy, almost opalescent panel, subtly shimmering with an internal light diffusion caused by the aerogel’s porous structure.
The aerogel, known for its incredibly low density and high insulation properties, would contribute significantly to the AEL’s lightweight nature, while the chemically strengthened glass layers would provide exceptional impact resistance. This combination would result in a bulletproof glass that is significantly lighter and stronger than current alternatives, while maintaining a high degree of transparency. The potential applications are vast, ranging from use in personal protective equipment and architectural applications to advanced aerospace and military vehicles, where weight reduction is paramount.
The AEL’s inherent lightness and strength would revolutionize many industries dependent on ballistic protection.
Last Recap
Bulletproof glass stands as a testament to human ingenuity, a product born from the need for protection and advanced through continuous innovation. From its initial conception to its current sophisticated forms, it has consistently adapted to meet the evolving challenges of ballistic threats. Understanding its composition, performance, and maintenance is key to appreciating its crucial role in securing our world, and the future promises even more remarkable advancements in this critical area of safety and security.
FAQ Guide
How much does bulletproof glass cost?
The cost varies significantly depending on the thickness, size, level of protection required, and the manufacturer. Expect to pay a substantial premium compared to standard glass.
Can bulletproof glass be scratched?
Yes, although it’s highly resistant, bulletproof glass can be scratched. Proper cleaning and handling are crucial to maintain its integrity and appearance.
Is bulletproof glass transparent?
While designed for transparency, there can be some slight distortion or discoloration depending on the thickness and composition. Modern advancements are constantly improving transparency.
How is bulletproof glass repaired?
Minor scratches can sometimes be buffed out, but significant damage usually requires replacement. Repair attempts should only be undertaken by qualified professionals.
What are the ethical considerations surrounding bulletproof glass?
The use of bulletproof glass raises ethical questions, particularly concerning its role in escalating conflicts or creating a sense of increased security that might encourage riskier behaviors.