Borosilicate glass, renowned for its exceptional heat resistance and durability, is a fascinating material with a wide range of applications. From the precision instruments of scientific laboratories to the everyday convenience of oven-safe cookware, its unique properties have revolutionized numerous industries. This exploration delves into the composition, manufacturing, uses, and future potential of this remarkable substance, highlighting its advantages and disadvantages.
Understanding borosilicate glass involves exploring its distinct chemical makeup, which sets it apart from common soda-lime glass. This difference translates into superior thermal shock resistance, making it ideal for applications involving significant temperature fluctuations. We’ll examine the manufacturing processes, from melting to annealing, and explore the diverse ways borosilicate glass is used, from high-precision scientific equipment to everyday household items.
Chemical Composition and Properties of Borosilicate Glass
Borosilicate glass, prized for its exceptional properties, stands apart from other glass types due to its unique chemical makeup and resulting characteristics. Understanding its composition and how it differs from more common glasses like soda-lime glass is crucial to appreciating its diverse applications.
Borosilicate glass is primarily composed of silica (SiO 2), typically around 70-80%, boric oxide (B 2O 3) at 10-13%, and smaller amounts of other oxides such as sodium oxide (Na 2O), aluminum oxide (Al 2O 3), and potassium oxide (K 2O). The key difference compared to soda-lime glass, the most common type, lies in the significant addition of boric oxide.
Soda-lime glass relies heavily on sodium oxide and calcium oxide to lower the melting point, making it easier and cheaper to produce. This however, comes at the cost of reduced thermal resistance and chemical durability.
Borosilicate glass, known for its heat resistance, is a popular choice in various applications. Its durability makes it suitable for situations requiring high temperatures, and this characteristic is also relevant when considering specialized glass types like Solar Control Glass , which needs to withstand intense sunlight. Therefore, borosilicate glass’s properties often play a key role in the manufacturing of such advanced glass products.
Thermal Resistance and Durability
The inclusion of boric oxide significantly alters the glass’s atomic structure, resulting in superior thermal shock resistance. Boric oxide strengthens the silica network, reducing the thermal expansion coefficient. This means that borosilicate glass experiences less stress when subjected to rapid temperature changes, making it far less prone to cracking or shattering compared to soda-lime glass. This high durability extends beyond thermal shock; borosilicate glass is also more resistant to scratching and general wear and tear, contributing to its longevity.
Chemical Inertness
Borosilicate glass exhibits excellent chemical inertness, meaning it resists reactions with most chemicals. This makes it ideal for applications requiring contact with corrosive substances. Unlike soda-lime glass, which can leach ions into liquids, particularly under acidic or alkaline conditions, borosilicate glass maintains a high degree of chemical stability, preserving the purity of its contents. This characteristic is vital in laboratory glassware, pharmaceutical containers, and food preparation equipment.
Borosilicate glass is known for its impressive heat resistance, making it a popular choice for cookware and laboratory equipment. This superior heat tolerance is a key characteristic that overlaps with the properties of fire-resistant glass, like the kind discussed in this article on Fire-Resistant Glass. Ultimately, understanding the heat properties of borosilicate glass helps us appreciate its various applications, from everyday use to specialized scientific settings.
Comparison of Properties
The following table compares the properties of borosilicate glass with soda-lime glass and other common glass types. Note that values can vary slightly depending on the specific composition.
Borosilicate glass is known for its resistance to thermal shock, making it ideal for cookware and laboratory equipment. Unlike borosilicate, a common type of glass is annealed glass, which you can learn more about here: Annealed Glass. However, the superior heat resistance of borosilicate glass sets it apart from annealed glass in many applications.
Property | Borosilicate Glass | Soda-Lime Glass | Quartz Glass |
---|---|---|---|
Thermal Expansion Coefficient (×10-6/°C) | 3.3 | 9.0 | 0.5 |
Refractive Index (at 589 nm) | 1.47 | 1.52 | 1.46 |
Chemical Resistance | Excellent | Good (but susceptible to alkaline solutions) | Excellent |
Hardness (Mohs scale) | ~7 | ~6 | ~7 |
Density (g/cm3) | 2.23 | 2.4-2.5 | 2.2 |
Manufacturing Processes of Borosilicate Glass
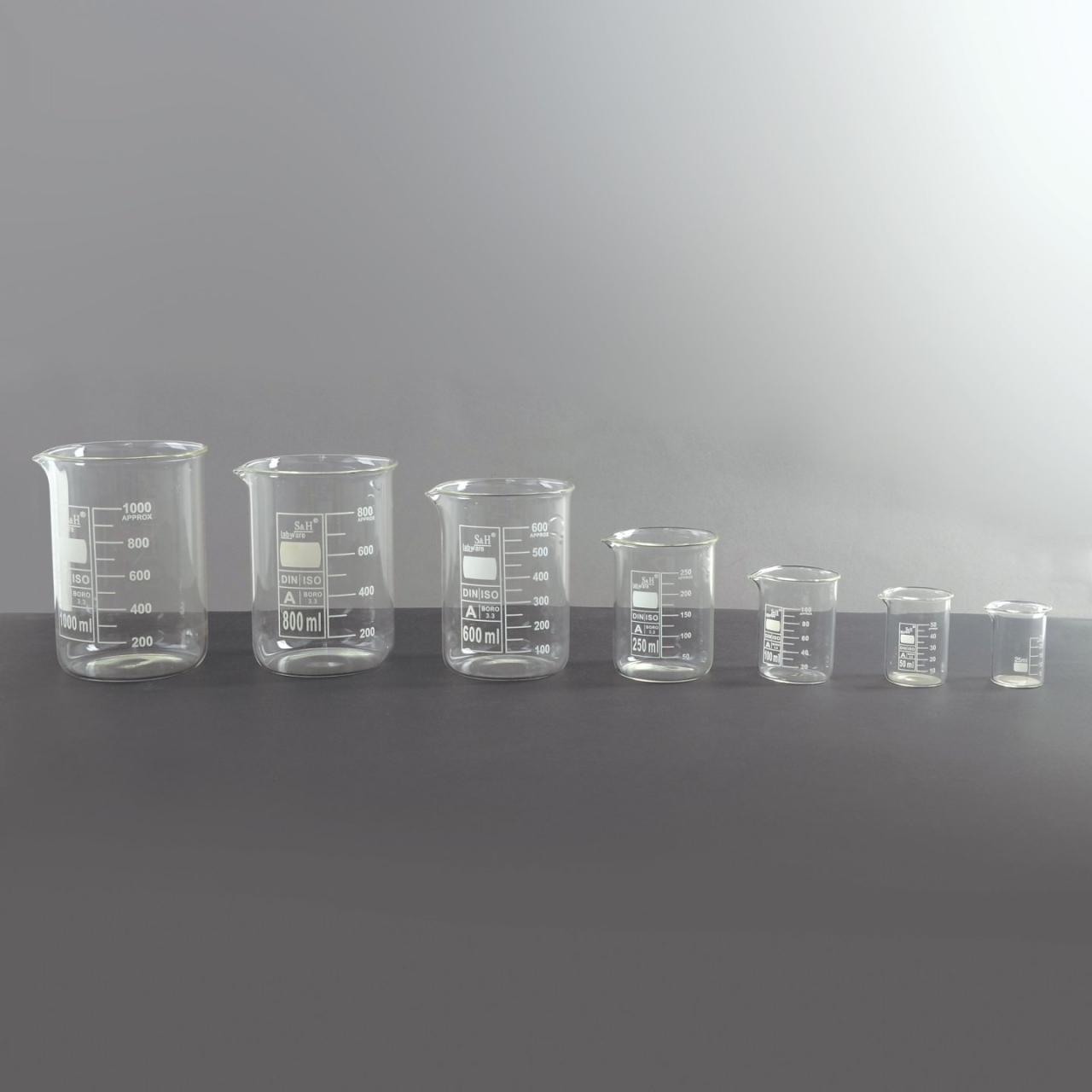
Source: com.tr
Borosilicate glass, prized for its low thermal expansion and chemical resistance, undergoes a sophisticated manufacturing process involving several key steps. These steps, from raw material melting to final annealing, are carefully controlled to ensure the final product meets stringent quality standards. The precise control of temperature is paramount throughout the entire process, impacting the glass’s final properties and its suitability for various applications.The manufacturing of borosilicate glass generally begins with the careful batching of raw materials.
These materials, primarily silica sand, boric oxide, soda ash, and alumina, are weighed and mixed in precise proportions to achieve the desired composition. The precise ratios determine the final properties of the glass, such as its thermal expansion coefficient and chemical durability.
Melting
The carefully mixed batch is then fed into a high-temperature furnace, typically a regenerative furnace or an electric melting furnace, where it is melted at temperatures exceeding 1500°C. This high temperature is necessary to break down the raw materials into a molten state, allowing the components to fully fuse and homogenize. The melting process typically takes several hours, allowing for complete fusion and the removal of any bubbles or impurities.
The temperature is carefully monitored and controlled throughout this phase to prevent devitrification (crystallization) and ensure a homogenous melt.
Shaping
Once melted, the molten glass is ready for shaping. Several methods exist, depending on the desired final product. For tubing, a continuous drawing process is often employed, where the molten glass is drawn upwards through a die, forming a continuous tube. For other forms like rods or sheets, different techniques such as pressing, blowing, or rolling are used.
These shaping techniques require precise control of temperature and pressure to achieve the desired dimensions and tolerances. For example, in the drawing process, the precise temperature of the molten glass and the rate of drawing directly influence the final dimensions and uniformity of the tubing.
Annealing
After shaping, the borosilicate glass undergoes annealing, a crucial heat treatment process to relieve internal stresses that may have developed during the shaping process. Annealing involves slowly cooling the glass to room temperature, allowing the internal structure to relax and reducing the risk of cracking or breakage. The annealing schedule, involving specific temperature ramps and holding times, is critical to achieving the desired final properties.
An improperly annealed glass may exhibit increased fragility and susceptibility to thermal shock.
Flowchart: Manufacturing of Borosilicate Glass Tubing
A flowchart illustrating the process would depict the following steps:
1. Raw Material Batching
Silica sand, boric oxide, soda ash, alumina are weighed and mixed.
2. Melting
The batch is melted in a high-temperature furnace (1500°C+).
3. Homogenization
The molten glass is stirred to ensure uniformity.
4. Shaping (Drawing)
Molten glass is drawn through a die to form a continuous tube.
5. Annealing
The tubing is slowly cooled to room temperature to relieve internal stresses.
6. Inspection
Quality control checks are performed.
7. Cutting and Finishing
The tubing is cut to desired lengths and any further finishing is done.
Applications of Borosilicate Glass
Borosilicate glass, with its superior heat resistance and chemical durability, finds applications across a wide spectrum of industries. Its unique properties make it ideal for situations demanding high temperatures, aggressive chemicals, and precise measurements. From scientific research to everyday kitchenware, the versatility of borosilicate glass is truly remarkable.
The diverse applications of borosilicate glass stem from its inherent properties. Its low thermal expansion coefficient minimizes breakage from thermal shock, while its high chemical resistance ensures its integrity even when exposed to harsh chemicals. This combination of properties allows for its use in a vast array of products and processes, making it a crucial material in various sectors.
Laboratory and Scientific Applications
Borosilicate glass is a cornerstone of scientific research and experimentation. Its resistance to thermal shock and chemical attack makes it perfect for applications requiring precise measurements and repeated heating and cooling cycles.
- Beaker: A cylindrical container with a flat bottom and a lip for pouring, used for mixing, heating, and measuring liquids in laboratory settings. Its durability ensures it can withstand repeated heating and cleaning.
- Flask: A container with a round body and a narrow neck, used for holding and mixing liquids. Erlenmeyer flasks, in particular, are often made from borosilicate glass due to their need to withstand heating and swirling.
- Test Tubes: Small, cylindrical tubes used for holding and testing small samples of liquids or solids. The chemical inertness of borosilicate glass prevents contamination of samples.
Culinary Applications
The heat resistance of borosilicate glass makes it a popular choice for cookware and bakeware. Its ability to withstand high temperatures without shattering or cracking makes it suitable for oven-to-table use.
- Oven-to-Table Dishes: These dishes can transition seamlessly from the oven to the dining table, eliminating the need for transferring food. The material’s durability and resistance to staining make cleanup easy.
- Pyrex Cookware: A well-known brand of borosilicate glass cookware, often used for baking, cooking, and storing food. Its ability to withstand rapid temperature changes makes it suitable for various cooking methods.
- Measuring Cups and Jugs: Precise measurements are crucial in baking and cooking, and borosilicate glass measuring tools provide accurate readings while withstanding the heat of ovens and dishwashers.
Lighting Applications
Borosilicate glass is also used extensively in lighting applications, particularly in high-intensity discharge lamps. Its ability to withstand high temperatures and its transparency make it ideal for transmitting light effectively.
- High-Intensity Discharge (HID) Lamps: These lamps, including metal halide and high-pressure sodium lamps, generate significant heat. Borosilicate glass envelopes protect the lamp components and contain the high-pressure gases.
- Specialty Lighting Fixtures: Borosilicate glass is used in various specialty lighting applications where high temperatures or chemical resistance are required, such as in industrial settings or scientific instruments.
Advantages and Disadvantages of Using Borosilicate Glass
Borosilicate glass, with its unique combination of properties, offers significant advantages in various applications. However, like any material, it also presents certain limitations. Understanding both the strengths and weaknesses is crucial for making informed decisions about its suitability for a given project. This section will explore these aspects, comparing its cost-effectiveness with other glass types.
Advantages of Borosilicate Glass
The superior performance of borosilicate glass stems from its low thermal expansion coefficient, high chemical resistance, and excellent durability. These properties make it ideal for applications requiring resistance to thermal shock, chemical attack, and mechanical stress. For instance, its resistance to thermal shock allows it to withstand rapid temperature changes without cracking, a feature highly valued in laboratory glassware and cookware.
Its chemical inertness prevents leaching of unwanted substances into its contents, crucial for scientific experiments and food preparation. The high durability ensures longevity, reducing replacement costs in the long run.
Disadvantages of Borosilicate Glass
While offering many advantages, borosilicate glass also has some drawbacks. Its higher manufacturing cost compared to soda-lime glass is a significant factor. Furthermore, its relatively higher hardness makes it more challenging to cut and shape than other glass types, increasing processing time and costs. Although strong, borosilicate glass can still break under sufficient stress or impact. Finally, its lower refractive index compared to some specialized glasses might limit its use in optical applications requiring higher refractive power.
Cost-Effectiveness Compared to Other Glass Types
The cost-effectiveness of borosilicate glass is application-dependent. While its initial cost is higher than soda-lime glass, its superior durability and resistance to breakage often translate to lower long-term costs, particularly in high-stress applications. For example, in laboratory settings, the reduced frequency of replacement due to breakage offsets the higher initial investment. Conversely, in applications where high thermal shock resistance is not critical, the cost of borosilicate glass might outweigh its benefits.
In the case of specialty optical applications, the trade-off between its lower refractive index and potentially higher cost compared to other glasses needs careful consideration.
Advantages | Disadvantages |
---|---|
High resistance to thermal shock | Higher manufacturing cost than soda-lime glass |
Excellent chemical durability and inertness | More difficult to cut and shape than other glass types |
High strength and durability | Can still break under sufficient stress or impact |
Suitable for high-temperature applications | Lower refractive index compared to some specialized glasses |
Long lifespan, reducing replacement costs | May not be cost-effective for all applications |
Recycling and Environmental Impact of Borosilicate Glass
Borosilicate glass, prized for its durability and heat resistance, presents a unique set of considerations when it comes to recycling and its overall environmental impact. Unlike some other materials, its recycling process isn’t always straightforward, but its inherent properties offer opportunities for sustainable practices. Understanding both the challenges and the potential benefits is crucial for responsible manufacturing and consumption.Borosilicate glass is chemically durable and can be recycled multiple times without significant degradation of its properties.
However, its recycling rate is significantly lower than that of soda-lime glass (the type commonly used for bottles and jars) due to several factors. The main issue is the need for separation from other types of glass during the recycling process. Contamination with other materials can compromise the quality of the recycled borosilicate glass, rendering it unsuitable for certain applications.
Recyclability of Borosilicate Glass
Borosilicate glass is inherently recyclable, meaning it can be melted down and reused to create new products. The process is similar to that of other glass types, involving crushing, cleaning, and remelting. However, the higher melting point of borosilicate glass requires more energy compared to soda-lime glass. This higher energy demand needs to be considered in the overall environmental impact assessment.
Furthermore, the lack of widespread collection and sorting systems specifically designed for borosilicate glass often leads to it ending up in landfills, despite its recyclability. Successful recycling depends on effective separation from other glass types and non-glass materials. Companies specializing in glass recycling are increasingly developing better techniques to efficiently sort borosilicate glass from other materials.
Environmental Impact Compared to Other Materials
Compared to materials like plastics or metals, borosilicate glass boasts several environmental advantages. It’s inert, meaning it doesn’t leach harmful chemicals into the environment. It’s also infinitely recyclable, unlike many plastics that degrade in quality with each recycling cycle. However, the energy required for its production and recycling remains a key factor in its overall environmental footprint.
The manufacturing process, involving high temperatures, consumes significant energy. Life cycle assessments (LCAs) comparing borosilicate glass to alternatives, like plastic or stainless steel, often highlight a trade-off between energy consumption and the avoidance of environmentally harmful substances. For example, while borosilicate glass might require more energy in production, its inert nature and recyclability can outweigh the energy costs over its longer lifespan compared to disposable plastics.
Challenges in Recycling Borosilicate Glass
The primary challenge lies in the separation and sorting process. Borosilicate glass is often mixed with other types of glass during collection, making separation difficult and potentially leading to contamination. This contamination reduces the quality of the recycled material. Another challenge is the lack of dedicated recycling streams for borosilicate glass. Many municipal recycling programs aren’t equipped to handle this specific type of glass, resulting in it being landfilled.
The higher melting point also necessitates higher energy consumption during the recycling process compared to other types of glass.
Opportunities in Recycling Borosilicate Glass
The development of advanced sorting technologies can significantly improve the efficiency of borosilicate glass recycling. Sensor-based sorting systems can identify and separate borosilicate glass from other materials with greater accuracy. Increased public awareness and education about the importance of separating borosilicate glass from other waste streams are also crucial. Collaboration between manufacturers, recyclers, and consumers can establish dedicated collection points and recycling pathways for borosilicate glass, increasing its recycling rate.
Furthermore, innovative recycling techniques, such as the use of microwave heating for more efficient melting, could reduce the energy consumption associated with the process.
Sustainable Manufacturing Practices
The borosilicate glass industry can significantly reduce its environmental impact through sustainable manufacturing practices. This includes adopting energy-efficient furnaces and processes, exploring the use of renewable energy sources for manufacturing, and optimizing the production process to minimize waste. Utilizing recycled cullet (broken glass) as a raw material in the manufacturing process reduces the need for virgin materials and energy consumption.
Companies can also invest in closed-loop systems, where waste materials are recycled and reused within the manufacturing process. Implementing stringent quality control measures throughout the production chain can minimize the generation of defective products that might end up in landfills. These steps contribute to a circular economy model for borosilicate glass, minimizing its environmental footprint.
Future Trends and Innovations in Borosilicate Glass Technology
Borosilicate glass, already a versatile material with a wide range of applications, is poised for significant advancements driven by evolving technological needs and innovative manufacturing processes. Ongoing research and development are pushing the boundaries of its capabilities, leading to new applications and improved performance characteristics. These advancements are not only enhancing existing uses but also opening doors to entirely new possibilities in diverse fields.The future of borosilicate glass technology is marked by a convergence of several key trends, focusing on improved properties, enhanced manufacturing techniques, and exploration of novel applications.
Enhanced Durability and Strength
Significant efforts are being directed towards increasing the mechanical strength and durability of borosilicate glass. This involves exploring novel compositions, incorporating reinforcing agents, and refining manufacturing processes to minimize internal flaws that can compromise structural integrity. For example, the development of nano-structured borosilicate glasses is showing promise in achieving higher strength-to-weight ratios compared to traditional formulations. These advancements are particularly crucial for applications in demanding environments, such as aerospace and high-temperature industrial processes.
Borosilicate glass, known for its heat resistance, is a popular choice in various applications. Its durability makes it a great base material for some advanced technologies, including those used in Smart Glass / Switchable Glass , where its strength helps maintain the integrity of the electrochromic layers. Ultimately, the properties of borosilicate glass contribute significantly to the performance and longevity of these innovative smart glass products.
Research into self-healing borosilicate glass is also underway, aiming to create materials that can automatically repair minor cracks or damage, extending their lifespan and reducing maintenance costs. This would be a significant leap forward, especially in applications where replacement is difficult or costly.
Advanced Manufacturing Techniques
The adoption of advanced manufacturing techniques is revolutionizing the production of borosilicate glass components. Additive manufacturing, also known as 3D printing, is gaining traction, allowing for the creation of complex and customized shapes with high precision. This technology enables the fabrication of intricate designs that would be impossible or prohibitively expensive to produce using traditional methods. Furthermore, advancements in glass molding and forming techniques are leading to improved dimensional accuracy and surface finish, resulting in higher-quality products.
This is particularly important for applications requiring high precision, such as optical components and microfluidic devices. For example, the use of high-precision robotic arms and advanced control systems is improving the consistency and speed of manufacturing processes.
Expansion into New Applications
The unique properties of borosilicate glass make it an ideal candidate for a growing number of applications. Its biocompatibility is leading to its increased use in medical devices and implants. Its excellent chemical resistance is fueling its adoption in advanced chemical processing equipment. Furthermore, its transparency and low thermal expansion make it suitable for use in high-power laser systems and solar energy applications.
The development of flexible borosilicate glass opens up new possibilities in wearable technology and flexible displays. Imagine a phone screen that is incredibly resistant to shattering, or a medical implant that seamlessly integrates with the body. These are the kinds of innovations becoming possible thanks to ongoing research. Additionally, research into borosilicate glass composites, combining glass with other materials like polymers or ceramics, is expanding its applications even further.
These composites can combine the best properties of each material, leading to innovative products with enhanced performance characteristics.
Illustrative Examples of Borosilicate Glass Applications
Borosilicate glass finds its niche in a wide array of applications, leveraging its unique properties of high heat resistance, chemical inertness, and durability. The following examples highlight its versatility across diverse sectors.
High-Temperature Application: Pyrex Baking Dishes
Borosilicate glass, famously used in Pyrex bakeware, excels in high-temperature applications due to its low thermal expansion coefficient. This means it resists cracking or shattering when subjected to rapid temperature changes, unlike many other types of glass. A typical Pyrex baking dish, for example, is transparent, allowing for easy monitoring of food during baking. Its smooth, non-porous surface prevents food from sticking, making cleaning simple.
The dish’s resistance to thermal shock ensures it can transition seamlessly from a hot oven to a cold countertop without damage, providing a reliable and safe cooking vessel. Its durability contributes to its long lifespan, making it a cost-effective choice for frequent baking.
Chemical Laboratory Setting: Beakers and Flasks
In chemical laboratories, borosilicate glass is the material of choice for beakers, flasks, and other glassware due to its exceptional chemical resistance. Its inert nature prevents it from reacting with most chemicals, ensuring accurate and reliable experimental results. A typical borosilicate glass beaker, for instance, will maintain its structural integrity and transparency even after repeated exposure to strong acids, bases, and solvents.
This resistance to chemical attack minimizes contamination risks and extends the lifespan of the glassware, making it a crucial element in maintaining the accuracy and reliability of laboratory experiments. The clarity of the glass also facilitates easy observation of reactions and measurements.
Everyday Life: Drinking Glasses
Many everyday drinking glasses are made from borosilicate glass, often chosen for its combination of durability and clarity. These glasses typically exhibit a smooth, transparent surface, showcasing the contents within. Their lightweight yet sturdy construction makes them comfortable to hold and resistant to accidental breakage from normal use. While not as heat-resistant as specialized laboratory or ovenware, their durability makes them suitable for everyday use and capable of withstanding the rigors of frequent washing and handling.
The clarity and simple design of these glasses allow them to blend seamlessly into various table settings.
Conclusion
Borosilicate glass stands as a testament to the power of material science, offering a unique blend of strength, durability, and heat resistance. Its versatility shines through in its diverse applications, from scientific research to culinary creations and beyond. As technology advances, we can anticipate even more innovative uses for this remarkable material, pushing the boundaries of its potential and further solidifying its place in our modern world.
FAQ Summary
Is borosilicate glass safe for the microwave?
Generally, yes, but always check the manufacturer’s instructions as some designs may have metal components unsuitable for microwaves.
Can borosilicate glass be recycled?
Yes, but recycling programs may not always accept it separately from other glass types. Check with your local recycling center.
How does borosilicate glass compare to Pyrex?
Pyrex is a brand name often associated with borosilicate glass; many Pyrex products are made from it, but not all borosilicate glass is Pyrex.
Is borosilicate glass more expensive than other types of glass?
Typically, yes, due to the specialized manufacturing process and superior properties.
How is the strength of borosilicate glass affected by repeated heating and cooling?
While highly resistant, repeated and extreme temperature changes can weaken it over time. Sudden temperature shocks are more damaging than gradual ones.