Pros and cons of using metal panels for luxury home exteriors are a key consideration for discerning homeowners. Metal siding offers a unique blend of modern aesthetics, exceptional durability, and potential environmental benefits, but it also comes with specific cost and maintenance implications. This exploration delves into the advantages and disadvantages, helping you determine if metal panels are the right choice for your dream home’s exterior.
From the sleek, contemporary appeal of aluminum to the rustic charm of copper, metal panels offer a diverse range of design options. Their longevity and resilience against harsh weather conditions make them a compelling alternative to traditional materials like wood or vinyl. However, the initial investment can be significant, and understanding the nuances of installation and long-term maintenance is crucial for making an informed decision.
This guide will navigate these complexities, providing a comprehensive overview to help you weigh the pros and cons effectively.
Aesthetics and Design
Metal paneling offers a surprisingly diverse range of aesthetic options for luxury homes, moving beyond the industrial connotations often associated with metal. The material’s inherent versatility allows for a seamless integration into various architectural styles and design preferences, creating stunning and durable exteriors. Careful consideration of metal type, finish, and design details is key to achieving the desired aesthetic.
The choice of metal significantly impacts the visual character of the home’s exterior. Different metals offer unique textural and color variations, influencing the overall feel and tone of the design.
Metal Types and Visual Characteristics
The visual appeal of metal siding greatly depends on the chosen material. Each metal offers a distinct aesthetic, contributing to the home’s overall style and curb appeal. The following table compares the visual characteristics of some popular options.
Metal Type | Visual Characteristics | Color Variations | Maintenance |
---|---|---|---|
Copper | Warm, reddish-brown tones that naturally patina over time, developing a unique and beautiful verdigris finish. | Ranges from bright reddish-orange to deep, dark brown-green. | Minimal, though patina requires no intervention. |
Zinc | Initially silvery-grey, developing a subtle, bluish-grey patina over time. The patina is less dramatic than copper’s. | Primarily shades of grey and blue-grey. | Low maintenance; the patina is protective. |
Aluminum | Highly versatile, available in a wide array of colors and finishes. Can mimic the appearance of other materials. | Unlimited; powder coating allows for virtually any color. | Very low maintenance; resistant to corrosion. |
Metal Panel Designs and Architectural Styles
Metal panels are remarkably adaptable and can enhance various architectural styles. The design of the panels themselves – from the size and shape to the pattern – plays a crucial role in determining the final aesthetic.
Metal panels offer a sleek, modern look for luxury homes, but their cost and potential maintenance issues are drawbacks. Choosing the right exterior material significantly impacts the overall aesthetic, and this extends to the interior; for ideas on coordinating materials, check out this article on best materials for high-end residential interior design. Ultimately, the pros and cons of metal panels need careful consideration alongside your interior design choices to achieve a cohesive, high-end look.
Modern homes often utilize sleek, linear metal panels in neutral colors to create a clean, minimalist look. Traditional homes might incorporate metal panels with more intricate detailing or a weathered finish to complement existing architectural features. Farmhouse styles can benefit from the use of corrugated metal panels or those with a rustic, aged appearance, contributing to a sense of warmth and character.
The versatility of metal allows for a wide range of creative possibilities. For example, a modern home might use large, flat panels in a brushed aluminum finish, while a traditional home might use smaller, textured panels in a dark bronze finish.
Finishes and Their Impact on the Overall Look
The finish applied to the metal panels dramatically alters their visual impact. Different finishes create diverse textures and reflect light in unique ways, influencing the overall appearance of the home.
A brushed finish provides a subtle, textured appearance with a matte or semi-gloss sheen, lending a sophisticated and contemporary feel. A polished finish offers a high-gloss, reflective surface that creates a sleek and modern look. Textured finishes, such as those mimicking wood grain or stone, add depth and visual interest, allowing for a more organic or rustic aesthetic.
Metal panels offer a sleek, modern look for luxury homes, boasting durability and low maintenance. However, they can be pricey and might not suit all architectural styles. Choosing the right materials is key, especially for smaller spaces, and you can learn more about that process by checking out this helpful guide on how to choose the right luxury materials for small spaces.
Ultimately, weighing the pros and cons of metal panels – like their potential for heat absorption – is crucial for a successful luxury home exterior.
The choice of finish significantly impacts the perception of light and shadow, adding to the overall design effect. A polished finish, for example, will reflect more light, creating a brighter, more modern feel, while a matte finish will absorb more light, giving a more subdued and traditional feel.
Durability and Longevity
Metal panels offer a compelling alternative to traditional exterior materials for luxury homes, boasting exceptional durability and longevity. Their lifespan significantly impacts the long-term cost-effectiveness and aesthetic appeal of a property, making a thorough understanding of their performance crucial for discerning homeowners. This section compares the durability and longevity of metal panels to other popular options and details their performance in various weather conditions.
Lifespan Comparison of Exterior Materials
The lifespan of a building’s exterior is a key factor influencing maintenance costs and overall property value. Metal panels, when properly installed and maintained, generally outlast many other common materials. This advantage translates to lower long-term replacement costs and less frequent disruptions to the home’s aesthetic integrity.
- Metal Panels: With proper care, metal panels can last 50 years or more, sometimes even exceeding a century depending on the specific metal and coating used. Examples include the iconic metal siding on many industrial buildings that have stood for decades, demonstrating their resilience.
- Wood Siding: Wood, while aesthetically pleasing, requires significant maintenance and is susceptible to rot, insect infestation, and weathering. Its lifespan is considerably shorter, typically ranging from 15 to 30 years, depending on the wood type and climate.
- Vinyl Siding: Vinyl siding is relatively low-maintenance and offers a longer lifespan than wood, generally lasting 20 to 40 years. However, it’s prone to fading, cracking, and damage from impact, potentially requiring earlier replacement than metal.
- Brick: Brick is a durable material with a long lifespan, often lasting 50 years or more. However, it can be susceptible to damage from freeze-thaw cycles in colder climates and requires occasional repairs to maintain its integrity. Moreover, the initial cost is significantly higher than metal.
Weather Resistance of Metal Panels
Metal panels exhibit exceptional resistance to a wide range of weather conditions, contributing significantly to their longevity. Their inherent properties make them a superior choice for many climates.Metal panels are highly resistant to extreme temperatures, expanding and contracting minimally compared to other materials. This minimizes the risk of cracking or warping, even in regions with significant temperature fluctuations. They are also impervious to moisture, resisting damage from rain, snow, and humidity.
Properly coated metal panels effectively resist corrosion and rust, ensuring long-term protection. The design of the panels, with overlapping seams and proper sealing, further prevents water penetration.
Maintenance Requirements of Metal Panels
The maintenance requirements of metal panels are considerably lower compared to many other exterior materials. This translates to significant cost savings over the building’s lifespan and less disruption to the homeowner.
Metal panels offer a sleek, modern look for luxury homes, but their high cost and potential maintenance needs are drawbacks. However, the overall aesthetic can be tied into the interior design choices, complementing, for example, the luxurious materials favored by top designers as highlighted in this article on top designers’ choices for luxury interior materials. Ultimately, the decision hinges on balancing the striking exterior with long-term practicality and budget.
- Metal Panels: Regular cleaning with water and a mild detergent is usually sufficient. Occasional inspections for any signs of damage or corrosion are recommended. Repairs, if needed, are often straightforward and relatively inexpensive.
- Wood Siding: Wood siding requires regular painting or staining to protect it from the elements and prevent rot. It also needs periodic inspections for insect infestation and repairs to damaged areas.
- Vinyl Siding: Vinyl siding generally requires minimal maintenance, but occasional cleaning may be necessary to remove dirt and debris. However, repairs to damaged sections can be costly.
- Brick: Brick requires minimal maintenance, but occasional cleaning and repairs to damaged mortar may be necessary.
Cost and Installation: Pros And Cons Of Using Metal Panels For Luxury Home Exteriors
Metal panel siding offers a premium look, but its cost is a significant factor to consider when planning a luxury home exterior. Understanding the various cost components and comparing them to other cladding options is crucial for making an informed decision. This section will break down the costs and installation processes involved.
The initial investment for metal panel siding is higher than many alternatives, but its longevity often makes it a worthwhile long-term investment. The total cost depends on several interconnected factors, and accurate budgeting requires careful consideration of all aspects.
Cost Breakdown of Metal Panel Installation
The overall cost of installing metal panels on a luxury home’s exterior can vary widely. Several factors contribute to this variability, and a detailed breakdown is essential for realistic budgeting. The following table provides a general overview of the cost components.
Cost Component | Cost Per Square Foot (Estimate) | Factors Influencing Cost | Example |
---|---|---|---|
Material Costs (Panels, Flashing, Fasteners) | $5 – $20 | Panel type (aluminum, steel, zinc), finish (painted, coated), gauge (thickness), and supplier. | Higher-end zinc panels with a custom finish will cost significantly more than standard painted aluminum panels. |
Labor Costs (Installation, Preparation) | $8 – $20 | Complexity of the design (e.g., intricate detailing, multiple angles), size of the house, and labor rates in the region. | A house with many dormers and complex angles will require more labor than a simple rectangular structure. |
Additional Expenses (Permits, Waste Removal, Underlayment) | $2 – $5 | Local building codes and regulations, amount of waste generated, and the need for additional materials like moisture barriers. | Permitting fees vary widely by location, and waste removal costs depend on the project’s scale. |
Total Estimated Cost Per Square Foot | $15 – $45+ | This is a broad estimate; actual costs can vary significantly based on the factors listed above. | A large, complex home with high-end materials could easily exceed the upper end of this range. |
Comparison of Installation Processes, Pros and cons of using metal panels for luxury home exteriors
The installation process for metal panels differs from other common exterior cladding options. Understanding these differences is key to appreciating the time and skill involved in each method.
Here’s a comparison of the installation steps for metal panels, vinyl siding, and brick veneer:
- Metal Panels:
- Careful measurement and planning.
- Installation of sheathing and weather barriers.
- Precise cutting and fitting of panels.
- Secure fastening of panels using specialized tools.
- Installation of trim and flashing to ensure watertightness.
- Vinyl Siding:
- Installation of sheathing.
- Application of starter strips.
- Overlapping installation of vinyl panels.
- Cutting and fitting panels around windows and doors.
- Installation of J-channels and trim.
- Brick Veneer:
- Construction of a supporting framework.
- Installation of a moisture barrier.
- Laying bricks using mortar.
- Grouting and cleaning of the brickwork.
- Installation of flashing and trim.
Factors Influencing Overall Cost
Several factors significantly influence the final cost of a metal panel exterior. These factors should be carefully considered during the planning and budgeting phases.
- Panel Type: Aluminum is generally the most affordable, followed by steel, with zinc and copper being the most expensive options. Different finishes and coatings also affect cost.
- House Size: Larger homes naturally require more materials and labor, leading to higher overall costs.
- Design Complexity: Intricate designs with many angles, curves, and details increase both material and labor costs. Custom fabrication of panels may be required, adding to the expense.
- Labor Rates: Regional variations in labor costs significantly affect the overall project cost. Specialized skills may command higher rates.
- Hidden Costs: Unexpected issues, such as rotted sheathing or unforeseen structural problems, can add to the final cost. Proper inspections before installation are essential.
Environmental Impact
Metal panels, while offering many advantages for luxury home exteriors, have an environmental footprint that needs careful consideration. Their production, use, and eventual disposal all contribute to the overall impact on the planet, making it crucial to understand the lifecycle implications of choosing this material. This section will explore the environmental aspects of metal panel use, comparing them to other common exterior materials and highlighting sustainability features where applicable.The environmental impact of metal panels stems primarily from the energy required for mining raw materials, manufacturing processes, and transportation.
The energy intensity varies significantly depending on the specific metal used (aluminum, steel, copper, zinc) and the manufacturing techniques employed. For instance, aluminum production is energy-intensive, relying heavily on electricity. Steel production, while also energy-intensive, can utilize recycled materials, significantly reducing its carbon footprint. Transportation distances also play a role, with locally sourced materials having a smaller impact than those shipped internationally.
End-of-life disposal and recycling options also significantly affect the overall environmental impact.
Manufacturing and Recycling Processes
Manufacturing metal panels involves several stages, each with its own environmental consequences. Mining the raw materials (e.g., bauxite for aluminum, iron ore for steel) can lead to habitat disruption and water pollution. The smelting and refining processes are energy-intensive and often release greenhouse gases. The subsequent fabrication of the panels into their final form also consumes energy.
However, the recyclability of most metals is a significant advantage. Aluminum, for example, is highly recyclable with minimal loss of material properties, making it a relatively sustainable option when recycling infrastructure is in place. Steel is also readily recyclable, though the recycling process itself still requires energy. The extent to which these metals are actually recycled greatly impacts their overall environmental profile; high recycling rates significantly reduce the need for new material extraction and production.
Comparison with Other Exterior Materials
Comparing metal panels to other common exterior materials like wood, brick, or vinyl reveals a complex picture. Wood, while a renewable resource, often requires significant energy for processing and transportation, especially if sourced from distant locations. Deforestation is also a major environmental concern. Brick production is energy-intensive, involving high-temperature firing, and often requires the extraction of clay, potentially leading to land degradation.
Vinyl siding, a petroleum-based product, has a significant carbon footprint during manufacturing and is not readily biodegradable. While a comprehensive life-cycle assessment (LCA) is needed for a precise comparison, studies suggest that the overall environmental impact of metal panels can be comparable to or even better than some alternatives, particularly when considering the high recyclability of many metal types.
Sustainable Metal Panel Features
Several features can contribute to the sustainability of metal panels. The use of recycled content in the manufacturing process is crucial. Many manufacturers now offer panels with a high percentage of recycled aluminum or steel, significantly reducing the environmental impact compared to panels made from virgin materials. Furthermore, choosing locally sourced panels minimizes transportation emissions. The longevity and durability of metal panels also contribute to sustainability by reducing the need for frequent replacements, which would otherwise increase the overall environmental impact over the building’s lifespan.
For example, a building using long-lasting metal panels would avoid the repeated energy consumption associated with replacing, say, a wood or vinyl siding every 15-20 years. Finally, choosing panels with high reflectivity can reduce the building’s cooling load, lowering energy consumption for air conditioning.
Maintenance and Repair
Metal panel exteriors, while incredibly durable, still require regular maintenance to preserve their beauty and longevity. Neglecting upkeep can lead to costly repairs down the line, so a proactive approach is key. This section details a preventative maintenance schedule and Artikels common repair procedures for various issues.Proper maintenance significantly extends the lifespan of your metal panel siding and minimizes the need for extensive repairs.
Metal panels offer a sleek, modern look for luxury homes, boasting durability and low maintenance. However, the initial cost can be high, and the potential for noise transmission is a concern. To complement this exterior choice, consider the current trends in interior design, as detailed in this article on modern luxury interior design material trends 2024 , to create a cohesive and stylish home.
Choosing interior materials that echo the metal’s modern aesthetic will complete the luxurious feel.
Regular cleaning and inspections help identify and address small problems before they escalate into larger, more expensive issues. This preventative approach saves both money and time in the long run.
Preventative Maintenance Schedule
A simple, consistent maintenance schedule can greatly extend the life of your metal panels. The frequency of some tasks may depend on your climate and environmental conditions (e.g., proximity to the coast or industrial areas).
- Annual Inspection: Conduct a thorough visual inspection of all panels, looking for signs of damage, corrosion, or loose fasteners. Pay close attention to seams, corners, and areas prone to water accumulation.
- Semi-Annual Cleaning: Clean the panels at least twice a year using a soft-bristled brush, mild detergent, and water. Avoid abrasive cleaners or high-pressure washing, which can damage the panel’s finish.
- Seasonal Gutter Cleaning: Clear gutters and downspouts of debris to prevent water damage to the siding. Clogged gutters can cause water to pool against the panels, leading to corrosion.
- Fastener Check (Every 3-5 years): Inspect all fasteners for looseness or corrosion. Tighten loose screws or replace damaged ones. Consider using stainless steel fasteners to prevent corrosion.
- Caulk Inspection and Repair (As Needed): Regularly inspect caulking around windows, doors, and other penetrations in the siding. Replace any cracked or missing caulking to prevent water intrusion.
Common Issues and Repair Processes
Several issues can affect metal panels over time, but many are easily addressed with proper maintenance and timely repairs. Early detection is crucial to prevent minor problems from becoming major headaches.
- Dents: Minor dents can often be removed using a specialized dent puller or by carefully applying pressure from behind the panel (if accessible). For significant dents, panel replacement may be necessary.
- Scratches: Superficial scratches can often be touched up with a matching paint or sealant. Deeper scratches may require more extensive repair or replacement.
- Corrosion: Corrosion typically begins as small spots of rust. These should be addressed promptly by cleaning the affected area, applying a rust converter, and then painting with a rust-resistant primer and topcoat. Severe corrosion may require panel replacement.
- Loose or Damaged Fasteners: Loose fasteners should be tightened. Damaged or corroded fasteners should be replaced with new stainless steel fasteners. This prevents water penetration and maintains structural integrity.
- Paint Chipping or Peeling: This is often caused by impact or weathering. The chipped or peeled paint should be removed, the area primed, and then repainted with a high-quality exterior paint designed for metal surfaces. Consider using a specialized paint formulated for the specific metal type.
Addressing Specific Issues: Examples
Let’s illustrate how to address some common problems. Imagine a small dent on a painted aluminum panel. A suction cup dent puller could effectively remove the dent, leaving minimal trace. For a large scratch exposing bare metal on a galvanized steel panel, applying a rust converter, followed by a high-quality primer and a topcoat in a color matching the existing siding would be necessary to prevent rust and maintain the aesthetic appeal.
If a section of aluminum siding shows significant corrosion, replacement of that panel would be the most effective solution to prevent further damage.
Insulation and Energy Efficiency
Metal panels, while aesthetically pleasing and durable, also play a significant role in a home’s energy performance. Their ability to contribute to better insulation and improved energy efficiency depends on several factors, including the type of metal used, the panel’s design, and the overall building envelope. Understanding these factors is crucial for maximizing the energy-saving potential of a metal-clad luxury home.Metal panels themselves are not inherently great insulators; they conduct heat readily.
However, their contribution to energy efficiency comes from their role in creating an effective building envelope when used correctly. The key lies in integrating them with proper insulation systems.
Metal Panel Types and Thermal Performance
Different metals possess varying thermal conductivities. Aluminum, for instance, has a higher thermal conductivity than steel. This means aluminum panels will transfer heat more readily than steel panels. However, the impact on overall energy efficiency is less about the metal’s inherent properties and more about the design of the panel and the insulation system. For example, a double-walled metal panel with an insulating core, regardless of whether it’s aluminum or steel, will perform significantly better than a single-skin panel.
Furthermore, the color of the metal panel also influences its ability to reflect solar radiation. Lighter colors reflect more heat, reducing the amount absorbed by the building and thus improving energy efficiency.
Metal panels offer a sleek, modern look for luxury homes, but their high cost and potential for dents are drawbacks. However, a cohesive design approach considers both exterior and interior elements; for instance, the luxurious feel of metal can be complemented by using reclaimed materials inside, as explored in this article on designing with reclaimed luxury materials for interiors.
Ultimately, the pros and cons of metal panels depend on individual preferences and budget.
Insulation Systems with Metal Panels
Effective insulation is paramount when using metal panels. A common approach involves installing rigid insulation boards directly behind the metal panels. These boards, typically made of polyurethane or polyisocyanurate, provide a significant thermal break, minimizing heat transfer. The insulation is often secured with fasteners that also serve to hold the metal panels in place. In some cases, a continuous insulation layer is applied to the exterior sheathing before the metal panels are installed.
This creates a thermal barrier that reduces thermal bridging – the transfer of heat through structural components like studs. The effectiveness of the insulation system is crucial. A properly installed and adequately thick insulation layer dramatically reduces energy loss, making a significant contribution to the home’s overall energy efficiency. For example, using a high-R-value insulation system, like spray foam, in conjunction with a well-designed metal panel system can achieve significant energy savings compared to traditional cladding systems.
This results in lower heating and cooling costs and a smaller carbon footprint.
Fire Resistance and Safety
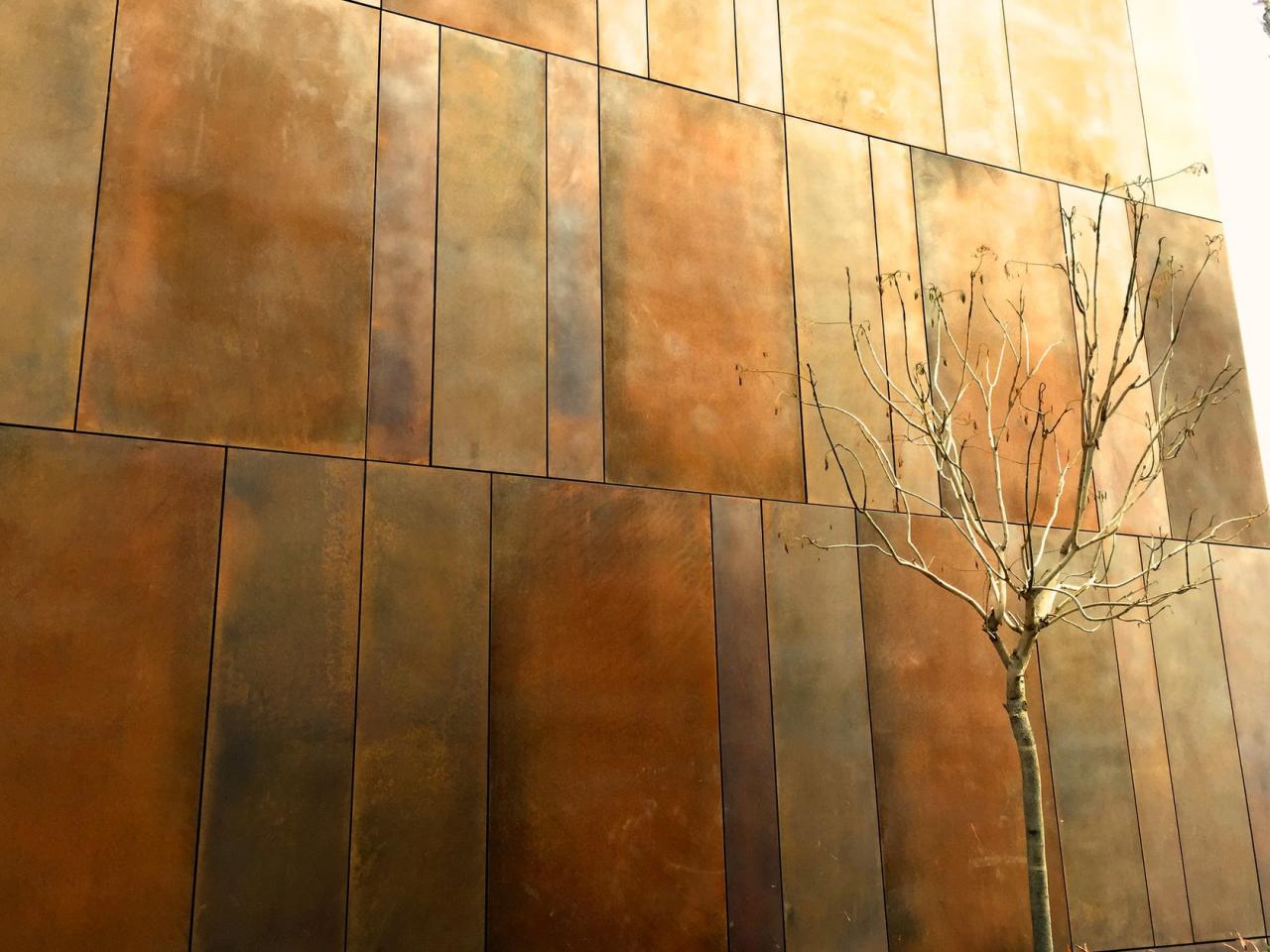
Source: architizer.com
Metal panels offer a significant advantage in terms of fire safety for luxury homes, providing a robust barrier against fire spread and damage. Their inherent properties and the way they are installed contribute to a higher level of fire protection compared to some traditional building materials.Metal panels, depending on their composition and construction, exhibit varying degrees of fire resistance.
The type of metal, its thickness, and the presence of any coatings all play a role in their overall fire performance. Steel, for instance, possesses excellent fire-resistant qualities, maintaining structural integrity at high temperatures for a considerable period. Aluminum, while not as strong as steel at extremely high temperatures, still offers a good level of protection and can be treated with fire-retardant coatings to enhance its performance.
The use of insulated metal panels (IMPs) further improves fire resistance by incorporating a non-combustible core material between the metal sheets.
Fire Resistance Ratings of Metal Panels
Metal panels’ fire resistance is typically assessed using standardized fire tests, resulting in ratings that reflect their ability to withstand fire exposure. These ratings often vary depending on the specific panel type, thickness, and the testing methodology used. While a direct comparison across all building materials is complex due to variations in testing standards and panel configurations, generally, metal panels achieve higher fire ratings than many combustible materials such as wood or vinyl siding.
For example, a properly installed steel panel system might achieve a Class A fire rating, representing the highest level of fire resistance, while wood siding often falls into lower fire-rated categories. This difference in fire resistance contributes significantly to the overall fire safety of a building.
The Role of Metal Panels in Fire Protection
Metal panels contribute to fire safety in several ways. Firstly, their non-combustible nature prevents them from igniting and contributing to the spread of flames. Secondly, their robust construction provides a physical barrier that can help contain a fire, slowing its progression and giving occupants more time to evacuate. Thirdly, the use of insulated metal panels (IMPs) adds an extra layer of protection by providing a thermal barrier that slows the transmission of heat, further reducing the risk of fire spread to adjacent areas.
The superior fire resistance of metal panels minimizes potential fire damage to the home’s exterior, protecting the underlying structure and interior spaces. In scenarios where a fire does occur, metal panel exteriors help limit the extent of the damage, potentially saving lives and reducing the overall cost of repairs.
End of Discussion
Ultimately, the decision of whether to use metal panels for your luxury home exterior hinges on a careful balancing of aesthetics, budget, and long-term considerations. While the initial cost and specialized installation might seem daunting, the potential for increased durability, lower maintenance, and enhanced energy efficiency can provide significant long-term value. By carefully weighing the pros and cons Artikeld above, and considering your specific needs and preferences, you can confidently choose the exterior cladding that best suits your vision and investment.
Expert Answers
What are the most common types of metal panels used for home exteriors?
Aluminum, steel, copper, and zinc are popular choices, each offering different aesthetic qualities and performance characteristics.
How long does it typically take to install metal panels?
Installation time varies depending on the house size and complexity of the design, but it generally takes longer than installing other materials like vinyl siding.
Can metal panels be recycled at the end of their lifespan?
Yes, most metal panels are highly recyclable, making them a more sustainable option compared to some other materials.
Are metal panels noisy in the rain?
Some types of metal panels can be noisy during heavy rain, although this can be mitigated through proper installation techniques and insulation.
How do I clean metal panels?
Regular cleaning with a mild detergent and water is usually sufficient. Avoid abrasive cleaners.