Comparing prices of natural stone veneer vs. manufactured stone for luxury homes reveals a fascinating interplay of aesthetics, cost, and longevity. The choice between these two materials significantly impacts both the initial investment and long-term maintenance for high-end residential projects. This exploration delves into the price differences, examining factors such as material sourcing, installation complexities, and the overall impact on a home’s value proposition.
From the initial cost per square foot, which can vary dramatically depending on stone type and origin, to the long-term expenses associated with maintenance and potential repairs, the decision requires careful consideration. We’ll analyze the visual appeal of each option, showcasing how their unique textures and colors can complement various architectural styles. Finally, we’ll also explore the environmental implications of each choice, considering sustainability factors for the discerning homeowner.
Initial Cost Comparison
Choosing between natural and manufactured stone veneer for a luxury home involves a significant financial decision. The initial cost, while a crucial factor, is only one piece of the puzzle; longevity, maintenance, and aesthetic impact also play vital roles. Understanding the price differences between these materials is key to informed decision-making.
The price per square foot for both natural and manufactured stone veneer varies considerably depending on several factors. These factors influence the overall cost of a project, making direct comparisons challenging without considering the specifics of each individual project. However, we can provide a general overview based on typical market ranges.
Average Price Ranges for Natural and Manufactured Stone Veneer
The following table presents estimated price ranges for natural and manufactured stone veneer in various luxury home markets. These are averages and should be considered estimates only; actual prices can fluctuate based on location, supplier, and specific stone type.
Material Type | Average Price/sq ft (Low) | Average Price/sq ft (High) | Price Variance |
---|---|---|---|
Natural Stone Veneer (e.g., Limestone, Granite, Slate) | $15 – $25 | $50 – $100+ | Significant; depends heavily on stone type, origin, and finishing. |
Manufactured Stone Veneer | $8 – $15 | $25 – $40 | Moderate; varies based on color, texture, and manufacturer. |
Factors Influencing Price Variations
Several factors contribute to the wide price range within both natural and manufactured stone categories. Understanding these factors allows for a more accurate budget projection.
For natural stone veneer, the type of stone is a major determinant. Rare and exotic stones like certain types of granite or imported marble will command significantly higher prices than more common options such as locally sourced limestone. The origin of the stone also plays a role; imported stones often incur higher costs due to shipping and import duties.
Finally, the level of finishing significantly impacts price. Highly polished or intricately carved stones are more expensive than those with a more rustic or natural finish.
Manufactured stone veneer price variations are less dramatic but still exist. The complexity of the mold used to create the stone, the materials used in the manufacturing process (cement, resins, etc.), and the level of detail in the texture and color all affect the final cost. Higher-end manufacturers often use superior materials and processes, resulting in a higher price point.
Examples of Luxury Home Projects
Consider two hypothetical luxury home projects: one using natural limestone veneer and the other using high-end manufactured stone veneer.
Project 1: Natural Limestone Veneer. A 5,000 sq ft luxury home utilizing high-quality, locally-sourced limestone veneer might cost approximately $20/sq ft for the material itself, totaling $100,000 for the stone. However, this doesn’t include installation, which can add a significant amount to the overall cost. The final cost, including labor and other related expenses, could easily reach $150,000-$200,000 depending on labor costs and the complexity of the installation.
The luxurious aesthetic of the limestone would justify this higher cost for many homeowners.
Choosing between natural and manufactured stone veneer for a luxury home involves careful budgeting. Natural stone often commands a higher price, but for a truly unique look, consider the sustainability angle; check out this article on designing with reclaimed luxury materials for interiors for alternative options. Ultimately, the price difference between natural and manufactured stone will significantly impact your overall project cost.
Project 2: High-End Manufactured Stone Veneer. The same 5,000 sq ft home using a premium manufactured stone veneer might cost $30/sq ft for materials, totaling $150,000. While the material cost is higher than a basic manufactured stone, the installation cost might be slightly lower due to the lighter weight and easier handling of manufactured stone. The total cost, including labor, might still reach $180,000-$220,000.
While the visual effect might not match the unique character of the natural stone, the savings in labor and potentially lower maintenance costs over time could be a significant factor for the homeowner.
Choosing between natural and manufactured stone veneer for a luxury home involves a careful price comparison. Understanding the cost differences is key, and a great resource for this is a broader look at luxury interior design materials cost comparison. This helps put the natural vs. manufactured stone veneer pricing into perspective when planning your budget for high-end finishes.
Ultimately, the best choice depends on your budget and desired aesthetic.
Long-Term Cost Considerations
Choosing between natural and manufactured stone veneer for your luxury home involves more than just the initial investment. A comprehensive assessment must include the long-term costs associated with maintenance, repairs, and the overall impact on your home’s value over its lifespan. Understanding these factors is crucial for making a financially sound decision.
The following sections detail the maintenance, repair, and resale value implications of each material over a typical 20-year period. We will explore how these long-term costs can significantly influence your overall investment.
Maintenance Requirements and Costs
Regular maintenance can significantly extend the lifespan and beauty of both natural and manufactured stone veneer. Neglecting maintenance, however, can lead to costly repairs down the line. The following Artikels the expected maintenance needs and associated costs for each material.
- Natural Stone Veneer: Natural stone, while beautiful, requires more diligent maintenance. Regular cleaning (at least annually) using a pH-neutral cleaner is essential to prevent staining and the build-up of grime. Resealing may be necessary every 5-7 years, depending on climate and exposure, adding to the long-term cost. This can range from $1 to $5 per square foot, depending on the sealant and labor costs.
Moss and algae growth are also common concerns, requiring occasional specialized cleaning.
- Manufactured Stone Veneer: Manufactured stone is generally easier to maintain. Regular cleaning with soap and water is usually sufficient. While it’s less susceptible to staining than natural stone, occasional power washing might be necessary to remove stubborn dirt. Resealing is typically less frequent and less expensive than natural stone, perhaps every 10-15 years, with costs potentially half that of natural stone.
Repair and Replacement Costs
Over two decades, the likelihood of needing repairs or even replacements increases. Understanding the potential costs associated with damage to each material type is vital.
- Natural Stone Veneer: Natural stone can be susceptible to cracking, chipping, and weathering, particularly in harsh climates. Repairs can be costly, involving sourcing matching stones (which can be difficult for unique varieties) and skilled masonry work. Replacement of damaged sections could range from hundreds to thousands of dollars depending on the extent of the damage and the accessibility of the affected area.
- Manufactured Stone Veneer: Manufactured stone is generally more resistant to cracking and chipping than natural stone. However, it can still be damaged by impacts or severe weather. Repairing or replacing manufactured stone is usually less expensive than natural stone due to readily available matching pieces and often simpler installation processes. Costs are typically lower, potentially ranging from tens to a few hundred dollars for smaller repairs.
Long-Term Value Retention
The choice of exterior materials significantly influences a home’s resale value. Both natural and manufactured stone can enhance curb appeal, but their impact on long-term value differs.
- Natural Stone Veneer: Natural stone is often perceived as a high-end, luxurious material, potentially commanding a higher resale price. However, the cost of maintenance and potential repairs should be considered. A well-maintained natural stone facade can significantly boost a home’s value, especially in affluent neighborhoods where buyers appreciate high-quality materials.
- Manufactured Stone Veneer: Manufactured stone offers a more budget-friendly alternative while still providing a sophisticated look. While it might not command the same premium as natural stone, its lower maintenance costs and durability contribute to a stable long-term value. In many markets, buyers recognize the quality and appreciate the lower upkeep associated with this material.
Aesthetic Considerations and Design
Choosing between natural and manufactured stone veneer for a luxury home involves careful consideration of the aesthetic impact. Both offer unique visual qualities and design flexibility, but their applications and overall effects differ significantly. The final choice hinges on the desired look, architectural style, and budget.
Natural and manufactured stone veneer each bring distinct visual attributes to a luxury home’s exterior. Natural stone, with its inherent variations in color, texture, and pattern, provides an unparalleled sense of authenticity and timeless elegance. Manufactured stone, while striving to mimic the look of natural stone, often exhibits more uniformity and predictable patterns. This can be advantageous in certain design contexts, but it may lack the unique character of its natural counterpart.
Texture, Color, and Pattern Comparisons
The differences in texture, color, and pattern between natural and manufactured stone are crucial to their aesthetic appeal. Natural stone offers a wide spectrum of textures, from the smooth polish of marble to the rough-hewn face of granite or the subtle variations of limestone. Color palettes in natural stone are equally diverse, ranging from warm earth tones to cool grays and even vibrant hues depending on the type of stone.
Patterns are completely organic and unique, with veining, striations, and other natural markings creating a visually rich surface. Manufactured stone, on the other hand, tends to have more consistent textures and colors within a particular batch, resulting in a more uniform appearance. While manufacturers offer a variety of colors and textures to mimic natural stone, the inherent randomness and unique characteristics of natural stone are often absent.
- Natural Stone: Highly variable textures (rough, smooth, pitted); wide range of colors and patterns; unique and unrepeatable.
- Manufactured Stone: More uniform textures and colors within a batch; patterns are often repetitive; designed to mimic natural stone, but lacks the organic variation.
Integration into Architectural Styles
Both natural and manufactured stone veneer can be successfully integrated into various architectural styles prevalent in luxury home design. However, their suitability might vary depending on the specific style and desired effect.
- Natural Stone: Its inherent elegance lends itself well to traditional, rustic, and Mediterranean styles. The rich textures and colors can enhance the grandeur of a stately manor or the rustic charm of a farmhouse. It can also be incorporated into modern designs for a touch of organic sophistication.
- Manufactured Stone: Its versatility makes it suitable for a broader range of styles, including contemporary and transitional designs. Its consistency and ease of installation make it a practical choice for larger projects or complex designs. However, it might be less appropriate for projects where the emphasis is on showcasing the unique character of natural materials.
Luxury Home Facade Designs, Comparing prices of natural stone veneer vs. manufactured stone for luxury homes
To illustrate the design possibilities, let’s consider three different exterior facades for a luxury home, each showcasing a different approach to stone veneer:
Facade 1: All-Natural Stone This design utilizes a combination of light-colored limestone for the main walls, accented by darker granite for window surrounds and a dramatic entryway. The varying textures and subtle color variations of the natural stone create a visually rich and sophisticated façade, perfectly complementing a traditional architectural style. The irregular shapes and patterns of the stones contribute to the home’s unique character.
Choosing between natural and manufactured stone veneer for a luxury home often comes down to budget. Natural stone tends to be pricier, but its unique character is a major selling point. To see what other high-end materials top designers favor, check out this article on top designers’ choices for luxury interior materials for some inspiration. Ultimately, the price difference between natural and manufactured stone can significantly impact your overall project cost, so careful planning is key.
Facade 2: All-Manufactured Stone This facade showcases a contemporary design, using a consistent manufactured stone with a smooth, clean finish. The chosen stone color is a warm, neutral gray, creating a sleek and modern aesthetic. The uniformity of the manufactured stone provides a cohesive look, highlighting the architectural lines and details of the house. This approach emphasizes clean lines and a streamlined design, reflecting a minimalist aesthetic.
Facade 3: Combination of Natural and Manufactured Stone This design blends the best of both worlds. The lower portion of the exterior features a rustic natural stone, such as fieldstone, to create a strong, grounded base. The upper levels are clad in a lighter-colored manufactured stone, providing a contrast and visually separating the levels. This combination creates a balanced aesthetic, combining the rustic charm of natural stone with the modern elegance of manufactured stone.
The contrast in texture and color adds visual interest and depth to the facade.
Installation and Labor Costs: Comparing Prices Of Natural Stone Veneer Vs. Manufactured Stone For Luxury Homes
Choosing between natural and manufactured stone veneer significantly impacts installation time and labor costs. Natural stone’s variability in size and shape, along with its often heavier weight, generally leads to a longer installation process and higher labor expenses compared to manufactured stone. Manufactured stone, with its consistent sizing and lighter weight, often allows for faster installation and reduced labor costs.
Choosing between natural and manufactured stone veneer for a luxury home often comes down to budget. Natural stone tends to be pricier, but its longevity is a key factor to consider. To fully understand the long-term value, it’s helpful to compare the durability of various luxury interior materials, such as you’ll find discussed in this article: comparing durability of various luxury interior materials.
Ultimately, the price difference between natural and manufactured stone needs to be weighed against their respective lifespans and maintenance needs.
Installation Time and Labor Cost Comparison
The following table provides estimated average installation times and labor costs per square foot for both natural and manufactured stone veneer. These figures are averages and can vary widely based on factors such as project complexity, accessibility, and regional labor rates. It’s crucial to obtain multiple quotes from experienced installers to get accurate pricing for your specific project.
Material Type | Average Installation Time (per sq ft) | Average Labor Cost (per sq ft) | Total Estimated Cost (Example: 100 sq ft project) |
---|---|---|---|
Natural Stone Veneer | 0.75 – 1.5 hours | $15 – $30 | $1500 – $4500 (labor only) |
Manufactured Stone Veneer | 0.5 – 1 hour | $10 – $20 | $500 – $2000 (labor only) |
Installation Challenges and Complexities
Installing natural stone veneer presents several challenges. The irregular shapes and sizes require more precise cutting and fitting, increasing installation time and potentially leading to material waste. The weight of natural stone necessitates stronger support structures and more careful handling, potentially requiring specialized equipment and expertise. In contrast, manufactured stone’s uniformity simplifies installation, minimizing cutting and fitting needs.
However, achieving a natural look with manufactured stone might require more attention to detail in terms of pattern and mortar application. Complex architectural features or tight spaces can increase installation difficulty for both types, leading to higher labor costs.
Specialized Tools and Techniques
Natural stone installation often involves specialized tools like diamond-blade saws for precise cutting, angle grinders for shaping, and pneumatic hammers for breaking larger stones. These tools add to the overall project cost. Experienced masons also use specialized techniques like dry-stacking or thin-veneer methods to optimize material usage and create a natural appearance. Manufactured stone typically requires less specialized tooling; however, tools such as a masonry saw, trowels, and levels are still necessary.
The cost of these tools, while less than those required for natural stone, should still be considered. The use of specialized adhesives and sealants for both types of stone also adds to the overall material and labor costs.
Deciding between natural and manufactured stone veneer for your luxury home involves careful consideration of budget. Natural stone tends to be pricier, but its unique character adds undeniable value. However, for smaller spaces, material choice is crucial, and you’ll want to check out this helpful guide on how to choose the right luxury materials for small spaces to maximize impact.
Ultimately, the price difference between natural and manufactured stone can significantly impact your overall project cost, so planning is key.
Sustainability and Environmental Impact
Choosing between natural and manufactured stone veneer for your luxury home involves considering more than just aesthetics and cost; the environmental impact of each material is a crucial factor. Both options have inherent advantages and disadvantages regarding sustainability, impacting energy consumption, carbon emissions, waste generation, sourcing, transportation, and end-of-life management. Let’s delve into a detailed comparison.
Environmental Impact Comparison
The environmental impact of natural and manufactured stone veneer differs significantly across several key factors. The following table summarizes the key differences:
Factor | Natural Stone | Manufactured Stone | Overall Assessment |
---|---|---|---|
Energy Consumption | High energy consumption in quarrying, transporting, and processing. | Moderate energy consumption in manufacturing, but often relies on fossil fuels. | Manufactured stone generally has a lower energy footprint, but this varies depending on the manufacturing process and materials used. |
Carbon Emissions | Significant carbon emissions from quarrying, transportation, and processing, particularly with long-distance shipping. | Moderate carbon emissions from manufacturing, transportation, and the use of cement (a significant carbon source). | Both have substantial carbon footprints, but the magnitude depends on sourcing and transportation distances. Locally sourced natural stone might have a lower carbon footprint than manufactured stone shipped from afar. |
Waste Generation | Generates significant waste during quarrying and processing, often with large amounts of unusable rock. | Generates less waste during manufacturing, but waste from packaging and potentially from manufacturing defects still occurs. Recycled materials can mitigate this impact. | Natural stone generates considerably more waste than manufactured stone. |
Sourcing and Transportation
Natural stone’s environmental impact is heavily influenced by its source and transportation. Quarrying can cause significant habitat disruption and landscape alteration. The distance the stone travels adds to its carbon footprint; locally sourced stone is more sustainable. Manufactured stone’s impact is also tied to transportation, but its manufacturing plants can be located closer to construction sites, potentially reducing transport emissions compared to long-distance natural stone shipping.
The use of recycled materials in manufacturing can further enhance its sustainability profile. For example, a manufactured stone producer utilizing recycled glass or industrial waste in their mix demonstrates a commitment to reduced environmental impact.
Durability and Recyclability
Natural stone is renowned for its exceptional durability, often lasting for centuries with minimal maintenance. However, its end-of-life management can present challenges. Disposal may involve significant costs and environmental impact. Manufactured stone, while generally durable, may not possess the same longevity. However, some manufacturers are exploring methods to improve recyclability by using more easily separable components in their products.
The potential for recycling manufactured stone remains a developing area, but it offers a pathway to reducing long-term environmental burdens compared to the more difficult-to-recycle natural stone. Ultimately, the long-term durability and recyclability of both options need careful consideration within a broader lifecycle assessment.
Final Review
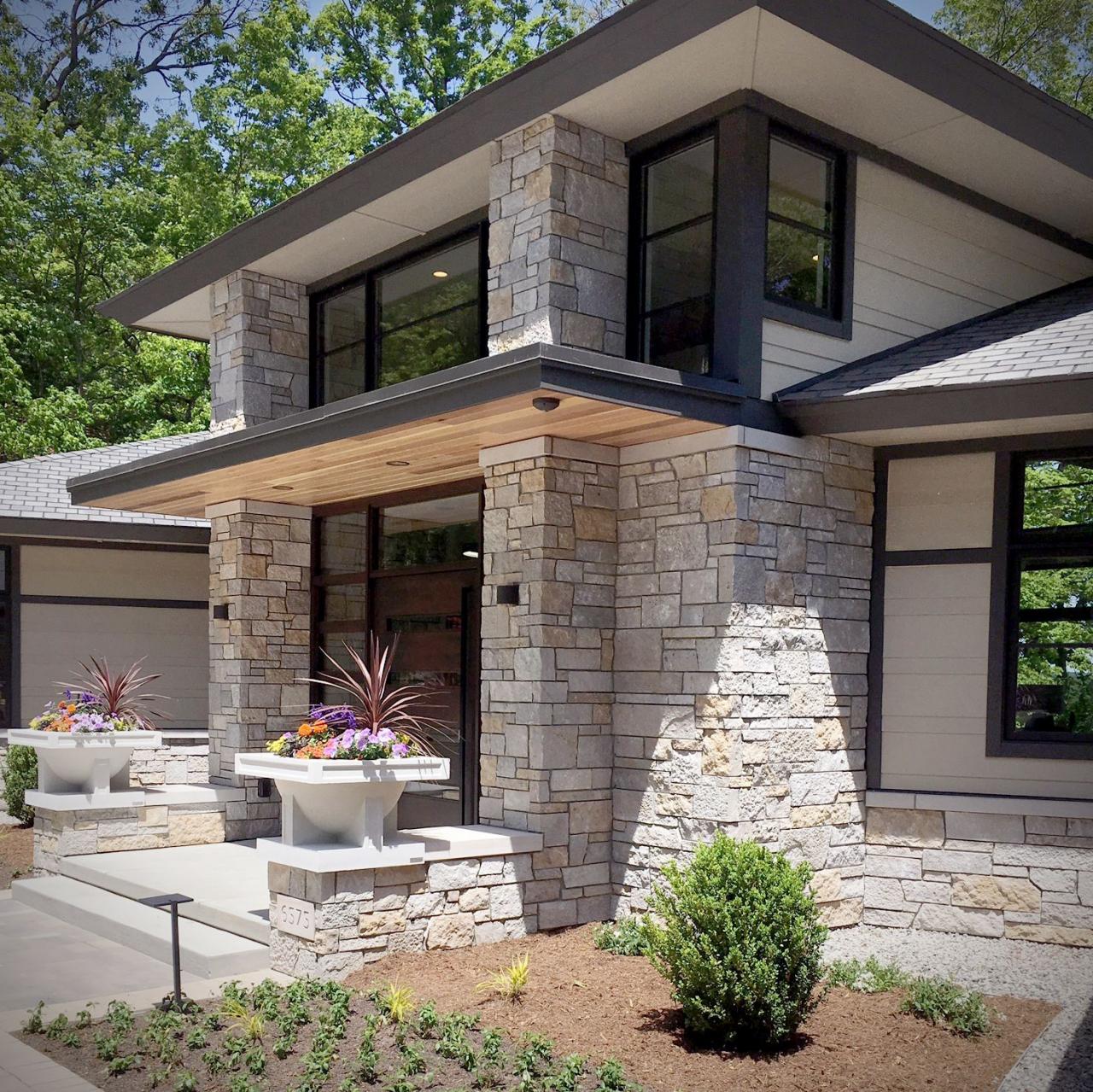
Source: pinimg.com
Ultimately, the choice between natural and manufactured stone veneer for a luxury home hinges on a careful balancing act. While natural stone often commands a higher initial price and requires more meticulous maintenance, it offers unparalleled aesthetic qualities and potentially greater long-term value retention. Manufactured stone provides a more budget-friendly alternative with comparable visual appeal and easier maintenance, although its longevity might not match that of natural stone.
By weighing the initial costs against long-term expenses, aesthetic preferences, and environmental considerations, homeowners can make an informed decision that aligns perfectly with their vision and budget.
Key Questions Answered
What are the typical warranties offered for natural and manufactured stone veneer?
Warranties vary widely depending on the manufacturer and supplier. Natural stone warranties often focus on material defects, while manufactured stone warranties may cover defects and sometimes even fading or discoloration. Always check the specific warranty details before making a purchase.
Can I mix natural and manufactured stone in a single project?
Absolutely! Combining both types can create unique and cost-effective designs. For example, you might use more expensive natural stone as an accent feature and manufactured stone for larger areas to control overall costs.
How does climate affect the choice of stone veneer?
Climate plays a significant role. In areas with harsh winters and frequent freeze-thaw cycles, certain types of natural stone may be more susceptible to damage. Manufactured stone, being more consistent in composition, can sometimes offer better durability in extreme climates. Consult with a professional to determine the best choice for your specific location.
What about insurance considerations?
Your homeowner’s insurance should cover damage to the stone veneer, regardless of whether it’s natural or manufactured. However, the specific coverage details might vary depending on your policy. It’s always advisable to review your policy and discuss any concerns with your insurance provider.